Supplies
What’s the best way to tie an apron
We recommend that you use a single loop version of a shoelace knot on your apron. This holds the apron shut securely while printing but also allows for easy removal with one hand behind the back.
Tell me how to put new adhesive on an old letterpress plate.
If you start to see gunk stuck in the adhesive (cat hair, human hair, your lunch crumbs, etc.), then it’s time to put new adhesive on your polymer plate. This should be a pretty easy process but does require a little muscle.
First, peel up the old adhesive to remove it. You’ll need some good fingernails to get between the adhesive and your plate. Since the adhesive holds onto the plate strongly, you can potentially kink the plastic backing if you’re not careful. We recommend that you lay the plate face down on a flat surface. Hold the plate down with one hand while peeling the adhesive off with the other. Try and keep the plate from flexing inordinately while you carefully tug the adhesive off the back of the plate. The adhesive might tear into pieces, but you can simply pull it up in strips.
Now, put on the new adhesive. If you have purchased a 12” x 18” sheet of adhesive, lay the blue release paper on a flat surface and have the brown silicone paper side face up. You will remove this silicone paper to show the sticky adhesive. If you have a roll of adhesive, pull out or unroll the adhesive so the sticky side is face up. When you first mount the adhesive to the plate, start with one side or corner of the plate and lay down the plate to the adhesive so that it makes as few air gaps or bubbles as possible. If the bubbles happen, work them out with your fingers or pierce them, through the back of the adhesive, with one prick of an Exacto knife or awl. You should be able to get all the bubbles out at this point.
If bubbles form underneath the plate when you mount it to the base, first try working these out to the edges of the plate with your fingers. If that fails, you can puncture the bubbles by sticking an Exacto knife through the BACK of the plastic backing of the plate (the blue side) to release the trapped air.
When do I replace my kreene in my platemaker? And how do I replace kreene?
Kreene, a flexible and matte transparent plastic, is used in a platemaker’s vacuum frame to hold films securely against photopolymer plates during exposure. But over time, it’s the nature of kreene to get wrinkled and lose flexibility. When you find that your kreene no longer creates a smooth seal, it’s time for a kreene replacement! At Boxcar Press, we replace our kreene every few days, but we process a lot of plates. With lower use, kreene can last for several months.
To replace your kreene: cut out a square of kreene to the size of the previous kreene piece (your kreene will be slightly larger than the grooves in the vacuum table). If your platemaker has one, pull the round bar out the previous sheet of kreene. Affix the new sheet of kreene to the bar with double-stick tape. Lay the kreene in position on the vacuum table and turn the vacuum on. Work out any wrinkles in the kreene so it remains flat. Using double-stick tape, affix the kreene edge opposite the bar to the vacuum table. You can then roll the kreene out over your vacuum table and start exposing your polymer plates. To increase the life of your Kreene, roll it out flat in your platemaker at the end of the day.
When do I replace my platemaker’s brushes?
A platemaker’s brushes wear out after prolonged use: these brushes should be replaced every 6-36 months. You can tell when a brush is tired out because the bristles are matted down. You can lengthen your brush life by keeping the brushes wet all the time and running your fingers through them to encourage the bristles to stand up. We sell replacement brushes for all of our platemakers: please e-mail or call us to order these.
How do I maintain the mounting rubber on my platemaker?
Magnetic mounting rubber and rigid mounting rubber come pre-sealed. Over time, this seal breaks down. You can make touch-up repairs with our green die sealer. Remove any old die sealer and apply green die sealer in a thin bead to the edge of the mounting rubber. Let dry overnight.
What are roller gauges and why do I need them?
Roller gauges are especially indispensable with a platen press. Letterpress rollers need to be positioned just right in order to deposit a thin film of ink onto the surface of the form, without squeezing ink over the edges. A roller gauge will help you accurately measure the height of your rollers so you can produce the crispest printing that your press is capable of. We sell roller gauges, precision ground to type high, which are also very fashionable.
When your rollers are positioned correctly, your printing will look beautifully crisp. But if your rollers aren’t positioned at the right height, your printing will have a halo effect: dark around the edges and/or chunkier/blotchier than it should be. If you ever notice ink on the back of your polymer plate or on your base — it’s a roller gauge emergency! Adjust your rollers now! We have a great video on setting roller gauge height in our Boxcar Training Videos and step by steps are listed here.
Step 1. While your press is inked up, remove the chase (on platen presses) or the base (on a Vandercook).
Step 2. We recommend checking the roller height in the four corners of the press bed. We’ll start in the upper right hand corner. Engage the form rollers and position them over the upper right corner of the bed.
Step 3. You will be pulling a stripe of ink on the round surface of the roller gauge. Pull the gauge underneath the form rollers so that a stripe of ink is transferred to the rounded surface of the gauge’s cylinder. Measure the stripe of the ink: you want your ink stripe to measure 3/32”. If the strip of ink is less than 1/16”, you’ll have difficulty consistently inking your plate (some areas will appear too light, and some areas will appear too dark). If your strip of ink is wider than 3/32”, your rollers put too much pressure on your plate and cause your printing to be chunky/blurry.
Step 4: On a platen press, to adjust the height of your form rollers: add tape to the rails that the roller trucks ride on. You may have to add several layers of tape. Strapping tape or plumber’s silver tape is frequently used for this. If you’re using a press other than a platen press, consult your manual as to how to raise your form rollers.
Step 5: Repeat steps three and four in each corner of your press bed.
Step 6: When your rollers are positioned correctly, you should pull identical 3/32” stripes of ink from the four corners of the press bed, and your printing should be both crisp and beautiful!
If you continue to notice inconsistencies in your inking after adjusting your roller height correctly, you may need to purchase new rollers and, if using a platen press, roller trucks as well.
When will I receive my order?
Photopolymer supply orders ship from our warehouse within 1-2 business days.
Custom Platemaking orders ship depending on the service you choose:
We offer a 1 business day turnaround, or Same Day Rush – an extra fee service.
For shipping in the USA, we offer UPS Ground, UPS 3 day air Service, UPS 2 day air Service, UPS Overnight morning, UPS afternoon Saver and UPS early Am (before coffee) 8:30 am service.
For International Customers, we offer US Postal Priority or Express Mail and UPS Worldwide Saver.
Remember that the days refer to business days and not weekends.
How do I know when my order has been shipped?
For platemaking, the day your order is completed (Order Complete) is the day your order ships. You will get a UPS tracking number via the log-in email on your account. Your invoice will be shipped in a separate email. Review your Order History to see all past and current orders for your status. For international orders using the US Postal Service, you will receive an email with your tracking number.
For Supplies – an email will be sent with the tracking number.
I need my order shipped today. By what time do I need to place the order?
For supply orders: Orders typically ship within 1-2 business days. If you need your order immediately, we encourage you to request expedited overnight shipping. However, if you’re in a serious letterpress emergency, please place your order before noon EST and mention that you’d like same day shipping. We’ll do our best to make it happen!
For platemaking: place your same day rushes by 1 p.m. EST.
Do you ship internationally?
Supplies: We ship supplies to Canada via UPS Standard or UPS Worldwide Saver and US Postal Service.
We ship international orders (outside of Canada) via UPS Worldwide Saver and US Postal Express Mail.
We think our online ordering system is pretty nifty but of course you can phone in your order to us by calling 315-473-0930. We love to talk to our customers.
Platemaking: We ship platemaking orders to Canada via UPS Standard or UPS Worldwide Saver and US Postal Service. We can ship Worldwide Saver to any international location or opt to use the US Postal Express Mail. These options are all at the click of a button through out platemaking site.
Printing: Yes, we love working with international clients and sending off printed letterpress beauties to destinations far and near.
Once my order is placed online, how do I make a change to it?
Supply orders: please call us or e-mail us as soon as possible.
Platemaking: First, log-in to see your order and check its current status. If we haven’t begun processing your order (STATUS – RECEIVED), you’ll be able to change your order details or upload files online. If we’ve already begun working on your order (STATUS – IN PLATEMAKING), please call us or e-mail us immediately, as you won’t be able to adjust your order online and we can see if the production process is already too far along. At this point, we can still change your shipping options and shipping addresses. If your status is BILLING COMPLETE, we will not be able to make any adjustments at this time.
How do I cancel an order?
For supplies, please call us as soon as possible to cancel your order. We will have to discuss refunds and crediting accounts as your online Supply Order has already been charged for payment.
For Platemaking – you can call us right away or you may be able to cancel your order online, if your status is still in RECEIVED or ON HOLD.
Log on to platemaking and you’ll see all current orders. Choose Complete Order to cancel your order. Confirm when it asks if you want to proceed. Your order status will reflect Order Cancelled.
The option to cancel is not available once we move your ticket into platemaking production. Cancelling after this step may incur some production costs. Please call us right away to minimize those costs, if possible.
If I purchase unexposed photopolymer, do I need to purchase adhesive too?
It depends on the plate. If you’re purchasing unexposed plastic-backed plates, you’ll need adhesive to adhere the plate to your printing base. We sell adhesive in 12×18 sheets and 27 yard rolls. Apply to the back of the plate after processing. If you’re purchasing unexposed steel-backed plates, there’s no need to purchase adhesive. Adhesive is included if we process the plastic-backed plates for you.
How often must I change the adhesive on my polymer plates?
As long as you’re careful about not getting dust or debris on the adhesive, and you carefully replace the blue protective release paper after use, the adhesive on your letterpress plates should remain sticky for many years. Keep in mind that adhesive can always be inexpensively replaced.
How do I use a Stouffer Gauge to help process my plates?
Instructions for using the Stouffer Gauge to accurately figure out the exposure time for your photopolymer plates: The Stouffer gauge is a reusable piece of continuous-tone film that you should use to test photopolymer plate exposures. Place the Stouffer Gauge in contact with a 1” x 6” strip of plate material (after you peel off the plate’s protective plastic cover). Then expose the plate.
You’ll have to guess the first exposure time because that varies depending on the equipment that you use. Start with the exposure time listed on your plate’s tech data sheet. For exposure times, please keep in mind that these times are for commercial photopolymer platemaking equipment. Any alternative photopolymer platemaking devices may have very different times and you’ll have to experiment more to find your ideal time.
Also check the plate’s tech data sheet for the Stouffer value you’re trying to hold during exposure. For example, the 94FL has a Stouffer value of 18. Make sure that the exposure used with the Stouffer Gauge hardens the plate for all the numbers up to and including #18. If you goal is #18, and #19 and #20 start to harden during your exposure time, then your exposure time is too long– decrease the exposure time. If your goal is #18, and #17 hardens but #18 washes out on the test plate, then increase the exposure time.
You most likely will have to expose several different test plates at several different exposure times to find the perfect exposure. Since the Stouffer gauge is small, you won’t waste much plate material in the process.
Platemaking
How can I check the progress of my order?
Log on to your account in platemaking. It will take you to your Orders page where the current status will be visible.
Status Explanations:
- Pending – Your order has been started but all the steps have not been completed. This requires further action on your part.
- Received – Waiting for us to review your files.
- On hold and awaiting action on your part.
- On Hold No Files Received – Please try uploading again or call for assistance.
- On Hold Bad Files – Your files need attention. You will receive an email indicating your order is on hold with the problem and asking you to correct and upload new files. File errors may include your files measure too large to plate, not in correct color mode, lines or dots too thin, files are in grayscale, etc.
- On Hold – Credit Card declined or expiration is passed. There is a problem with your payment, please contact us.
- In Platemaking – We are in production making your films to make plates. Your ticket is locked as we are moving ahead.
- Billing complete – Your platemaking job is billed and awaiting shipping.
- Shipping Complete – We have shipped and still need to Invoice your order.
- Order Complete – We closed out your order as we have created a shipping label and your package is out the door. The day your order was completed was the day it shipped.
How do I get my rewards from Plate Club
Your rewards and savings are automatic. This discount is applied to every order for the current year. The details page of your job ticket will reflect this discount with the dollar amount identified in your billing details. The type of discount – Plate Club – will be shown. Your emailed invoice will also have a line item with your Plate Club discount. All of your orders are also adding to your new square inch total for membership in the next year.
If I’m eligible for Plate Club, do I need to do anything?
No action is needed. The platemaking system is keeping track of your square inches. Your Plate Club discount is applied to your billing total on every job ticket for the year. No fuss, no muss.
How do I see my growing total of square inches?
Click on your Account Page when logged into boxcarpress.com. There will be a section near the bottom of your account page called “Platemaking Usage”. This is where you can find the current tally of square inches plated (as well as a date of this accrual).
What is the Plate Club?
Plate Club is a new rewards program offered by Boxcar Press that provides a 5% discount for platemaking customers whose orders totaled more than 7,500 square inches in the past year. Eligible orders are for the period from January 1 to December 31st. If you ordered more than 7,500 square inches of processed plate material last year, you will automatically be enrolled in the Plate Club. Membership eligibility recalculates at the beginning of each calendar year (January 1st).
I heard I can process letterpress plates myself with a UV box and a washout brush. What should I know about processing plates myself like this?
Platemaking can be an interesting process for the adventurous with some research and experimentation. If you plan on processing your letterpress plates by hand, know that the most challenging part is having a good source for your film negative. The density of the black part of your negative must be high enough to block out any extra light through the film. Photographic film works best for this. Try the light test. Hold up your negative to the light, you should NOT see the the bulbs or any light shapes through the black part of your “film”. If you see the outline of light, that means some light will filter through during exposure. The more light seeping through, particularly at the edges of the clear parts of your negatives means you lose some of the crispness of your exposure. If you use transparencies for your negatives, you will likely see some light as the density is not as strong as photographic film. One solution for a more rich density of black is to lay two transparencies on top of each other. You will have to decide how much light is acceptable for your project. Your light source / UV box should also have steady light from different angles on the top of the plate for strong, well formed relief.
Another part of good plate processing is a good washout. When you do it by hand, you will need a very soft handheld brush but beware, because handheld brushes are small and washout times frequently are over 10 minutes per plate (and that’s you moving a small brush with constant motion for 10 minutes in room temperature water). With this much exposure to water, you will have to keep an eye on the plate. The substrate material that holds the polymer on the back of the plate can start to break down after long times in the water. This causes loss of detail because the plate can soften too much and may come apart in the water. Text is one of the hardest things to consistently process on homemade units, and we all love text, right? The learning curve for processing quality plates can take time. Lastly you will need a drying /heat source. Do some research to assemble all your tools for the greatest success.
An alternative to hand processing your plates is using a professional plate processor service like Boxcar Press. We’ll provide you with quality plates every time, and we guarantee our plates will cause you no hassles or loss of detail on the press.
Or you can consider purchasing a professional platemaking machine if budget and your time allows. These machines are expensive but they are also convenient, allowing you to have your plates ready immediately. Make sure to ponder if you have the time, staff and energy to be making your own plates, or if you’d rather focus on your printing instead.
It’s a Crazy Friday and I have to print over the weekend. Can you help?
We can help! Get your files into us by 1 p.m. EST on Friday (and make sure your design files are prepared just right!). Choose our rush service which means we’ll ship your plates Friday. Choose overnight AM for shipping and Saturday delivery and you’ll have your plates in hand by Saturday, noon. Hooray!
How do I add crop marks when I am submitting files for custom platemaking?
There are two ways to create crop marks in Illustrator.
In Method 1, first create a rectangle by using the Rectangle (or Marquee tool (M)) in your standard tool palette located on the left-hand side of your screen. Create the rectangle so that the box size is your piece’s final trim down size (e.g such as 5.5″ x 7″ for an invitation, etc). Next, while the rectangle is still selected, drag it to its proper position over the artwork. Crop marks will be created outside the corners of the box.
In CS4 or newer, select EFFECT>Crop Marks to create the correct type of crop marks in Illustrator. In CS3 or older, select FILTER>Create>Crop Marks.
In Method 2, If you created your design in illustrator and set up your artboard to measure the finished size of your printed piece, any crop marks created will be outside the artboard. You will need to save your file with an eps extension so the crop marks will be included. You may then save the file as a PDF and send us either EPS or PDF. Avoid saving as an AI extension, the crop marks will be left off outside your artboard and not included in the file.
While using Adobe InDesign, you will need to create the crop marks manually by creating line segments via the LIne Tool (L) to delineate what your trim down size.
Please note that your crop marks are considered line objects and must meet your plate type’s minimum line thickness to be guaranteed to hold on your plate type (Link to What is My Minimum Line Thickness For My Plate Type?). If you need to thicken the line weight, you will need to expand the crop marks by selecting OBJECT>Expand or OBJECT>Expand Appearance.
Please note that we do not add crop marks to any file at Boxcar Press, as we do not know where or what your intended trim down size is.
How should I upload corrected files?
Sometimes we may notify you that your files have an error and need correcting. Follow the instructions to make those corrections and rename your file, preferably with the words “New”, “Revised”, or “Corrected” in the file name. Please don’t upload a changed file with the same name as the original file as we won’t be able to tell it’s a replacement and new file.
Re-upload new files to your current platemaking ticket. Log in to Boxcarpress.com with your username and password. Click on the applicable ticket to upload or drag and drop the new revised file.
You can only upload files to your ticket if your platemaking ticket’s status is either set as “Received”, “Pending” or “On Hold”. We will see new files and get to work to process your plates.
If you find that your ticket’s status is “In Platemaking”, you will need to call us at 315-473-0930 to see if it is possible to still add corrected or revised files.
If your ticket status is “Billing Complete”, “Order Complete” or “Shipped”, your ticket is unable to be altered.
Do I send my files reversed for your processing?
No. Please send your artwork and text right-reading as you want it to appear as the final print. We will make a film negative here at Boxcar Press for you. However, if you are planning to use your files in a different process than printing, please call us to discuss how best to prep your files.
Can you explain how you calculate the file dimensions for billing
Here is how we compute dimensions – we gang all your files up together and draw a box around the “black” part – the images and text. Now we know the length and the width. We multiply these two numbers together and this is your square inches total. We then multiply this square inch number by your square inch price of $0.62/sq inch or $0.67/sq inch.
Example:
9″ x 8″ is your “black part”
9” x 8” = 72 sq inches x $0.67 = $50.40
If your file has crop marks, we measure outside the crop marks. So if you don’t need crop marks, consider leaving them off to save a little cash.
Can you explain the same day rush service and fee?
Boxcar Press has a pretty fast platemaking turnaround service with our one business day turnaround. But if you have an even greater need for speed, consider our Same Day Rush Service. If you create your job ticket, upload your files before 1 pm EST, and choose Same Day, we’ll get your files out the door to arrive the next Business Day via UPS. Of course, speed comes at a price, the fee for Same Day Rush starts at $45 or 40% (whichever is greater) plus the regular cost of the plate plus your overnight shipping costs. Your minimum cost for a Same Day Rush plate is $75 before shipping and goes up from there.
So, we encourage you to make use of the one day turnaround as much as possible. Create your job ticket and upload your files before 5:30 pm EST and we’ll ship on the next business day, assuming your files are in tip-top A1 shape. File corrections may delay your shipping.
Do I send my files to size or scaled down?
You will need to send your files at 100% scale. We do not resize, scale up or down, or rotate any artwork. We highly recommend using the ruler feature available in Adobe Illustrator, Photoshop and InDesign to check your work to see if it is the size you want.
When exporting a PDF from Adobe Illustrator or Adobe InDesign, please double check to make sure it is the correct size by either re-opening it in Illustrator or placing it in InDesign to check the actual dimensions of your file. In InDesign you can use the Rectangle Frame tool to draw a box around your images/text to measure.
In Photoshop, use the Image Size tool to check your size. Saving your file as a .TIF locks your image size.
How do I take advantage of the free 2 day shipping?
Boxcar Press offers free two day shipping for platemaking orders that are over 120 square inches as of August 15th, 2014. If your order qualifies, this option will appear as the default shipping choice.
Please remember these details about this service:
- Two day service is ground service for those already within our 1 or 2 days service area (New York state, the Northeast to Maine, down to Virginia, and parts of Wisconsin, Illinois and Kentucky).
- If your usual UPS ground is 3 day – 6 days, you will receive UPS 2 day Air.
- If you have selected any overnight air services for shipping, we will NOT downgrade for free 2 day service. We will believe that you really need the faster overnight service.
- If you really do need 2 day Air service, please choose the 2 day Air and don’t wait for us to upgrade you from ground or a slower service. It’s hard to make UPS deliver faster once it’s out for shipping.
- Free 2 day air applies to business days and not Saturday delivery.
What’s the best way to tie an apron
We recommend that you use a single loop version of a shoelace knot on your apron. This holds the apron shut securely while printing but also allows for easy removal with one hand behind the back.
How do I cancel an order?
For supplies, please call us as soon as possible to cancel your order. We will have to discuss refunds and crediting accounts as your online Supply Order has already been charged for payment.
For Platemaking – you can call us right away or you may be able to cancel your order online, if your status is still in RECEIVED or ON HOLD.
Log on to platemaking and you’ll see all current orders. Choose Complete Order to cancel your order. Confirm when it asks if you want to proceed. Your order status will reflect Order Cancelled.
The option to cancel is not available once we move your ticket into platemaking production. Cancelling after this step may incur some production costs. Please call us right away to minimize those costs, if possible.
Once my order is placed online, how do I make a change to it?
Supply orders: please call us or e-mail us as soon as possible.
Platemaking: First, log-in to see your order and check its current status. If we haven’t begun processing your order (STATUS – RECEIVED), you’ll be able to change your order details or upload files online. If we’ve already begun working on your order (STATUS – IN PLATEMAKING), please call us or e-mail us immediately, as you won’t be able to adjust your order online and we can see if the production process is already too far along. At this point, we can still change your shipping options and shipping addresses. If your status is BILLING COMPLETE, we will not be able to make any adjustments at this time.
Do you ship internationally?
Supplies: We ship supplies to Canada via UPS Standard or UPS Worldwide Saver and US Postal Service.
We ship international orders (outside of Canada) via UPS Worldwide Saver and US Postal Express Mail.
We think our online ordering system is pretty nifty but of course you can phone in your order to us by calling 315-473-0930. We love to talk to our customers.
Platemaking: We ship platemaking orders to Canada via UPS Standard or UPS Worldwide Saver and US Postal Service. We can ship Worldwide Saver to any international location or opt to use the US Postal Express Mail. These options are all at the click of a button through out platemaking site.
Printing: Yes, we love working with international clients and sending off printed letterpress beauties to destinations far and near.
I need my order shipped today. By what time do I need to place the order?
For supply orders: Orders typically ship within 1-2 business days. If you need your order immediately, we encourage you to request expedited overnight shipping. However, if you’re in a serious letterpress emergency, please place your order before noon EST and mention that you’d like same day shipping. We’ll do our best to make it happen!
For platemaking: place your same day rushes by 1 p.m. EST.
How do I know when my order has been shipped?
For platemaking, the day your order is completed (Order Complete) is the day your order ships. You will get a UPS tracking number via the log-in email on your account. Your invoice will be shipped in a separate email. Review your Order History to see all past and current orders for your status. For international orders using the US Postal Service, you will receive an email with your tracking number.
For Supplies – an email will be sent with the tracking number.
When will I receive my order?
Photopolymer supply orders ship from our warehouse within 1-2 business days.
Custom Platemaking orders ship depending on the service you choose:
We offer a 1 business day turnaround, or Same Day Rush – an extra fee service.
For shipping in the USA, we offer UPS Ground, UPS 3 day air Service, UPS 2 day air Service, UPS Overnight morning, UPS afternoon Saver and UPS early Am (before coffee) 8:30 am service.
For International Customers, we offer US Postal Priority or Express Mail and UPS Worldwide Saver.
Remember that the days refer to business days and not weekends.
I want to use photopolymer to do something other than letterpress printing. How do I know what plate to use?
While our troubleshooting only extends to using photopolymer plates for letterpress printing, there are literally dozens of other uses for photopolymer plates. If you know the tech specs of the plate that you need, or if you can send us a sample of the plate required for your application, we would be happy to try and recommend a plate that we have in stock that will work for you.
We have innovative people using our plates for metal clay jewelry making, translucent porcelain, and leather work. We always like to hear what you want to try.
How do I know what plate type to choose?
This depends on the type of base you own. See the plate choices part of our web site for more information! In general, you will choose a plate with two things in mind, your base system (Boxcar or Magnetic) and your printing press. Our plastic backed plates correspond to a particular Boxcar Base and steel backed plates will correspond to either the Patmag or Bunting base.
If you are using one of the Do It Yourself home letterpress systems, we suggest the KF152 plastic backed plates.
If you are using an etching press, call us and we’ll suggest a plate, based upon a few questions about your setup.
As you are likely hand inking with these last two presses, please remember to ask us to SEND STRIPS in your platemaking order. They will be very helpful with your inking brayer for an easier inking.
How large can my file be while uploading?
The largest size, data-wise, that we accept is 26MB. If your file’s data size is larger than this, determine if it can be broken up into two or more files. If you actually have a large file in MB but not in inches, check to see if your images could be saved again in Photoshop with LZW compression and placed again into your document. This great compression feature will make your files more manageable.
For alternate electronic ways, we highly recommend compressing the file down with a program such as StuffIt or ZIP. There are also many numerous online free File Transfer Sites, such as YouSendIt.com or DropBox.com, that let you upload a file and send a link for Boxcar to download.
We will also always take your files on CD by mailing to: Platemaking Department; Boxcar Press; 509 W. Fayette St. #135; Syracuse, NY 13204.
Is there a checklist for me to review with my files before submitting to platemaking?
To ease file prep woes and to ensure a smooth production transition from file to plate, it is a great help to all to give your files one last review before submitting them. The first few things to make sure is that your file’s artwork is set to the right dimensions, that you’ve checked your artwork to make sure all plate type line minimums are met, that your file is in the proper color mode or image mode and that your file is in the proper file format and extension.
When working with a file that requires multiple colors for separations, please make sure all objects are assigned to their appropriate Pantone swatch or spot color. Adobe Illustrator and InDesign are excellent programs for setting up and checking such files.
Please also remember to check out any other file prep questions to answer any unresolved questions that you may have.
Should I gang up my images/smaller files into one larger file?
If you are ordering printing from us, no. Please send individual files and we will set up for most efficient production in our shop.
If you are ordering plates and doing your own printing, yes! By ganging up the plate yourself, you have more control over the margins and gaps between the ganged up artwork. Between each individual piece, we recommend .375” for plastic-backed plates and .5” for steel-backed plates. Our negatives come out of the imagesetter in 18″ strips, so ganging up onto a 17” wide strip, and up to max 22” long, is the most economical way to make negatives. Since we like to keep our maximum plate size at 17 x 22, please break larger files into two files.
That said, if you were to send us many individual files, we’d gang up the pieces in the most cost-effective manner. If you’re using plastic-backed plates, after we gang up your files, we’ll ship your job as a single plate and you can trim them easily yourself, using scissors or an Exacto.
If you’re using steel-backed plates and we gang up your files for you, we’ll ship your job as a single plate, unless you provide a cutting diagram for us. If you are submitting a ganged up file, keep in mind the fingers of our employees who have to trim your metal plates and leave us enough room around your text/images to hold the plate safely while we cut.
What programs do you support?
Our favorite ways to receive files for letterpress platemaking are by you sending us a press-ready PDF file (with fonts embedded) for platemaking. This PDF will serve as both your hard copy and your plate file. No additional faxing or email needed.
Our second favorite way is for you to send an EPS or AI file for platemaking. We also accept PDF digital files in current versions of other major design programs (i.e. Quark, InDesign, Freehand).
If you are creating your files in Photoshop, we like to say that this program is good for images but not so great for text. It’s best to convert your grayscale images in Photoshop and place them into Illustrator where you will add your text. If Photoshop is your only option, start with a file that is 600 dpi minimum so you can minimize the pixelation of your text when you convert files. More on file conversion to Image Mode of Bitmap under File Prep Tips. We prefer tif files from photoshop for upload.
Note, we can often make plates from PDFs created from Word files, however, Word is not able to format your file exactly the way we need. So please tell us your file was originally a Word document so we can anticipate and make corrections. If you are designing in Word, we suggest that you don’t use any funky or crazy fonts we won’t have access to. Oftentimes, they will just print as strange characters. Your images placed in Word will usually require some corrections too. You can email your files to plates@boxcarpress.com for an evaluation first and we’ll advise on how letterpress friendly it is.
What’s the largest size plate you can make?
For the 94FL, KF95, KF152, and 152SB plates, the largest size plate we can process is 17.5” x 22.5” (where your image area is 17” x 22”). For all other plates, the largest size plate is 16” x 22” (image area is 15.5” x 22”)
Photopolymer
What do I need to be able to letterpress print with your photopolymer plates?
You’ll need:
- a printing base. The polymer plates we create aren’t type high by themselves. They need to be mounted on a base to make a type-high printing surface. We recommend our Boxcar Base system. Letterpress printers also use magnetic bases from Patmag or Bunting. If you are printing on a DIY press such as L Letterpress, please refer to this tutorial.
- a Printing press. Remember that most letterpress printing presses people purchase will not be ready to print beautifully right away and a little tender loving care will be needed. Be prepared to purchase new rollers or do other maintenance on your press!
- Ink. we recommend Van Son rubber-based letterpress inks, which you can order in any uncoated Pantone number! Or you can purchase the Van Son base colors and mix your own colors. View the inks we carry.
- various pressroom supplies, including printers furniture, quoins, tympan paper, type gauge, ink knife and (if using a platen press) Kort gauge pins or Henry gage pins.
- a fashionable printing apron
We now sell letterpress starter packs, which contain a lot of what you’ll need to get started.
What’s the biggest problem that printers new to photopolymer encounter?
Photopolymer plates offer an way to letterpress print extremely detailed designs with a deep heavy impression (or a kiss impression if you’re so inclined). The chief problem that new photopolymer users encounter usually deals with roller height/roller condition. But no worries! Unlike larger problems like war or global warming, roller issues do have concrete and relatively easy solutions. We recommend rubber rollers and, if using a platen press, solid trucks. If switching from lead type/magnesium plates, you’ll want to keep a much closer eye on your rollers. You may find our general printing FAQ’s useful, especially if you’ll be using a Boxcar Base.
How many impressions can I get off a plastic-backed photopolymer plate?
If you take care of them, the plates will last for as many impressions as you need them (or for years of use). Plastic-backed photopolymer, in commercial applications, lasts for thousands of impressions – the plastic is incredibly hard and durable. Read about how to take care of your polymer plates.
I have a Boxcar Base. What plates do I purchase?
Standard Boxcar Base users: We offer 3 different plate types for the Standard base. A popular plate type is the Jet 94FL. If you are using the plates for a long period of time, this plate resists curling and brittleness the longest. Another option is the KF95 plate. However, some printers find they prefer printing with our hardest plate – the Jet 94 Clear (94CHFB). The harder plate has the least compression when printing, and gives less distortion than the 94FL on type smaller than 8 points. However, the 94 clear plates do get brittle in as little as 3 months so they are best for short term or limited use jobs. All 94/95 plates are the same price per sq inch for our platemaking service.
Deep Relief Boxcar Base users: The KF 152 plates work with our Deep Relief Boxcar Base.
I have a Patmag base. What plates do I purchase?
For the Patmag base user: we recommend the 152SB plate for most letterpress printers. Some printers find they prefer printing with a harder plate, the 145HSB. This harder plate gives less distortion than the 152SB on type smaller than 8 points or on thin lines. However, the 152SB holds slightly better detail. The 145HSB plate is a little less flexible than the 152SB and may crack if flexed too much on the magnetic base.
I have a Bunting base. What plates do I purchase?
For the Bunting base user: the Bunting Base can be any height, but typically, the bases pair up with the 152SB or (less often) the 94SB. Bases that measure .858” use the 152SB. Bases that measure .880” use the 94SB. Use a micrometer or calipers to measure your base. You can also send in a polymer plate that’s worked on your Bunting Base in the past, and we can match it up to the appropriate plate.
I want to use photopolymer to do something other than letterpress printing. How do I know what plate to use?
While our troubleshooting only extends to using photopolymer plates for letterpress printing, there are literally dozens of other uses for photopolymer plates. If you know the tech specs of the plate that you need, or if you can send us a sample of the plate required for your application, we would be happy to try and recommend a plate that we have in stock that will work for you.
We have innovative people using our plates for metal clay jewelry making, translucent porcelain, and leather work. We always like to hear what you want to try.
Is processing a photopolymer plate toxic?
None of the byproducts of processing photopolymer plates are known to have health risks, except if you’re allergic by contact to plastic. Check out the MSDS’s for more specific health information. You can find each plate’s MSDS on it’s product page: plastic-backed plates; steel-backed plates; intaglio plates.
How do I process my photopolymer plates?
Because processing your own plates can get complicated – and the results need to be excellent for quality letterpress printing – we recommend using a dedicated photopolymer platemaker. If you don’t already own one of these machines, we can help you source out light boxes, washout and exposure units, whatever your budget. If you’d rather learn how to hand-process your plates, we recommend checking out Letterpress Commons and, if you can, taking a class at one of these great book arts centers: Center for Book Arts (NYC); Minnesota Center for Book Arts; San Francisco Center for Book Arts; Columbia College Center for Book and Paper Arts (Chicago). You’ll find essential exposure information in your plate’s datasheets, though you’ll want to use a Stouffer Gauge to perfect exposure. We can always process your plates professionally for you through our platemaking services.
How do I process my intaglio plates?
Boxcar Press provides unexposed plates for intaglio and etching artists who want to create prints using a safer and more environmentally friendly process. Because we specialize in letterpress printing, we do not process intaglio plates at our shop. We can’t offer instruction on how to process these plates. But in an effort to assist artists with their intaglio process, we recommend the following books and web sites, written by people who are creating and experimenting with polymer in terms of correct UV exposure, wash out times, creating transparencies, homemade UV light boxes and more.
Overviews and Glossary
- Website – to identify the various printmaking techniques, with excellent close-ups (called Image Maps) and a glossary, – Print Room at the Spencer Museum of Art – University of Kansas
- Kenneth Tyler Printmaking Collection Glossary
Technique
- Instructional Outlines from State University at Buffalo, NY
- Animations demonstrating basic printmaking techniques on the Museum of Modern Art website. Includes a great glossary and recommended reading list.
- “Polymer Photogravure for More Photographic Intaglio Prints” by Jon Lybrook (new weblink)
- Non Toxic Printing – Intaglio Manual
- Non Toxic Printing – Instructional Videos
- World Printmakers – Technical Topics
- “Photo intaglio – an overview, ” Alternative Photography (new weblink)
- Intaglio Printing from Art Reflective
- ” Intaglio photogravure printmaking ” Alternative Photography (new weblink)
- Solarplate Etching how to
- “Possibilities of Polymer Photogravure,” by Kari Holopainen (new weblink)
- Videos on etching, lithography and relief printing – Caliornia Society of Printmakers
- Monoprinting / Drypoint
Instructions and Suppliers – Light Boxes, Brayers, Inks, Aquatints, Negatives
- Dan Burkholder’s “Making Digital Negatives for Contact Printing”
- McClain Printmaking
- Ultraviolet Light Box
- Pictorico – transparency film for photopolymer plates
- Renaissance Graphic Arts
- Video on making an etching press
- Building an Exposure Unit
- Intaglio Printmaking Equipment
Learn more with videos and books
- Video on Etching and Screenprinting – Chicago Printmakers Collaborative
- Intaglio: The Complete Safety-First System for Creative Printmaking: Acrylic-Resist Etching, Collagraphy, Engraving, Drypoint, Mezzotint By Robert Adam, Carol Robertson
- Etching and Photopolymer Intaglio Techniques, by Colin Gale
- Printmaking in the Sun, by Dan Welden and Pauline Muir (Amazon)
- Polymer Photogravure: A New Method for Photographers and Graphic Artists, by Taneli Eskola and Kan Holopainen
- Intaglio Printmaking (Printmaking Handbooks) By Mychael Barratt
Other links to useful and interesting Sites
- University Art Dept and Printmaking Directory – Bill Fisher
- Printmaking Links from Maryland Printmakers
- World Printmakers
- Zea Mays Printmaking Resources
We hope this information helps you in the process of what you’re trying to achieve. Please help us to spread the good news by letting us know about other useful sources.
I’m a metal clay artist. What photopolymer plates do I use?
We carry plates that are very similar to those recommended by Art Jewelry Magazine. Many metal clay artists have used our plates to great success. We have several plate types that will suit your needs and preferences.
Art Jewelry Suggests | Boxcar Press plate | Boxcar plate thickness | Plate material | Impression |
---|---|---|---|---|
0.8mm | 94FL | .94mm/.037” | plastic backed | shallower |
1.52mm | KF152 | 1.50mm/.060 | plastic backed | deep |
0.9mm or greater | 94SB | .94mm/.037” | metal backed | shallower |
0.9mm or greater | 145HSB | 1.40mm/.057″ | metal backed | medium |
1.52mm | 152SB | 1.50mm/.060″ | metal backed | deep |
Boxcar Press offers two options to metal clay artists. We can sell you unexposed polymer plates for do-it-yourself artists to create their own negatives and process themselves. Check out our new Plates by the Pound service for our plastic backed plates under our Supplies. Or we can take your digital files or images and professionally create plates for you, quickly and economically.
In either case, you will want to store your exposed plates in a zipper bag out of sunlight. You may also want to consider using a silicon spray to protect the plate from the moisture in the clay. You will want to clean the plate with vegetable oil. Exposure to too much light and moisture will cause your plates to deteriorate.
Remember, we’re a letterpress shop, and letterpress is our expertise. We can’t answer specific questions about how our plates work with your process, but we can offer information on the polymer plate material, thickness, exposure times, and processing.
For additional information, you may also want to check out:
- Metal Clay yahoo group: join this vibrant community of over 3,000 artists.
- Maggie Berman’s site features a great instructional article on using polymer plates for metal clay, PMC, or precious metal clay artists.
Do I need to order adhesive if I’m having a plastic-backed plate processed by you?
No! Any plate that will be printed on a Boxcar Base will have Boxcar film adhesive applied at no charge.
What’s the smallest size plate that I can print on my Boxcar Base?
The Boxcar Base is guaranteed to hold plates in register, provided they are standard thickness plastic-backed plates mounted with our film adhesive. But plates that are smaller than .25 square inches may drift under certain conditions due to their small area of contact with the base. Make sure your plates are larger than .5″ by .5″, even if your image is very small.
How are plastic-backed and steel-backed plates different?
When mounted on their appropriate bases, plastic-backed and steel-backed photopolymer plates both create type-high surfaces for letterpress printing. Both plate types are recyclable. We’ll talk about some of their differences below.
Plastic-backed polymer plates are flexible, transparent, easy to cut, and mount onto a Boxcar Base for simple registration. You’ll find these plates:
- can be cut with scissors in both their unexposed and exposed forms.
- are transparent, meaning you can see the Boxcar Base’s grid through your plate. This allows for simple alignment of your plates to your base: For perfect registration, align a certain element of your plate to the grid: take a horizontal or vertical element in your plate (this could be your registration marks, or a horizontal line in your artwork) and line it up to the grid.
- eliminate plate creep (steel-backed plate users sometimes experience this while on press). The plastic-backed plate’s adhesive is shift resistant, giving you a secure, strong hold during printing (but the adhesive also peels up easily when you’re done printing)
- allow printers to print two color jobs using one plate if the design elements don’t touch. Cut out the second color images/text with a craft knife or scissors and set aside. Print color #1. Set your second color images back in place and pull up the first plate for color #1—perfect registration!
- allow designs to be ganged up on plates closely to save space (and money).
- are reusable. You will be able to reuse the plate many times if you keep the adhesive protected with the blue overlay after printing. You can also replace adhesive for even more extended plate use.
- more prone to curling, especially with large solid areas over time.
- If purchasing unexposed plastic-backed polymer plates, you’ll also want to purchase film adhesive to adhere your plates to your base. If we’re making your plates for you, we include adhesive.
- are suitable for metal clay jewelry.
- Over here at Boxcar, we use plastic-backed plates for all our printing (the Jet 94 Clear plate paired with the Standard Boxcar Base).
Steel-backed polymer plates are compatible with magnetic bases, generally the Patmag or Bunting base. Steel-backed polymer plates:
- require cutting with a metal shear or heavy-duty trimmer. You can use tin snips, though you may end up with kinks in your plate, as tin snips won’t cut as cleanly.
- sometimes shift and creep on your base during printing. Magnets in the base effectively hold a plate from peeling but cannot always hold a plate from moving side to side. The cylinder or rollers of a press can move steel-backed plates out of register (that’s “plate creep”).
- are not transparent. Because magnetic bases aren’t gridded (and you can’t see through these plates), you’ll have to align your plates to your base with a line gauge and possibly registration marks. This works, but it is more time consuming and there’s more room for error.
- are rigid, meaning they don’t bend well. This inflexibility can cause plates to kink and warp when handled so that their corners may work up while on press. Steel-backed plates are, however, very durable and not prone to curling over time.
- can be more expensive than plastic-backed plates because you may require registration or crop marks which makes for a larger plate.
- are difficult to get on and off the base, especially when the base has inlaid magnets. When placing metal plates on a magnetic base, keep fingers clear so they don’t get pinched when the magnet grabs. When taking your plate off the base, try an ink knife to pry under the plates to release from the magnetic base.
- have sharp edges, which dictate extra care when handling.
- can be used for a wide range of printing and impression—on leather, metal clay jewelry, ultra heavy-weight paper stocks. Steel-backed plates can also be used on etching presses when relief printing is desired. They are not suitable for high temperatures of foil stamping though.
What’s the maximum size polymer plate I can print on my base?
Your maximum plate size is actually the size of your base — your photopolymer plates can go right up to the edge of your base. Obviously your relief images and text should not hang over your edge. This is true for both magnetic bases and the Boxcar Base. If you need a little more base for occasional projects, consider a Boxcar Base scrap to add that extra ½” – 1”. Read more about maximum base size.
General Printing with the Boxcar Base
Can I print lead type at the same time I’m printing polymer with my Boxcar Base?
Since polymer plates mounted on a base are type-high, there is nothing keeping you from printing type at the same time! Many printers will print a form that includes a smaller Boxcar Base with a polymer image design with metal or wood type combined around one or more sides of the base. This is a great use of both when you want to add an image.
Can I lock up two different Boxcar Bases and use them together?
Yes, you can certainly lock up two Boxcar Bases into one chase and print, and in most situations print a letterpress plate that spans the two bases. We inspect our Boxcar Bases and verify they are within plus/minus 0.001” in thickness, parallel and flatness. Still, we’d like your bases to be even closer in height than +/- 0.001″ if possible. Here’s how to do this depending on your situation.
- You purchase one base and have it cut into two pieces: use each piece individually or lock them both back up together for a larger base surface. Your two cut sides should match up perfectly. Slide them together and using quoins, furniture and leading, fill the chase on all sides around the two bases to support the pieces and have a good strong lock-up.
- You already have two different bases in your shop: These should be fine to print. There may be slight variation within the +/- 0.001″ tolerance, so find the two sides most similar in thickness and slide them together.
- You have a base. You want to purchase another base to print with at the same time: We keep detailed specs on each base we sell. When you order your second base, let us know your original base’s serial number—we’ll make sure the bases we ship to you are identical heights so you can butt them together and have a very even printing surface. Where do you find your serial number – on the bottom edge under the Boxcar text.
- You are going to purchase two bases to print with at the same time: Just let us know that you’re planning to print with them at the same time, and we’ll choose the two closest in height from our inventory.
I own both a Vandercook and a platen press – do you suggest that I buy two separate bases, the Deep Relief Base for the platen press, and the Standard Grid base for the Vandercook?
We suggest purchasing one type of base for both presses, so that your presses will be able to share the same plate. It really comes down to your experience: if you’re a new printer, go with the Deep Relief base. Setting roller height can be a longer adjustment process on platen presses and this base will be more forgiving as you work through this. If you can use a roller gauge in your sleep, and you have experience expertly adjusting your inking rollers on your C&P, go with the Standard Base. The Standard Base’s plates are less expensive per square inch as they are slightly thinner but all plates, when paired with the correct base, equal type high (.918) and that is the most critical factor.
If I have a 10 x 15 chase on my press, why can’t I use a 10 x 15 base?
We totally understand that you want to get the most use and space out of your press. However, knowing about some of the challenges you will face can help you make decisions about the correct size.
First, keep in mind that every press, like every person, has a limit to its strength. A press with a 10 x 15 chase will never be able to hammer a 10 x 15 block of text. You’ll be able to get a good impression using about 60-70% of your chase, depending on your form. Secondly, your base needs to stay put in your chase with a good lockup. To secure your base in your chase, you need to make room for the quoins plus furniture for distributing the weight of the base, and gauge pins. Gauge pins fit in the space outside the base and over the furniture.
We recommend checking out our Base Selection Chart which recommends the ideal size base for your chase. With a 10×15 chase, we would recommend a 9×12 base, for instance.
If you really want to max out the base size, keep in mind your base should be at least 1 inch, preferably 1.5 inches, smaller than your chase. If you use a lot of paper that is precut, it is most likely smaller than your base. This can make it challenging to place your gauge pins and still hold the paper and not hit the base. One safety note, the larger the base in your platen press, the further you have to reach into the press to place your paper. This is very important with a larger press with a motor, so take into consideration your comfortable reach, the speed of the press, and your fingers when locking up a larger base.
Why do I have ink on my Boxcar Base?
It’s important to keep the grid on your Boxcar Base clean so you can see its registration marks when printing. If your rollers ever lay ink down directly on the base’s surface, STOP! STOP! STOOOOOOOOOOOOOP! Don’t keep running the press because something is out of alignment. Then ask yourself:
- Are your rollers at type-high? Using a roller gauge, check to make sure your rollers are set for type-high printing material. The surface of the base is far below type high and should never come into contact with the rollers.
- Is your base flat in the press bed? Take a piece of onionskin paper and try to slide it between the base and the press bed – if the onionskin paper fits, one of the corners of your base is working up in the press. Frequently this is caused by tightening the quoins too much. Since the Boxcar Base won’t work up as easily as handset metal type or monotype, you don’t need to tighten the quoins quite as hard.
Still getting ink on your base? If, after checking the roller height and loosening the quoins, you still have problems with ink on your base – contact us and we’ll assist you in problem-solving further.
How do I know whether I should purchase a deep relief or standard base?
Here are our general guidelines for choosing between a deep relief or standard Boxcar Base:
For presses with cylinder inking systems, such as a Vandercook or a Heidelberg Windmill, where press adjustments for rollers are fairly easy to make, we suggest a Standard Boxcar Base (.875” thick).
For platen presses with rollers that run on rails and an ink disk system, such as Chandler and Prices, Goldings, Kluges, etc., where press adjustments for correct roller height takes longer, may have more steps, and can be a little trickier, we often suggest a deep relief base. Why? Many of the platen presses have rollers that are set too low and need quite a bit of taping on the rails to bring them up to type high. So if roller height is not correctly set, the rollers can hit the base or ink the standard base. The deep relief base is a thinner base (.853” thick) and while adjusting rollers and preparing makeready, the rollers usually won’t ink or hit this base.
Of course, there are exceptions to every guideline. If you are an experienced printer with skills in roller height adjustment, a standard base will be just fine for you. If you are already printing on a press with a standard boxcar base and are outfitting a new press, it is certainly easier to use (and remember) the same base and plates for all jobs. Roller height adjustment is the key to good printing regardless of press so this is valuable to learn regardless of your choice of Boxcar Base.
What’s the smallest size plate that I can print on my Boxcar Base?
The Boxcar Base is guaranteed to hold plates in register, provided they are standard thickness plastic-backed plates mounted with our film adhesive. But plates that are smaller than .25 square inches may drift under certain conditions due to their small area of contact with the base. Make sure your plates are larger than .5″ by .5″, even if your image is very small.
What happens if you use a Deep Relief Boxcar Base on a Vandercook, Heidelberg Cylinder, or Heidelberg Windmill–some info you need to know?
The Deep Relief Boxcar Base does work fine on cylinder presses or the Windmill — since its base + plates + adhesive still equals a type high surface (.918”) and that is the critical issue for all bases and plates. There is the advantage of holding a slightly finer line with a standard plate but let’s be realistic when we compare. The 94/95 plates will hold a 0.25pt line and the 152 plates will hold a 0.35pt line (when talking inches that is a .0035″ line compared to a .0048″ line. Not much to quibble about. We just like the way a 94 plate works on our windmills with our standard base and that is how we started years ago in the infancy of Boxcar Press. That said, some printers who use the Deep Relief base on their platen presses already may want to use the Deep Relief base on, say, their Vandercook too, so that both presses can share plates — this is totally okay too.
How do I measure the height of my letterpress base?
If you have a Boxcar Base – we can tell you the thickness of your base down to the ten thousandths of an inch. Just provide the 5-digit serial number on the bottom of your base below the base description and we’ll send you the dimensions.
If you want to measure your own base – we suggest a micrometer that measures to thousandths of an inch. Follow the directions that come with your micrometer, however, basically you will clamp your micrometer’s measuring rods around your base and tighten until it holds the base firmly and securely. Tightening too hard can cause an error in your reading. Read the measurement per the instructions for that micrometer.
Boxcar Bases are measured to the following heights:
Standard bases – .875” plus or minus .001
Deep relief bases – .853” plus or minus .001
If your base is .X” high, subtract that amount from type high .918 and you’ll get the height you want for your plates.
What’s the maximum size polymer plate I can print on my base?
Your maximum plate size is actually the size of your base — your photopolymer plates can go right up to the edge of your base. Obviously your relief images and text should not hang over your edge. This is true for both magnetic bases and the Boxcar Base. If you need a little more base for occasional projects, consider a Boxcar Base scrap to add that extra ½” – 1”. Read more about maximum base size.
How do I measure the size of my chase or press bed?
For cylinder presses without chases, such as Vandercooks:
bed width: the distance between the rails.
bed length: find the “dead lines” inscribed in your bed. There are two lines, one at the head of the press, one at the foot of the press. Measure the distance between those lines – that’s the length of your press bed.
You need to make sure that your base stays within those lines. If you put your base on the outside of either line, your cylinder grippers can smash it.
For presses with chases
A chase is an iron frame. To get the width and length of your chase, simply measure the INSIDE of the frame. The measurements may be rounded up to identify your chase size, for example, 4.95” x 7.875” will be called a 5×8 chase.
My chase is rocking while it’s laying flat (before I try any lockup!). What should I do?
First, figure out why your chase isn’t lying level.
- Possibility 1. Your chase might have cracked some time in the past then was welded to repair it. If this is the case, you may need to file or shave off any excess metal that might interfere with your chase being level.
- Possibility 2. You may have a low spot on your chase. You’ll want to add a shim (a small piece of metal) to the chase to level things off.
In either case, use a professional machinist. They can expertly grind down your chase if needed to create a smooth surface, or they can add a shim to your chase to level things out.
How do I decide whether I need registration marks for my print job?
First, let’s talk about what are registration marks. Registration marks print outside the trim area of printing. They can include bulls-eye targets, crop marks, plate information, etc. These marks allow the printer to accurately align separate letterpress plates for multiple color print jobs and better align cuts when trimming.
How do you tell whether you need registration marks for your job? If you are letterpress printing a job that has two or more colors that print up against each other or overprint each other, registration marks help you to set up each plate color for a close printing with minimal to no adjusting.
If you have a letterpress printing design with bleeds, crop marks are useful for a proper paper trim after printing.
If you are printing a design with scores and folding, having those marks designated outside your trim area is helpful for die cutting and finishing work.
If you are sending your letterpress printing project to another location for cutting and finishing, registration marks can be a very smart move for a successfully trimmed job.
If you just want guidelines for trimming, crop marks make a good template.
If you are adding registration marks to your plates, here’s how to use them to register your plate to your base: Plastic backed letterpress plates are see-through and you’ll be able to see and use your Boxcar Base grid lines for registering. Place a registration mark over a grid line at an intersection where two lines cross. This will be your same starting place for the registration marks on a second color plate.
File Preparation
When using Illustrator, how do I outline my fonts and why is it important?
Sending all your fonts packaged is not fail-safe: all needed fonts aren’t always provided, or all your fonts may not be recognized when we open your file, causing shifting and changes in your design. On the other hand, outlining fonts is fool-proof, safe, and ideal. So outline your fonts! In Illustrator, you do this by selecting TYPE>Create Outlines. This will automatically convert your text into vector shapes. Your type will temporarily look bolder and be highlighted in blue. Click on any white area of your file and it will look normal again.
Creating Vector Art with Live Trace
Creating vector art via the Live Trace function in Adobe Illustrator will convert a rasterized (e.g a pixel-based) graphic into a vectorized graphic (e.g artwork made up of vectors or small points). Using the Live Trace feature to convert your artwork ensures the crispest and cleanest plate possible, as well as allows scaling and transforming the artwork without losing data or composition clarity.
Depending on what type of artwork one is looking to convert to vector, a few considerations must be taken for best results. Pixel-based graphics, such as calligraphy and line art, should be converted to image mode of bitmap beforehand and have a higher resolution of 300-600. The more graphic, stark, and higher contrast an image is, the better the Live Trace result will be. Live Trace will not always work for all images but with practice, you’ll learn to recognize what images will work best with Live Trace.
First, open the file in Adobe Illustrator. Next, double-click on the image with the default (black) arrow tool until the Live Trace toolbar appears at the top of the Illustrator tool bar.
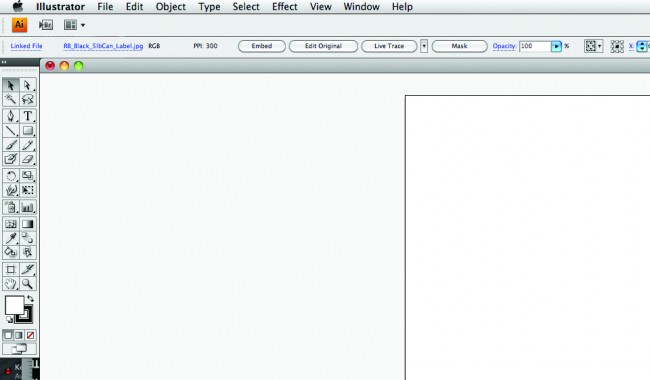
Live Trace Toolbar
Within the Live Trace toolbar in Adobe Illustrator, you have the ability to choose either between presets or experiment with different manual settings. The default is usually adequate for most purposes so click on Live Trace. The image will reshape and convert to 100% cmyk black. If you are satisfied with the conversion-to-vector on screen preview, then click “Expand” or “Live Paint” to immediately convert the file to vector. White and black anchor squares will appear on the Illustrator art board to denote the successful conversion. Click on your white artboard again to complete the trace.
Depending on the quality of the original pixel-based file and the desired effect in mind, Live Trace is a very powerful editing tool for scanned-in calligraphy and high-contrast line art.
How do I select spot colors in my file instead of CMYK?
Spot color or Pantone swatch colors can be applied to objects via the Pantone Swatch Color Book or Spot color library found in Adobe Illustrator. For Adobe InDesign, Spot Colors are more easily accessed. First, activate the Swatch palette by selecting WINDOW>Swatches.
Notice the fly-down menu icon in the upper right-hand corner of the Color palette? The icon looks like a small downward black triangle with four small lines next to it. Clicking on this will open a fly-out window menu. Hover your mouse over “Open Swatch Library” to open another fly-out window menu of all the color books. Very carefully move your mouse to hover over “Color Books”, which will open up another fly-out menu. You’ll see a lot of different color book options, but we recommend using “PANTONE solid uncoated”. Clicking on this color book will open a new window filled to the brim with a plethora of color
Swatches that Pantone has to offer.
Finally, assign all your file’s artwork, objects, and text to their appropriate Pantone Swatches or spot colors.
In Indesign, open the swatch window. click on the downward black triangle to the right and choose New Color. This opens a New Color Swatch Window. Select Spot as color type and Pantone Solid Uncoated as the Color Mode. The PMS colors will load for you to select and click OK.
How do I add crop marks when I am submitting files for custom platemaking?
There are two ways to create crop marks in Illustrator.
In Method 1, first create a rectangle by using the Rectangle (or Marquee tool (M)) in your standard tool palette located on the left-hand side of your screen. Create the rectangle so that the box size is your piece’s final trim down size (e.g such as 5.5″ x 7″ for an invitation, etc). Next, while the rectangle is still selected, drag it to its proper position over the artwork. Crop marks will be created outside the corners of the box.
In CS4 or newer, select EFFECT>Crop Marks to create the correct type of crop marks in Illustrator. In CS3 or older, select FILTER>Create>Crop Marks.
In Method 2, If you created your design in illustrator and set up your artboard to measure the finished size of your printed piece, any crop marks created will be outside the artboard. You will need to save your file with an eps extension so the crop marks will be included. You may then save the file as a PDF and send us either EPS or PDF. Avoid saving as an AI extension, the crop marks will be left off outside your artboard and not included in the file.
While using Adobe InDesign, you will need to create the crop marks manually by creating line segments via the LIne Tool (L) to delineate what your trim down size.
Please note that your crop marks are considered line objects and must meet your plate type’s minimum line thickness to be guaranteed to hold on your plate type (Link to What is My Minimum Line Thickness For My Plate Type?). If you need to thicken the line weight, you will need to expand the crop marks by selecting OBJECT>Expand or OBJECT>Expand Appearance.
Please note that we do not add crop marks to any file at Boxcar Press, as we do not know where or what your intended trim down size is.
How do I outline fonts?
While either in Adobe Illustrator or InDesign, select all your text that needs to be outlined using the black arrow tool (the default arrow tool). Next, select TYPE>Create Outlines. This will automatically convert your text into vector shapes. Your text will temporarily look bolder and be highlighted in blue. Click anywhere on your artboard that is white to deselect your text and its appearance will look normal again.
What file formats do you accept?
We prefer press quality PDF files and also accept Adobe Illustrator files and EPS files. (If sending an eps file please also send a pdf for reference.)
How should I upload corrected files?
Sometimes we may notify you that your files have an error and need correcting. Follow the instructions to make those corrections and rename your file, preferably with the words “New”, “Revised”, or “Corrected” in the file name. Please don’t upload a changed file with the same name as the original file as we won’t be able to tell it’s a replacement and new file.
Re-upload new files to your current platemaking ticket. Log in to Boxcarpress.com with your username and password. Click on the applicable ticket to upload or drag and drop the new revised file.
You can only upload files to your ticket if your platemaking ticket’s status is either set as “Received”, “Pending” or “On Hold”. We will see new files and get to work to process your plates.
If you find that your ticket’s status is “In Platemaking”, you will need to call us at 315-473-0930 to see if it is possible to still add corrected or revised files.
If your ticket status is “Billing Complete”, “Order Complete” or “Shipped”, your ticket is unable to be altered.
Do I send my files reversed for your processing?
No. Please send your artwork and text right-reading as you want it to appear as the final print. We will make a film negative here at Boxcar Press for you. However, if you are planning to use your files in a different process than printing, please call us to discuss how best to prep your files.
When do I need crops and / or registration marks?
You will need crop marks if you are sending the files to us for printing. This will aid us in setting up your files into its final layout. While we will have the info on the final size of your printed piece, your crop marks in your file will help us determine that we are including all the elements you intended and in their proper place. This is especially important when your design will bleed off the page. How to place crop marks on your file, in Illustrator will depend on your CS version.
In CS3 or older – Filter > Create > Crop marks
In CS4 and newer – Effect > Crop marks
If you created your design in Illustrator and set up your artboard to measure the finished size of your printed piece, the crop marks will be outside the artboard. You will need to save your file with an eps extension so the crop marks will be included. You can then save the file as a PDF and send us both EPS and PDF. If you save as an AI extension, the crop marks were left off outside your artboard and not included in your file.
If you created your design on a larger artboard, use the rectangle tool to draw a box the desired size around your design. It will temporarily block your design until you go to your Color window and click on the white square with the red diagonal stripe. Using the selection arrow, move your box around until it’s the correct size and in the preferred place of your design. Add crop marks and save as a PDF.
How do I set up my files for 2-color printing?
The easiest way of setting up a 2-color file in an image editing program, such as Illustrator or InDesign, is to set your first color’s objects in either 100% of a color channel in CMYK mode where the three other color channels not used are set to 0%. The second color would then use 100% of a different color channel. For example, your first color’s objects may be 100% black and your second color’s objects are set to 100% cyan. If you are using this method, be sure to let us know which color channel corresponds to the ink colors you have chosen for your printing.
Our Preferred Method: If you are very comfortable with Illustrator or InDesign, you may use Pantone Swatches from the Swatch Color Libraries palette in lieu of using 100% of individual CMYK color channels. We recommend using swatches from the Pantone Solid Uncoated color book.
Do I send my files to size or scaled down?
You will need to send your files at 100% scale. We do not resize, scale up or down, or rotate any artwork. We highly recommend using the ruler feature available in Adobe Illustrator, Photoshop and InDesign to check your work to see if it is the size you want.
When exporting a PDF from Adobe Illustrator or Adobe InDesign, please double check to make sure it is the correct size by either re-opening it in Illustrator or placing it in InDesign to check the actual dimensions of your file. In InDesign you can use the Rectangle Frame tool to draw a box around your images/text to measure.
In Photoshop, use the Image Size tool to check your size. Saving your file as a .TIF locks your image size.
After I scan my artwork that I want to letterpress print, what do I do now?
Your scanner will likely save your image as a grayscale.jpg. Many scanners will only allow you to scan up to 300 dpi. If you can scan higher, choose 600 dpi. You have some options now.
If looking for the crispest and cleanest impression, you will need to convert the file to black and white only (no grey pixels). You have two methods depending on what computer software you have available. If you only have Photoshop, you will need to convert your file to one that is in image mode of bitmap. If your image dpi is currently 300 dpi, you can choose Image > Image Size and change your dpi to 600 or higher without changing the inches. Your file will temporarily be quite large but you will then save as a .TIF with LZW compression and this will resize it to something smaller and more manageable. A higher DPI can help with preserving your details and smoother pixelation while bitmapping. For exact steps to Image Mode of Bitmap, see our File Prep Tips.
If you have both Photoshop and Illustrator, you can convert your image to image mode of bitmap as directed above, then place your TIF into Adobe Illustrator, and convert the file to a vector art file via the Live Trace option. This does not always work with all files to give satisfactory results, so with practice, you will learn to recognize which files will give you a vector result you like. After converting to vector, save the file as a PDF or EPS for upload.
I want to keep my files in grayscale, how can I make them look their best?
Grayscale is a range of shades of black on a spectrum from 1 to 100. Light gray is in the lower spectrum and darker grays are in the higher spectrum. While 100% black images and text will produce crisp line art and is the norm for letterpress, sometimes you may want to print something where you want to see all the details and subtleties of the shading.
If you are trying to print a photographic image, it’s best to choose one that has areas that provide high contrast between light and dark, that is, the photo has details that are both darker gray in the upper ranges (70 to 100% of black) and lighter gray in the lower ranges (5% to 35% of black). This contrast will give the most depth and interest to the photo. If your photo has mostly shades of black in a similar range (30 – 60% of black), it will look muddy to the eye because it’s harder to discern the shading without a lack of contrast. Experimenting with the image in Photoshop by changing levels of black or adding brightness and contrast can help some with this.
If you are printing a scanned image, where you want to keep the tonal imagery, you can send the file as grayscale and we’ll apply a line screen to it. Your image will be a large shape with the tones created as little dots on the surface of the plate. The films are very sensitive and will capture shades of black down to 5%. So if your background has some color, it may be picked up by the film and show on your plate.
Halftones and grayscale images can be challenging to print with relief plates on the commonly used uncoated papers of letterpress. Call us to discuss your particular image and the results you want to achieve.
It’s not necessary to reverse your files before submitting.
We need your files and proofs to appear the way you want your final design to print – commonly called right-reading (no backward text or images). When we create your film negatives, our software does the reversing to create proper negatives, so leave that part up to us.
In Illustrator, if you want crop marks on your plate, create crop marks, not crop areas!
While using Adobe Illustrator, you will first need to create a rectangle by using the marquee tool (M) in your standard tool palette located on the left-hand side of your screen. Create the rectangle so that its dimensions are your piece’s final trim down size (e.g such as 5.5″ x 7″ for an invitation, etc). Next, while the rectangle is still selected, drag it to its proper location with respects to the artwork. This location should be the correct position intended for the crop marks. Please note that we do not add crop marks to any file at Boxcar Press, as we do not know where or what your intended trim down size is.
While the rectangle is still selected, please select EFFECT>Crop Marks to create the correct type of crop marks in Illustrator. If you need to shorten the length of the crop mark lines or thicken the line weight, you will need to expand the crop marks by selecting OBJECT>Expand or OBJECT>EXPAND APPEARANCES.
If your file has linked images, embed them in Illustrator or Export them as a PDF from InDesign.
Before sending your Illustrator files to us, embed all linked images (an option in the Links palette). If linked images aren’t embedded, they can give an error message that your links are missing and we can’t output your plates! With InDesign, export your file as a press ready PDF.
What’s the smallest type size you can hold in your platemaking?
This question is not as straightforward as it seems. We can hold a 3 pt. Times New Roman type face on 94 and 95 plate material but the real question is the next one about the thinnest line and dots the plates can hold. The font choice and characteristics of the font may limit the point size.
In Illustrator, the only black your submitted file should use is 100% CMYK black (CM and Y are 0%)
When opening any new document in Illustrator, choose File > Document Color mode > CMYK. To Check this before submitting your file for upload – in illustrator versions CS4 and CS5, you can open your Output-Separations Preview window. Click on the drop down window showing Off and select Separations. Click off the black eye and everything left showing on your file is not in 100%K. If you select a part of your file that is left, and look at your color palette, anything that shows a percentage of C,M, or Y needs to be corrected. To correct this – go to Select > Same > Fill (or Stroke). It should highlight everything that looks like black (but isn’t). Than go to the color palette and using the eyedropper, click on the black part of the bar (far right). The C, M, and Y will go to 0% and the K should go to 100%. Now this part of the file should disappear because it is correctly set to 100%K.
Don’t use a jpeg or save as a bmp file for your images!
Our favorite image mode is a .tiff. Or send us vector art images (made in Illustrator or Freehand) instead of raster images (made in Photoshop). Jpeg files will create low-quality letterpress plates that will make you unhappy; its file format is best intended for the web. Files that end in .bmp can also give unwanted results by saving as the wrong size and are also lower quality.
If you want a lineart image, use bitmap mode (don’t use a linescreen or halftone)
Most of the time, if your file contains an image, you’ll want that image to be in bitmap mode for a nice clean bite into your paper. Otherwise your image will produce a halftone, which means your image will be made up of tiny dots on the surface of your plate.
If you zoom in on your image and it is made up of tiny grey and black pixels, it’s in grayscale. We want your images all in black pixels.
You can correct this by:
- Opening your image in Photoshop and selecting Image > Mode > Grayscale.
- Select Yes if a window asks about discarding color.
- Then Select Image > Mode > Bitmap. A window will pop up looking for info – use a resolution of 600-1200 dpi and an output method of 50% threshold.
- Save your files as a tif (with LZW Compression) and send us the tif. Or insert the Tif into your Illustrator or InDesign file.
Images in higher resolution (600-1200 dpi) will give better, finer results than images in lower resolutions (72-300 dpi). If your images lose a lot of detail, you can either re-scan or adjust your levels of black. A quick explanation about the 50% threshold method. A grayscale image is made up of pixels from 1 – 100% black. When you select 50% threshold, you are telling the computer to change all pixels less than 50% black to be white and all pixels greater than 50% black to be black. So sometimes adjusting the levels of gray pixels under 50% to a little darker and over the 50% mark will keep more details in your image. We suggest experimenting with the following: Image Adjustments > Levels or Image Adjustments > Brightness and Contrast. This may give you more pleasing results in your final bitmap tif.
How large can my file be while uploading?
The largest size, data-wise, that we accept is 26MB. If your file’s data size is larger than this, determine if it can be broken up into two or more files. If you actually have a large file in MB but not in inches, check to see if your images could be saved again in Photoshop with LZW compression and placed again into your document. This great compression feature will make your files more manageable.
For alternate electronic ways, we highly recommend compressing the file down with a program such as StuffIt or ZIP. There are also many numerous online free File Transfer Sites, such as YouSendIt.com or DropBox.com, that let you upload a file and send a link for Boxcar to download.
We will also always take your files on CD by mailing to: Platemaking Department; Boxcar Press; 509 W. Fayette St. #135; Syracuse, NY 13204.
Is there a checklist for me to review with my files before submitting to platemaking?
To ease file prep woes and to ensure a smooth production transition from file to plate, it is a great help to all to give your files one last review before submitting them. The first few things to make sure is that your file’s artwork is set to the right dimensions, that you’ve checked your artwork to make sure all plate type line minimums are met, that your file is in the proper color mode or image mode and that your file is in the proper file format and extension.
When working with a file that requires multiple colors for separations, please make sure all objects are assigned to their appropriate Pantone swatch or spot color. Adobe Illustrator and InDesign are excellent programs for setting up and checking such files.
Please also remember to check out any other file prep questions to answer any unresolved questions that you may have.
If I’m scanning an image, what resolution (DPI) should it be?
Most folks want clean line art, and if this is what you’re seeking, scan at least at 600 DPI, though 1200 DPI is even better. Open your scan in Photoshop to convert your file to the Image mode of Bitmap via the 50% threshold method and an output of 600 – 1200. If you lose too much detail, you can make adjustments to your image by using Image Adjustments > Levels or Image Adjustments > Brightnesss / Contrast.
If you’d like a halftone, you can use a 300 DPI scan. With halftones, keep the image in the grayscale color mode in Photoshop, and let us know the LPI / line screen.
Either way, save your image as a TIFF with LZW compression. This will make your file size more manageable when placing into another program like Illustrator or uploading to your job ticket.
Is there a preferred LPI (Lines Per Inch) for halftones?
The ideal LPI depends on your paper and presswork, but most printers printing on uncoated paper use a 100 LPI. It’s a good balance of fine screen and easy printing. The higher the line screen, the more difficult it will be to print, because the high line-screen plate plugs up with ink in the shadows and looks murky over-all. Some printers prefer playing it safe and order 85 or 65 LPI. Using a lower LPI does make the dots coarser and more obvious. The finest line screen that we usually process is 133 LPI, although we would even question the use of 133 LPI, except on coated or hard papers.
If you’d like a halftone for your image, don’t adjust or apply an LPI in your file. Just tell us what LPI you’d like us to use, and we’ll take care of the rest.
If you tell us the paper, the type of press you’re using, and what you hope to accomplish with your halftone, we would be happy to recommend a line screen for you!
What does LPI (Lines Per Inch) do? What do I need to know about LPI and my files?
The amount of dots in an inch of a halftone is determined by the LPI, also known as line screen. The higher the LPI, the more dots there are per inch. A higher LPI means the dots are smaller and less noticeable. Letterpress printers typically use between 85-133 LPI for their halftones. We find that 100 LPI is a good choice for all plate types and is the default we apply if you don’t specify.
What is a grayscale and a halftone?
The technical definition: a halftone is a matrix of different size dots which allow printers to simulate tonal variation when printing with a single ink on press. What this means: a halftone allows you, using one color ink, to approximate various shades of color. Take a magnifying glass and look at a black and white photo printed in your local newspaper. You’ll notice the image is actually made up of different size dots. The smaller the dot, the lighter the color in the halftone. A grayscale is made up of pixels that are in varying shades of black so the tones are represented by the different shades. Once a file has a line screen applied, the grayscale is now a halftone.
Should I gang up my images/smaller files into one larger file?
If you are ordering printing from us, no. Please send individual files and we will set up for most efficient production in our shop.
If you are ordering plates and doing your own printing, yes! By ganging up the plate yourself, you have more control over the margins and gaps between the ganged up artwork. Between each individual piece, we recommend .375” for plastic-backed plates and .5” for steel-backed plates. Our negatives come out of the imagesetter in 18″ strips, so ganging up onto a 17” wide strip, and up to max 22” long, is the most economical way to make negatives. Since we like to keep our maximum plate size at 17 x 22, please break larger files into two files.
That said, if you were to send us many individual files, we’d gang up the pieces in the most cost-effective manner. If you’re using plastic-backed plates, after we gang up your files, we’ll ship your job as a single plate and you can trim them easily yourself, using scissors or an Exacto.
If you’re using steel-backed plates and we gang up your files for you, we’ll ship your job as a single plate, unless you provide a cutting diagram for us. If you are submitting a ganged up file, keep in mind the fingers of our employees who have to trim your metal plates and leave us enough room around your text/images to hold the plate safely while we cut.
What programs do you support?
Our favorite ways to receive files for letterpress platemaking are by you sending us a press-ready PDF file (with fonts embedded) for platemaking. This PDF will serve as both your hard copy and your plate file. No additional faxing or email needed.
Our second favorite way is for you to send an EPS or AI file for platemaking. We also accept PDF digital files in current versions of other major design programs (i.e. Quark, InDesign, Freehand).
If you are creating your files in Photoshop, we like to say that this program is good for images but not so great for text. It’s best to convert your grayscale images in Photoshop and place them into Illustrator where you will add your text. If Photoshop is your only option, start with a file that is 600 dpi minimum so you can minimize the pixelation of your text when you convert files. More on file conversion to Image Mode of Bitmap under File Prep Tips. We prefer tif files from photoshop for upload.
Note, we can often make plates from PDFs created from Word files, however, Word is not able to format your file exactly the way we need. So please tell us your file was originally a Word document so we can anticipate and make corrections. If you are designing in Word, we suggest that you don’t use any funky or crazy fonts we won’t have access to. Oftentimes, they will just print as strange characters. Your images placed in Word will usually require some corrections too. You can email your files to plates@boxcarpress.com for an evaluation first and we’ll advise on how letterpress friendly it is.
Can you scan my camera-ready artwork?
Yes! Simply mail us your camera-ready art and we will scan it in for you. When possible, we love art work that’s on smooth, bright white paper or drafting vellum. Textured paper makes our job more difficult as the scan will pick up any background patterns, paper shadings, paper texture, etc. We are faithful to originals: if you require modification or retouching, you may be charged for additional file preparation time at our shop rate of $60/hour. We’ll contact you before we bill for additional file prep. We can scan, in house, artwork up to 12 x 17 inches.
What’s the thinnest line and smallest dot you can hold on a plate?
It depends on the plate (though no hair lines, please!). If your plate has a 94 or 95 in the product name, we recommend at least a 0.25 point thickness (or larger). If your plate has 145 or 152 in the product name, we recommend at least a .35 point/.007″ thickness (or larger). Watch out for typefaces with swirly curves that thin or have breaks or fonts with fine cross bars.
For dots, we recommend at least a 1 pt diameter if your plate has a 94 or 95 in the product name. Boost that to 1.25pt diameter for plates that are 145 or 152 in thickness. Each of those dots has to stand on it’s own on the plate and that thickness will provide the support at the base of the plate to hold the dot. Watch out for typefaces where the dots on the “I’s or periods are small, as seen in many sans serif fonts that are decorative, free form or look hand drawn.
Undersize lines and dots may appear on your plate as wavy or be missing completely so checking this is very important for a good file and usable plate.
Mark as helpful. 204
Ink
Can I mix an oil-based letterpress ink with a rubber-based letterpress ink or an acrylic ink?
No, it’s not recommended to mix ink types. You can get unexpected results when you mix the different characteristics of oil-based, acrylic or rubber-based inks. The acidities, emulsifications, driers, and amounts of distillates can compete with each other and alter drying properties or tackiness.
What letterpress ink should I use: oil base, rubber base, or acrylic?
We recommend rubber-based inks for general letterpress printing—it’s the type of ink we use in our own print shop. Rubber-based inks dry by being absorbed into the paper. That makes them ideal for the cotton and bamboo blends of paper used in letterpress. Use the oil-based inks if you’d like a glossier ink that works well with coated papers . Oil based inks dry by oxidation or air drying. That is why they can form a skin on the top of the can after opening and why you won’t want to keep it on your press overnight. Try the acrylic if you’re looking for a glossier ink that can still stay open on the press. Acrylic inks will also harden in the can quicker than rubber-based inks so long term storage can be a factor.
It is best to mix only like inks from the same family—oil base with oil base, rubber base with rubber, and acrylic with acrylic.
What are the most essential basic letterpress ink colors for me to have in my shop?
Try our letterpress ink basic starter kit, which includes Printing Black; Warm Red; Reflex Blue; Yellow; Transparent White (mixing white); and Pantone Black (mixing black). With these 6 colors you can mix over 250 pantone colors. If you’re ready for more, you may want to try the remaining Pantone base colors.
How do I firm up my thin letterpress ink?
Add magnesium carbonate to your ink. Magnesium carbonate is available in our Supplies section from Boxcar Press. Inks are measured by their tackiness or stickiness and their body or how stiff it is. An ink’s body can be drippy like chocolate syrup topping or thicker like frosting or paste. The ink can also be described as being long or short. Long inks are tackier and when pulled up straight from the can will have a long tail. The white powder of magnesium carbonate will stiffen your ink and reduce tackiness.
How do I print with light toned letterpress inks on dark paper?
With letterpress, we most often print dark ink on light paper, because that is letterpress printing’s strength! Light ink on dark paper is really best suited for engraving. That said, if you really want light ink on dark paper, just be prepared for paper to show through. Think “chalkboard” for the end results. Letterpress uses transparent inks. Even with opaque white, printing light ink on dark paper will be like using a thin coat of white paint on a brown wall: you’ll see the brown color through the paint. If using a pure white ink, you can run a piece through the press twice to create a more dense color. Metallic inks will be more opaque and are the most popular choice for paper cover-up with dark papers.
Why shouldn’t I let oil-based letterpress ink dry on my rollers
Oil based inks will dry within a few hours if left unattended on press; dried oil-based inks can take a long time to clean and can even cause rollers to be permanently damaged.
Once I’m done printing, how do I clean the letterpress ink off my rollers/plates?
To clean ink off your press, we recommend California Wash used with rags or disposable shop towels. This press wash cleans up acrylic, oil based and rubber based inks well, is a low VOC solvent, and has a mild somewhat citrus odor. For an occasional cleaning and deglazing of rollers, use Easy Street Additive after press wash.
Tell me more about the ink colors that you carry.
We offer all 14 base Pantone mixing inks. These inks, paired with the Pantone formula guide, will allow you to mix any of the guide’s hundreds of Pantone colors. The base inks are: Red (032); Pantone Black (mixing black); Blue (072); Green; Transparent White (mixing white); Orange (021); Process Blue; Purple; Reflex Blue; Rhodamine Red; Rubine Red; Violet; Warm Red; and Yellow. We also carry opaque white for printing white or printing on dark paper stock; universal printing black, the perfect black letterpress ink (available in oil-based or rubber-based only); and custom mixes that match any Pantone number. View a PDF of the Van Son color chart.
When do you recommend I order a custom ink instead of mixing the ink myself?
Custom inks are a good alternative if you don’t have all the the Pantone Basic Colors but you still want to put a specific Pantone color on your press. Some printers prefer ordering custom mix inks for every job they print, though this can get expensive (and, since custom ink mixes come in 1 lb cans, you’ll have a lot leftover).
We recommend going with custom ink particularly in these two situations:
- you’re going to be printing the same color ink over an extended period of time—for example, we ordered custom ink mixes of all the ink colors in our Smock and Bella Figura ink libraries so we can offer consistent color for all customer jobs. This way, if you order a custom ink of say 476U, you’ll know when you need to reorder it a year later it will look exactly the same.
- you’re printing with very light colors or a pastel ink. The formulas for such inks require very precise measurements (.2% yellow plus 99.5% trans white, etc.) and it’s difficult to mix these colors accurately yourself.
Which is a more environmental ink: soy ink, oil-based ink, or rubber-based ink?
We get asked a lot about soy ink from our customers, since there’s this general feeling that soy ink is THE greenest ink out there. That’s not really true. Soy sheet-fed ink has to be just 20% soy to be labeled a soy ink (the exact % of soy varies depending on the specific ink). Rubber-based and oil-based inks both have 20-30% vegetable-oil (soy and linseed). Linseed oil is the traditional letterpress ink vehicle: it’s what Gutenberg used when he first used ink. Also keep in mind that soy inks are really geared toward high speed printing and loaded with lots of driers—they’re usually very thin, liquidy inks, not ideal for letterpress. In our experience, soy inks don’t transfer well to letterpress printing, and you’ll get the same environmental impact from using oil-based or rubber-based inks.
Platemakers
When do I replace my kreene in my platemaker? And how do I replace kreene?
Kreene, a flexible and matte transparent plastic, is used in a platemaker’s vacuum frame to hold films securely against photopolymer plates during exposure. But over time, it’s the nature of kreene to get wrinkled and lose flexibility. When you find that your kreene no longer creates a smooth seal, it’s time for a kreene replacement! At Boxcar Press, we replace our kreene every few days, but we process a lot of plates. With lower use, kreene can last for several months.
To replace your kreene: cut out a square of kreene to the size of the previous kreene piece (your kreene will be slightly larger than the grooves in the vacuum table). If your platemaker has one, pull the round bar out the previous sheet of kreene. Affix the new sheet of kreene to the bar with double-stick tape. Lay the kreene in position on the vacuum table and turn the vacuum on. Work out any wrinkles in the kreene so it remains flat. Using double-stick tape, affix the kreene edge opposite the bar to the vacuum table. You can then roll the kreene out over your vacuum table and start exposing your polymer plates. To increase the life of your Kreene, roll it out flat in your platemaker at the end of the day.
When do I replace my platemaker’s brushes?
A platemaker’s brushes wear out after prolonged use: these brushes should be replaced every 6-36 months. You can tell when a brush is tired out because the bristles are matted down. You can lengthen your brush life by keeping the brushes wet all the time and running your fingers through them to encourage the bristles to stand up. We sell replacement brushes for all of our platemakers: please e-mail or call us to order these.
How do I maintain the mounting rubber on my platemaker?
Magnetic mounting rubber and rigid mounting rubber come pre-sealed. Over time, this seal breaks down. You can make touch-up repairs with our green die sealer. Remove any old die sealer and apply green die sealer in a thin bead to the edge of the mounting rubber. Let dry overnight.
How do I drain and refill my platemaker?
Drain the platemaker often, usually after every 10 to 12 processed plates. To drain, open the drain valve. The washout water is safe to go down the drain. To refill, close the drain and fill with water. Leave the tank full of water so the brushes don’t dry out. If you’re leaving the machine unused for an extended period of time, add half a cup of bleach to the water to resist algae. When you use the machine again, drain and refill the tank with fresh water.
Printing with a Platen Press
Will a Boxcar Base work with a platen press (also known as a clamshell press)?
The short answer: yes, yes and yes. In fact, we manufacture a Deep Relief Boxcar Base specifically with platen press users in mind. The Deep Relief bases are a thinner base to keep the inking rollers from inking the base and plate backing while adjusting roller height. These bases got their name because they are paired with a thicker relief plate . Read more about choosing your base.
I own both a Vandercook and a platen press – do you suggest that I buy two separate bases, the Deep Relief Base for the platen press, and the Standard Grid base for the Vandercook?
We suggest purchasing one type of base for both presses, so that your presses will be able to share the same plate. It really comes down to your experience: if you’re a new printer, go with the Deep Relief base. Setting roller height can be a longer adjustment process on platen presses and this base will be more forgiving as you work through this. If you can use a roller gauge in your sleep, and you have experience expertly adjusting your inking rollers on your C&P, go with the Standard Base. The Standard Base’s plates are less expensive per square inch as they are slightly thinner but all plates, when paired with the correct base, equal type high (.918) and that is the most critical factor.
If I have a 10 x 15 chase on my press, why can’t I use a 10 x 15 base?
We totally understand that you want to get the most use and space out of your press. However, knowing about some of the challenges you will face can help you make decisions about the correct size.
First, keep in mind that every press, like every person, has a limit to its strength. A press with a 10 x 15 chase will never be able to hammer a 10 x 15 block of text. You’ll be able to get a good impression using about 60-70% of your chase, depending on your form. Secondly, your base needs to stay put in your chase with a good lockup. To secure your base in your chase, you need to make room for the quoins plus furniture for distributing the weight of the base, and gauge pins. Gauge pins fit in the space outside the base and over the furniture.
We recommend checking out our Base Selection Chart which recommends the ideal size base for your chase. With a 10×15 chase, we would recommend a 9×12 base, for instance.
If you really want to max out the base size, keep in mind your base should be at least 1 inch, preferably 1.5 inches, smaller than your chase. If you use a lot of paper that is precut, it is most likely smaller than your base. This can make it challenging to place your gauge pins and still hold the paper and not hit the base. One safety note, the larger the base in your platen press, the further you have to reach into the press to place your paper. This is very important with a larger press with a motor, so take into consideration your comfortable reach, the speed of the press, and your fingers when locking up a larger base.
How do I prevent my gauge pins and grippers from smashing into my base? In other words, what do I have to worry about most when printing with a Boxcar Base on a platen press?
When using any kind of polymer printing base with your platen press, it’s vital to keep the gauge pins and the grippers from smashing into—and denting!— your base. When the press goes to impression, make doubly sure – no, make triply sure – that the gauge pins and grippers will not impact the Boxcar Base’s surface. Here’s how to do this.
You must carefully place your gauge pins on the platen to avoid hitting the base. Place the gauge pins below and beyond where the base will sit in the chase. In addition, place the grippers to the left and right of where the base sits in the chase. This will keep the grippers and gauge pins from contacting the base when the press closes for impression. If you need to use the grippers, keep them outside the base but construct a paper (or tape or string) frisket between them to hold the paper.
You might find it easier to position gauge pins if you print on sheets larger than the final trim size, especially if you have a quarter inch margin or less on either of your feed edges. This will move the gauge pins farther from the printing area and from the base – reducing the likelihood of a gauge pin/base collision. Print on the largest possible sheets and trim them down after printing.
You might also want to consider using Henry gage pins for certain print jobs. These cushiony paper holders may be just the thing and won’t damage your base or require cuts in your tympan paper.
What will I need to do to my platen press before printing with polymer and a Boxcar Base (especially if my printing is blobby and/or has a “halo”)? i.e. how do I add tape to my rails?
Every platen or lever press has wear on the rails and needs tape on the rails to raise the rollers to the right height. This is whether you use lead type or polymer—although the problem surfaces more frequently on polymer if the roller rails aren’t set correctly. You have to build up the rails that the roller trucks travel on so that the rollers just graze the surface of the form. The best way to do this is to add equal layers of masking or strapping tape to each rail. Keep building up the rails in this fashion until whatever you’re printing doesn’t ink up at all (i.e. bring the rollers up just past the point where the rollers ink the plate). Then take off one layer of tape so that the rollers drop down with minimum contact to the plate. This will keep ink from getting on the backing of the plate and the base, and it will also help make your printing crisper. It’s not uncommon to have to add as much as a 1/16″—or sometimes 1/8″—in tape in order to get the rails to the right height. These presses are often 100 years old and have 100 years of wear that you have to overcome. We do not recommend that you adjust your trucks or printing plate/base for this problem. Better printing results from type-high rollers. After you add tape to your rails, we recommend using a roller gauge to perfect the height of your rollers.
What are roller gauges and why do I need them?
Roller gauges are especially indispensable with a platen press. Letterpress rollers need to be positioned just right in order to deposit a thin film of ink onto the surface of the form, without squeezing ink over the edges. A roller gauge will help you accurately measure the height of your rollers so you can produce the crispest printing that your press is capable of. We sell roller gauges, precision ground to type high, which are also very fashionable.
When your rollers are positioned correctly, your printing will look beautifully crisp. But if your rollers aren’t positioned at the right height, your printing will have a halo effect: dark around the edges and/or chunkier/blotchier than it should be. If you ever notice ink on the back of your polymer plate or on your base — it’s a roller gauge emergency! Adjust your rollers now! We have a great video on setting roller gauge height in our Boxcar Training Videos and step by steps are listed here.
Step 1. While your press is inked up, remove the chase (on platen presses) or the base (on a Vandercook).
Step 2. We recommend checking the roller height in the four corners of the press bed. We’ll start in the upper right hand corner. Engage the form rollers and position them over the upper right corner of the bed.
Step 3. You will be pulling a stripe of ink on the round surface of the roller gauge. Pull the gauge underneath the form rollers so that a stripe of ink is transferred to the rounded surface of the gauge’s cylinder. Measure the stripe of the ink: you want your ink stripe to measure 3/32”. If the strip of ink is less than 1/16”, you’ll have difficulty consistently inking your plate (some areas will appear too light, and some areas will appear too dark). If your strip of ink is wider than 3/32”, your rollers put too much pressure on your plate and cause your printing to be chunky/blurry.
Step 4: On a platen press, to adjust the height of your form rollers: add tape to the rails that the roller trucks ride on. You may have to add several layers of tape. Strapping tape or plumber’s silver tape is frequently used for this. If you’re using a press other than a platen press, consult your manual as to how to raise your form rollers.
Step 5: Repeat steps three and four in each corner of your press bed.
Step 6: When your rollers are positioned correctly, you should pull identical 3/32” stripes of ink from the four corners of the press bed, and your printing should be both crisp and beautiful!
If you continue to notice inconsistencies in your inking after adjusting your roller height correctly, you may need to purchase new rollers and, if using a platen press, roller trucks as well.
Unexposed Photopolymer
What’s the smallest type size you can hold in your platemaking?
This question is not as straightforward as it seems. We can hold a 3 pt. Times New Roman type face on 94 and 95 plate material but the real question is the next one about the thinnest line and dots the plates can hold. The font choice and characteristics of the font may limit the point size.
What’s the thinnest line and smallest dot you can hold on a plate?
It depends on the plate (though no hair lines, please!). If your plate has a 94 or 95 in the product name, we recommend at least a 0.25 point thickness (or larger). If your plate has 145 or 152 in the product name, we recommend at least a .35 point/.007″ thickness (or larger). Watch out for typefaces with swirly curves that thin or have breaks or fonts with fine cross bars.
For dots, we recommend at least a 1 pt diameter if your plate has a 94 or 95 in the product name. Boost that to 1.25pt diameter for plates that are 145 or 152 in thickness. Each of those dots has to stand on it’s own on the plate and that thickness will provide the support at the base of the plate to hold the dot. Watch out for typefaces where the dots on the “I’s or periods are small, as seen in many sans serif fonts that are decorative, free form or look hand drawn.
Undersize lines and dots may appear on your plate as wavy or be missing completely so checking this is very important for a good file and usable plate.
Mark as helpful. 204
I want to use photopolymer to do something other than letterpress printing. How do I know what plate to use?
While our troubleshooting only extends to using photopolymer plates for letterpress printing, there are literally dozens of other uses for photopolymer plates. If you know the tech specs of the plate that you need, or if you can send us a sample of the plate required for your application, we would be happy to try and recommend a plate that we have in stock that will work for you.
We have innovative people using our plates for metal clay jewelry making, translucent porcelain, and leather work. We always like to hear what you want to try.
Is processing a photopolymer plate toxic?
None of the byproducts of processing photopolymer plates are known to have health risks, except if you’re allergic by contact to plastic. Check out the MSDS’s for more specific health information. You can find each plate’s MSDS on it’s product page: plastic-backed plates; steel-backed plates; intaglio plates.
I’m a metal clay artist. What photopolymer plates do I use?
We carry plates that are very similar to those recommended by Art Jewelry Magazine. Many metal clay artists have used our plates to great success. We have several plate types that will suit your needs and preferences.
Art Jewelry Suggests | Boxcar Press plate | Boxcar plate thickness | Plate material | Impression |
---|---|---|---|---|
0.8mm | 94FL | .94mm/.037” | plastic backed | shallower |
1.52mm | KF152 | 1.50mm/.060 | plastic backed | deep |
0.9mm or greater | 94SB | .94mm/.037” | metal backed | shallower |
0.9mm or greater | 145HSB | 1.40mm/.057″ | metal backed | medium |
1.52mm | 152SB | 1.50mm/.060″ | metal backed | deep |
Boxcar Press offers two options to metal clay artists. We can sell you unexposed polymer plates for do-it-yourself artists to create their own negatives and process themselves. Check out our new Plates by the Pound service for our plastic backed plates under our Supplies. Or we can take your digital files or images and professionally create plates for you, quickly and economically.
In either case, you will want to store your exposed plates in a zipper bag out of sunlight. You may also want to consider using a silicon spray to protect the plate from the moisture in the clay. You will want to clean the plate with vegetable oil. Exposure to too much light and moisture will cause your plates to deteriorate.
Remember, we’re a letterpress shop, and letterpress is our expertise. We can’t answer specific questions about how our plates work with your process, but we can offer information on the polymer plate material, thickness, exposure times, and processing.
For additional information, you may also want to check out:
- Metal Clay yahoo group: join this vibrant community of over 3,000 artists.
- Maggie Berman’s site features a great instructional article on using polymer plates for metal clay, PMC, or precious metal clay artists.
How do I use a Stouffer Gauge to help process my plates?
Instructions for using the Stouffer Gauge to accurately figure out the exposure time for your photopolymer plates: The Stouffer gauge is a reusable piece of continuous-tone film that you should use to test photopolymer plate exposures. Place the Stouffer Gauge in contact with a 1” x 6” strip of plate material (after you peel off the plate’s protective plastic cover). Then expose the plate.
You’ll have to guess the first exposure time because that varies depending on the equipment that you use. Start with the exposure time listed on your plate’s tech data sheet. For exposure times, please keep in mind that these times are for commercial photopolymer platemaking equipment. Any alternative photopolymer platemaking devices may have very different times and you’ll have to experiment more to find your ideal time.
Also check the plate’s tech data sheet for the Stouffer value you’re trying to hold during exposure. For example, the 94FL has a Stouffer value of 18. Make sure that the exposure used with the Stouffer Gauge hardens the plate for all the numbers up to and including #18. If you goal is #18, and #19 and #20 start to harden during your exposure time, then your exposure time is too long– decrease the exposure time. If your goal is #18, and #17 hardens but #18 washes out on the test plate, then increase the exposure time.
You most likely will have to expose several different test plates at several different exposure times to find the perfect exposure. Since the Stouffer gauge is small, you won’t waste much plate material in the process.
Can I mount your plates on wood?
We don’t recommend it. If you are determined to use wood, however—know that, even after your lengthy set-up time that will be required of you, you’ll still see uneven printing if using a wood base. Wood simply isn’t a flat enough surface to print on.
How are plastic-backed and steel-backed plates different?
When mounted on their appropriate bases, plastic-backed and steel-backed photopolymer plates both create type-high surfaces for letterpress printing. Both plate types are recyclable. We’ll talk about some of their differences below.
Plastic-backed polymer plates are flexible, transparent, easy to cut, and mount onto a Boxcar Base for simple registration. You’ll find these plates:
- can be cut with scissors in both their unexposed and exposed forms.
- are transparent, meaning you can see the Boxcar Base’s grid through your plate. This allows for simple alignment of your plates to your base: For perfect registration, align a certain element of your plate to the grid: take a horizontal or vertical element in your plate (this could be your registration marks, or a horizontal line in your artwork) and line it up to the grid.
- eliminate plate creep (steel-backed plate users sometimes experience this while on press). The plastic-backed plate’s adhesive is shift resistant, giving you a secure, strong hold during printing (but the adhesive also peels up easily when you’re done printing)
- allow printers to print two color jobs using one plate if the design elements don’t touch. Cut out the second color images/text with a craft knife or scissors and set aside. Print color #1. Set your second color images back in place and pull up the first plate for color #1—perfect registration!
- allow designs to be ganged up on plates closely to save space (and money).
- are reusable. You will be able to reuse the plate many times if you keep the adhesive protected with the blue overlay after printing. You can also replace adhesive for even more extended plate use.
- more prone to curling, especially with large solid areas over time.
- If purchasing unexposed plastic-backed polymer plates, you’ll also want to purchase film adhesive to adhere your plates to your base. If we’re making your plates for you, we include adhesive.
- are suitable for metal clay jewelry.
- Over here at Boxcar, we use plastic-backed plates for all our printing (the Jet 94 Clear plate paired with the Standard Boxcar Base).
Steel-backed polymer plates are compatible with magnetic bases, generally the Patmag or Bunting base. Steel-backed polymer plates:
- require cutting with a metal shear or heavy-duty trimmer. You can use tin snips, though you may end up with kinks in your plate, as tin snips won’t cut as cleanly.
- sometimes shift and creep on your base during printing. Magnets in the base effectively hold a plate from peeling but cannot always hold a plate from moving side to side. The cylinder or rollers of a press can move steel-backed plates out of register (that’s “plate creep”).
- are not transparent. Because magnetic bases aren’t gridded (and you can’t see through these plates), you’ll have to align your plates to your base with a line gauge and possibly registration marks. This works, but it is more time consuming and there’s more room for error.
- are rigid, meaning they don’t bend well. This inflexibility can cause plates to kink and warp when handled so that their corners may work up while on press. Steel-backed plates are, however, very durable and not prone to curling over time.
- can be more expensive than plastic-backed plates because you may require registration or crop marks which makes for a larger plate.
- are difficult to get on and off the base, especially when the base has inlaid magnets. When placing metal plates on a magnetic base, keep fingers clear so they don’t get pinched when the magnet grabs. When taking your plate off the base, try an ink knife to pry under the plates to release from the magnetic base.
- have sharp edges, which dictate extra care when handling.
- can be used for a wide range of printing and impression—on leather, metal clay jewelry, ultra heavy-weight paper stocks. Steel-backed plates can also be used on etching presses when relief printing is desired. They are not suitable for high temperatures of foil stamping though.
Customer Service Questions
When will I receive my order?
Photopolymer supply orders ship from our warehouse within 1-2 business days.
Custom Platemaking orders ship depending on the service you choose:
We offer a 1 business day turnaround, or Same Day Rush – an extra fee service.
For shipping in the USA, we offer UPS Ground, UPS 3 day air Service, UPS 2 day air Service, UPS Overnight morning, UPS afternoon Saver and UPS early Am (before coffee) 8:30 am service.
For International Customers, we offer US Postal Priority or Express Mail and UPS Worldwide Saver.
Remember that the days refer to business days and not weekends.
How do I know when my order has been shipped?
For platemaking, the day your order is completed (Order Complete) is the day your order ships. You will get a UPS tracking number via the log-in email on your account. Your invoice will be shipped in a separate email. Review your Order History to see all past and current orders for your status. For international orders using the US Postal Service, you will receive an email with your tracking number.
For Supplies – an email will be sent with the tracking number.
I need my order shipped today. By what time do I need to place the order?
For supply orders: Orders typically ship within 1-2 business days. If you need your order immediately, we encourage you to request expedited overnight shipping. However, if you’re in a serious letterpress emergency, please place your order before noon EST and mention that you’d like same day shipping. We’ll do our best to make it happen!
For platemaking: place your same day rushes by 1 p.m. EST.
Do you ship internationally?
Supplies: We ship supplies to Canada via UPS Standard or UPS Worldwide Saver and US Postal Service.
We ship international orders (outside of Canada) via UPS Worldwide Saver and US Postal Express Mail.
We think our online ordering system is pretty nifty but of course you can phone in your order to us by calling 315-473-0930. We love to talk to our customers.
Platemaking: We ship platemaking orders to Canada via UPS Standard or UPS Worldwide Saver and US Postal Service. We can ship Worldwide Saver to any international location or opt to use the US Postal Express Mail. These options are all at the click of a button through out platemaking site.
Printing: Yes, we love working with international clients and sending off printed letterpress beauties to destinations far and near.
What is your return policy for supplies?
Unexposed plates are not returnable as they have been custom cut for your order. Ink orders may or may not be returnable based on the date the order was made. Bases may or may not be returnable based on whether they have been used. We try to be fair in our returns so please call and we will work with you individually.
Once my order is placed online, how do I make a change to it?
Supply orders: please call us or e-mail us as soon as possible.
Platemaking: First, log-in to see your order and check its current status. If we haven’t begun processing your order (STATUS – RECEIVED), you’ll be able to change your order details or upload files online. If we’ve already begun working on your order (STATUS – IN PLATEMAKING), please call us or e-mail us immediately, as you won’t be able to adjust your order online and we can see if the production process is already too far along. At this point, we can still change your shipping options and shipping addresses. If your status is BILLING COMPLETE, we will not be able to make any adjustments at this time.
How do I cancel an order?
For supplies, please call us as soon as possible to cancel your order. We will have to discuss refunds and crediting accounts as your online Supply Order has already been charged for payment.
For Platemaking – you can call us right away or you may be able to cancel your order online, if your status is still in RECEIVED or ON HOLD.
Log on to platemaking and you’ll see all current orders. Choose Complete Order to cancel your order. Confirm when it asks if you want to proceed. Your order status will reflect Order Cancelled.
The option to cancel is not available once we move your ticket into platemaking production. Cancelling after this step may incur some production costs. Please call us right away to minimize those costs, if possible.
How can I check the progress of my order?
Log on to your account in platemaking. It will take you to your Orders page where the current status will be visible.
Status Explanations:
- Pending – Your order has been started but all the steps have not been completed. This requires further action on your part.
- Received – Waiting for us to review your files.
- On hold and awaiting action on your part.
- On Hold No Files Received – Please try uploading again or call for assistance.
- On Hold Bad Files – Your files need attention. You will receive an email indicating your order is on hold with the problem and asking you to correct and upload new files. File errors may include your files measure too large to plate, not in correct color mode, lines or dots too thin, files are in grayscale, etc.
- On Hold – Credit Card declined or expiration is passed. There is a problem with your payment, please contact us.
- In Platemaking – We are in production making your films to make plates. Your ticket is locked as we are moving ahead.
- Billing complete – Your platemaking job is billed and awaiting shipping.
- Shipping Complete – We have shipped and still need to Invoice your order.
- Order Complete – We closed out your order as we have created a shipping label and your package is out the door. The day your order was completed was the day it shipped.
How do I take advantage of the free 2 day shipping?
Boxcar Press offers free two day shipping for platemaking orders that are over 120 square inches as of August 15th, 2014. If your order qualifies, this option will appear as the default shipping choice.
Please remember these details about this service:
- Two day service is ground service for those already within our 1 or 2 days service area (New York state, the Northeast to Maine, down to Virginia, and parts of Wisconsin, Illinois and Kentucky).
- If your usual UPS ground is 3 day – 6 days, you will receive UPS 2 day Air.
- If you have selected any overnight air services for shipping, we will NOT downgrade for free 2 day service. We will believe that you really need the faster overnight service.
- If you really do need 2 day Air service, please choose the 2 day Air and don’t wait for us to upgrade you from ground or a slower service. It’s hard to make UPS deliver faster once it’s out for shipping.
- Free 2 day air applies to business days and not Saturday delivery.
Can you explain the same day rush service and fee?
Boxcar Press has a pretty fast platemaking turnaround service with our one business day turnaround. But if you have an even greater need for speed, consider our Same Day Rush Service. If you create your job ticket, upload your files before 1 pm EST, and choose Same Day, we’ll get your files out the door to arrive the next Business Day via UPS. Of course, speed comes at a price, the fee for Same Day Rush starts at $45 or 40% (whichever is greater) plus the regular cost of the plate plus your overnight shipping costs. Your minimum cost for a Same Day Rush plate is $75 before shipping and goes up from there.
So, we encourage you to make use of the one day turnaround as much as possible. Create your job ticket and upload your files before 5:30 pm EST and we’ll ship on the next business day, assuming your files are in tip-top A1 shape. File corrections may delay your shipping.
Can you explain how you calculate the file dimensions for billing
Here is how we compute dimensions – we gang all your files up together and draw a box around the “black” part – the images and text. Now we know the length and the width. We multiply these two numbers together and this is your square inches total. We then multiply this square inch number by your square inch price of $0.62/sq inch or $0.67/sq inch.
Example:
9″ x 8″ is your “black part”
9” x 8” = 72 sq inches x $0.67 = $50.40
If your file has crop marks, we measure outside the crop marks. So if you don’t need crop marks, consider leaving them off to save a little cash.
Troubleshooting
Why do I have ink on my Boxcar Base?
It’s important to keep the grid on your Boxcar Base clean so you can see its registration marks when printing. If your rollers ever lay ink down directly on the base’s surface, STOP! STOP! STOOOOOOOOOOOOOP! Don’t keep running the press because something is out of alignment. Then ask yourself:
- Are your rollers at type-high? Using a roller gauge, check to make sure your rollers are set for type-high printing material. The surface of the base is far below type high and should never come into contact with the rollers.
- Is your base flat in the press bed? Take a piece of onionskin paper and try to slide it between the base and the press bed – if the onionskin paper fits, one of the corners of your base is working up in the press. Frequently this is caused by tightening the quoins too much. Since the Boxcar Base won’t work up as easily as handset metal type or monotype, you don’t need to tighten the quoins quite as hard.
Still getting ink on your base? If, after checking the roller height and loosening the quoins, you still have problems with ink on your base – contact us and we’ll assist you in problem-solving further.
Most of my plate is printing fine, but one or two areas of the plate are printing heavy. What do I do?
More often than not, this is a result of roller problems. It could be the height of your rollers or your rollers can have an uneven or flat spot on the surface (read more about roller gauges). If you processed your plates yourself, there’s the chance your plate wasn’t processed correctly and you have “fat” text, which can cause some areas to look heavier.
How do I get that darn ink off my base?
Rest assured that ink on your base is a cosmetic problem; ink won’t damage the tolerances or the thickness of the plates. But if your base’s grid is covered in a pretty shade of PMS 2756, registration will be difficult, as you won’t be able to see your grid well!
You want to try and remove ink from your base before it’s dried. Aluminum is like your skin, with millions of pores that will absorb the pigments of the ink. But unlike your skin, aluminum’s surface doesn’t shed. If ink dries in these pores, it’s very difficult to get out. When ink contacts the base, clean it off immediately with any press wash so that you’ll continue to have a beautiful gray surface to attach your plates to.
If ink has dried on your base, use a Mr. Clean Magic Eraser sponge (or similar generic product) and Simple Green (found in hardware and drug stores). Wet the sponge and squeeze out excess. Wipe your base to start to remove all the ink. Sometimes the sponge will do it all. If you have some ink remaining, use a little Simple Green and wipe again. This will do the job beautifully. Rinse out the sponge until clean and let it dry for the next time. Dry the base with a soft rag.
Most printers who use the Boxcar Base have very clean bases because they make sure, like all their other non-printing surfaces, to keep things clean and tidy during the whole course of the printing process.
My letterpress plates are starting to curl. How do I flatten them out?
Like our skin, plates can be affected by the room temperature, humidity, and age. When humidity levels are low, the plates can look and feel brittle. With the passage of time, the thinner polymer on the plate edges are pulled towards the denser polymer text and images on the front—this causes curling. With a life expectancy of up to 1 year or more, polymer plates do age, but these simple steps can hydrate your plates and give them extra longevity.
Step 1. Place your plate back in your platemaking washout system for up to ½ a minute (or, if you don’t have a washout unit, simply immerse in water). We suggest room temperature for a quick dunking. A ½ minute may only be necessary if your plates are severely curled.
Step 2. Sponge off the water and place back in the drying oven of the platemaker for 5-10 minutes. If you don’t have a platemaker, use a hair dryer to warm the plate and make it more pliable. Placing your plate in a box and blowing the hair dryer into the box will keep the warm air more contained and warm the plates more effectively.
Step 3. After the plate warms and starts to become more pliable, place the plate in its bag and set a heavy object on it to keep the flattened shape.
This should help your plates relax so you can adhere them to your base for additional print runs.
Here’s some final advice:
- if using a hair dryer, take care to avoid putting it too close to the plates.
- be patient, as warming the plates takes time.
- watch that you don’t handle your letterpress plates too roughly after the wash and during drying so your relief images don’t chip.
- remember to store your plates flat out of direct light and in a bag so that fluctuations in humidity don’t affect the polymer.
- check your adhesive backing, to see if the adhesive needs to be re-applied to the back of your polymer plate for a secure hold on your base.
Using Your Plates
Can I cut the polymer plates myself?
Plastic-backed polymer plates are simple to cut: just use scissors. Easy. Fun. Done.
Steel-backed photopolymer plates are not simple to cut. For the cleanest cut, we recommend using a metal shear or heavy-duty trimmer. You can also use tin snips, though you may end up with kinks in your plate, as tin snips won’t cut as cleanly. If we process your plates, we can cut your steel-backed plates on our metal shear– just include a cutting diagram with your order. (To make a cutting diagram, use a line with a magenta stroke to indicate the cut lines on your file. Make sure to keep your cutting diagram simple, since we can only make straight cuts across steel-backed plates).
Do I need to order adhesive if I’m having a plastic-backed plate processed by you?
No! Any plate that will be printed on a Boxcar Base will have Boxcar film adhesive applied at no charge.
How do I clean my photopolymer plates?
Step 1. Start to remove ink with a soft dry rag. If you are inking correctly, you should only have a thin layer of ink on the surface of your polymer plates. So start with a soft dry rag to lightly remove the letterpress ink. Normal shop rags, worn t-shirts, or synthetic printing cloths work well for cleaning the plate surface. A hard hand is not necessary here; a light stroke can remove most of the ink.
Step 2. Wipe polymer plates down with a little mild solvent to remove the remaining ink. Choose a mild solvent. Printers who want to keep their photopolymer plates should consider a water-miscible solvent. Aggressive solvents that can clean lead type (like methyl ethyl ketone (MEK) or denatured alcohol) often dry out polymer plates, causing them to crack a few months later. Do not use alcohols. Keep solvents away from plate edges so that the solvent doesn’t contact the film adhesive. We recommend using solvent sparingly. Water-miscible solvents do not mean that you use water for washing your plates. It can soften and deteriorate your plates so they start to chip or crumble.
Step 3. Wipe off your letterpress plates one last time with a dry rag.
On all these steps, remember don’t rub too hard! The photopolymer is difficult to damage through scrubbing, but you should treat it like any typographic surface and not use too much abrasion when cleaning. Because you aren’t putting a lot of ink onto the plate relief surface, you can easily, but firmly wipe off the ink from your plates with just a light hand. Your polymer plates can last for several years if you follow these cleaning instructions (and also store your clean plates properly).
If you’re not planning on saving your plates, just clean them with any normal press wash before recycling them.
How should I store my polymer plates?
To preserve your plates, the manufacturers recommend storing polymer plates in a constant humidity between 50% and 60%. At the very least, avoid extreme fluctuations in humidity. If stored properly (and cleaned correctly), your letterpress plates can last for one year or more.
- For your exposed plates, maintain a constant humidity by storing plates in a ziplock bag. Keep your plates away from ultraviolet light that will crack the surface of your plate (i.e. store in a drawer or cabinet).
- For your unexposed plates, store in a black light-blocking bag that is taped shut.
Can I mount your plates on wood?
We don’t recommend it. If you are determined to use wood, however—know that, even after your lengthy set-up time that will be required of you, you’ll still see uneven printing if using a wood base. Wood simply isn’t a flat enough surface to print on.
My letterpress plates are starting to curl. How do I flatten them out?
Like our skin, plates can be affected by the room temperature, humidity, and age. When humidity levels are low, the plates can look and feel brittle. With the passage of time, the thinner polymer on the plate edges are pulled towards the denser polymer text and images on the front—this causes curling. With a life expectancy of up to 1 year or more, polymer plates do age, but these simple steps can hydrate your plates and give them extra longevity.
Step 1. Place your plate back in your platemaking washout system for up to ½ a minute (or, if you don’t have a washout unit, simply immerse in water). We suggest room temperature for a quick dunking. A ½ minute may only be necessary if your plates are severely curled.
Step 2. Sponge off the water and place back in the drying oven of the platemaker for 5-10 minutes. If you don’t have a platemaker, use a hair dryer to warm the plate and make it more pliable. Placing your plate in a box and blowing the hair dryer into the box will keep the warm air more contained and warm the plates more effectively.
Step 3. After the plate warms and starts to become more pliable, place the plate in its bag and set a heavy object on it to keep the flattened shape.
This should help your plates relax so you can adhere them to your base for additional print runs.
Here’s some final advice:
- if using a hair dryer, take care to avoid putting it too close to the plates.
- be patient, as warming the plates takes time.
- watch that you don’t handle your letterpress plates too roughly after the wash and during drying so your relief images don’t chip.
- remember to store your plates flat out of direct light and in a bag so that fluctuations in humidity don’t affect the polymer.
- check your adhesive backing, to see if the adhesive needs to be re-applied to the back of your polymer plate for a secure hold on your base.
Letterpress Inks
What letterpress ink should I use: oil base, rubber base, or acrylic?
We recommend rubber-based inks for general letterpress printing—it’s the type of ink we use in our own print shop. Rubber-based inks dry by being absorbed into the paper. That makes them ideal for the cotton and bamboo blends of paper used in letterpress. Use the oil-based inks if you’d like a glossier ink that works well with coated papers . Oil based inks dry by oxidation or air drying. That is why they can form a skin on the top of the can after opening and why you won’t want to keep it on your press overnight. Try the acrylic if you’re looking for a glossier ink that can still stay open on the press. Acrylic inks will also harden in the can quicker than rubber-based inks so long term storage can be a factor.
It is best to mix only like inks from the same family—oil base with oil base, rubber base with rubber, and acrylic with acrylic.
What are the most essential basic letterpress ink colors for me to have in my shop?
Try our letterpress ink basic starter kit, which includes Printing Black; Warm Red; Reflex Blue; Yellow; Transparent White (mixing white); and Pantone Black (mixing black). With these 6 colors you can mix over 250 pantone colors. If you’re ready for more, you may want to try the remaining Pantone base colors.
How do I firm up my thin letterpress ink?
Add magnesium carbonate to your ink. Magnesium carbonate is available in our Supplies section from Boxcar Press. Inks are measured by their tackiness or stickiness and their body or how stiff it is. An ink’s body can be drippy like chocolate syrup topping or thicker like frosting or paste. The ink can also be described as being long or short. Long inks are tackier and when pulled up straight from the can will have a long tail. The white powder of magnesium carbonate will stiffen your ink and reduce tackiness.
How do I print with light toned letterpress inks on dark paper?
With letterpress, we most often print dark ink on light paper, because that is letterpress printing’s strength! Light ink on dark paper is really best suited for engraving. That said, if you really want light ink on dark paper, just be prepared for paper to show through. Think “chalkboard” for the end results. Letterpress uses transparent inks. Even with opaque white, printing light ink on dark paper will be like using a thin coat of white paint on a brown wall: you’ll see the brown color through the paint. If using a pure white ink, you can run a piece through the press twice to create a more dense color. Metallic inks will be more opaque and are the most popular choice for paper cover-up with dark papers.
Why shouldn’t I let oil-based letterpress ink dry on my rollers
Oil based inks will dry within a few hours if left unattended on press; dried oil-based inks can take a long time to clean and can even cause rollers to be permanently damaged.
Once I’m done printing, how do I clean the letterpress ink off my rollers/plates?
To clean ink off your press, we recommend California Wash used with rags or disposable shop towels. This press wash cleans up acrylic, oil based and rubber based inks well, is a low VOC solvent, and has a mild somewhat citrus odor. For an occasional cleaning and deglazing of rollers, use Easy Street Additive after press wash.
Tell me more about the ink colors that you carry.
We offer all 14 base Pantone mixing inks. These inks, paired with the Pantone formula guide, will allow you to mix any of the guide’s hundreds of Pantone colors. The base inks are: Red (032); Pantone Black (mixing black); Blue (072); Green; Transparent White (mixing white); Orange (021); Process Blue; Purple; Reflex Blue; Rhodamine Red; Rubine Red; Violet; Warm Red; and Yellow. We also carry opaque white for printing white or printing on dark paper stock; universal printing black, the perfect black letterpress ink (available in oil-based or rubber-based only); and custom mixes that match any Pantone number. View a PDF of the Van Son color chart.
When do you recommend I order a custom ink instead of mixing the ink myself?
Custom inks are a good alternative if you don’t have all the the Pantone Basic Colors but you still want to put a specific Pantone color on your press. Some printers prefer ordering custom mix inks for every job they print, though this can get expensive (and, since custom ink mixes come in 1 lb cans, you’ll have a lot leftover).
We recommend going with custom ink particularly in these two situations:
- you’re going to be printing the same color ink over an extended period of time—for example, we ordered custom ink mixes of all the ink colors in our Smock and Bella Figura ink libraries so we can offer consistent color for all customer jobs. This way, if you order a custom ink of say 476U, you’ll know when you need to reorder it a year later it will look exactly the same.
- you’re printing with very light colors or a pastel ink. The formulas for such inks require very precise measurements (.2% yellow plus 99.5% trans white, etc.) and it’s difficult to mix these colors accurately yourself.
Which is a more environmental ink: soy ink, oil-based ink, or rubber-based ink?
We get asked a lot about soy ink from our customers, since there’s this general feeling that soy ink is THE greenest ink out there. That’s not really true. Soy sheet-fed ink has to be just 20% soy to be labeled a soy ink (the exact % of soy varies depending on the specific ink). Rubber-based and oil-based inks both have 20-30% vegetable-oil (soy and linseed). Linseed oil is the traditional letterpress ink vehicle: it’s what Gutenberg used when he first used ink. Also keep in mind that soy inks are really geared toward high speed printing and loaded with lots of driers—they’re usually very thin, liquidy inks, not ideal for letterpress. In our experience, soy inks don’t transfer well to letterpress printing, and you’ll get the same environmental impact from using oil-based or rubber-based inks.
L Letterpress
What kind of ink should I use when printing with KF152 polymer plates?
The L Letterpress comes with an oil based ink. You can continue to use those offered by the manufacturer but they are limited in colors. Boxcar Press sells a wide assortment of oil based and rubber based ink. We like rubber based inks for letterpress as they dry quickly on cotton papers and similar papers used for letterpress. Do not use any paints or water based inks on your photopolymer plates as they will soften and deteriorate the plates.
How can I achieve proper inking with this press?
When inking for letterpress, very little is always better. You only need a very light layer of ink on the top of your plates. We suggest the 2-step method of inking.
You will need these items:
- A new brayer (throw out the one that came with the machine and purchase a soft rubber brayer)
- The hard plastic sheet that comes with your machine – approx 6”.
- An ink knife
- Another piece of glass (or plastic) for part two of your inking – at least 8” wide and long.
Steps:
- Squeeze out an inch or two of ink from the tube. Or if you have a can of our Van Son ink, take your ink knife and scoop out a tablespoon of ink from the surface of the ink can. Place it on the 6” square and start to mix the ink to make it more fluid and smooth. Use a motion like scrambling eggs where you turn the ink over, pull the knife through and repeat. The ink should soften a little while you mix.
- Take the ink knife and pull a small ⅛” thick roll of ink from the mixture with your blade. Move this ink to the second piece of glass. Dab that ink across the glass until it’s about equal to the width of your brayer. Roll your brayer back and forth and side to side through the ink until it’s spread out evenly on the brayer. The ink may make a little noise like its snapping as you spread it out.
You will need very little ink for printing and this two step method means that you can control your ink coverage better. Using your roller bearers (polymer strips we ship you), lay the strips on both sides of your design plate. These support your brayer for smooth inking. Take your brayer and ink up your polymer plate – usually 1-2 rolls of the brayer. If your inking is fuzzy and on the sides of your impression, you have too much ink. Wipe off your brayer and roll it through the ink again.
With a little practice you will learn to control inking. To add more ink to your second inked glass, pull a small bit from the first mixing square – always 1/8″ thick roll or less.
How do I clean my machine, plates and brayer?
Use baby wipes, an old soft cotton t-shirt and odorless mineral spirits. The L Letterpress machine can be cleaned with baby wipes.
If you used any Van Son ink from a can, return any extra ink back to the can from the plastic ink square. Clean the two ink squares, both glass and plastic with baby wipes. Take one side of the cotton rag and wipe off the ink on your plates with a light stroke. Your ink is only on the surface of the plates so it should clean easily. If you have any ink residue left, take part of the cotton rag and get a small amount of the mineral spirits from the bottle. Wipe lightly on your plates and then turn the cloth over to a dry spot and wipe the plates again to remove any spirits. Do not use baby wipes or water on your plates.
Clean your brayer with baby wipes and then finish with a wipe of the rag with mineral spirits. You always want your brayer (roller) to be completely clean.
Do not use any water to clean your polymer plates, we can’t say this enough.
How do I hold my paper in place when I use this machine?
Use our Henry Gage Pins to hold your paper. They have a little plastic lip to hold your paper in place. Lay your paper in the position desired. Slide two of the Henry Gage Pins up to the longest side of your paper and one on the shortest side. When they are tight against the paper sides, adhere to the machine base. The Gage pins are re-usable.
Another option is to take one spare piece of the paper you are printing on. Cut out the paper to form an “L”. Adhere this L shape on the machine base with Removable double-sided tape so the inside of the “L” is the outside boundary for two sides of your paper to be printed. Tape a small piece of plastic over the corner of the inside angle of the “L”. Slide your paper up against the L shape so one corner should go just under the small plastic holder to hold it in place while the sides of the paper are tight against the inside of the L shape.
How do I properly place my photopolymer plate so it is aligned to print correctly in the right position on my paper?
Here is a printer tip we use on our presses. Set up your paper where you want it on your machine bed. Take a piece of scotch tape and make a loop. Place it on the front of your polymer plate. Stick that side down in the position desired on your paper. Peel off the protective blue covering of the plate adhesive on the back of your plate. Close the lid of your L Letterpress. Open it up and now your plate is securely in the place you need. Remove the tape loop. Close the lid again to make sure you are happy with your placement.
How do I design for printing on paper that is 100# and 200# weight?
We encourage you to read all our file prep tips for platemaking. A good design for letterpress will have crisp clean line art and fonts. If you are printing for 100# (or 110#) paper, you can gang up a lot of images together leaving ½” between them to cut with scissors. When you are ready to print, you can cut and paste and arrange your layout on the L Letterpress. When you print on this weight of paper, the edges of the plates will not leave marks on the paper.
However, when you are printing on the thicker weight 200# (or 220#) paper, you will need to set up your files a little differently. With this thicker paper, cut and pasting doesn’t work because the edges of the plates will also impress into the paper. Not the look you want. So you must design your whole plate completely so that everything is in its exact placement and the plate must be a fraction larger than your finished size of your paper. So if your paper is 5” x 7”, your finished plate must be 5 ⅛” x 7 ⅛”. The easiest way to do this is put registration marks at those dimensions so we can send a plate at the correct size. Cut off these marks when your plate arrives to a size so that the plate edges will be just outside your paper edge.
How do I learn to print with good results on the L Letterpress?
The L Letterpress does take a little learning and practice. Follow all of our instructions and read our blog on getting the best results from this machine.
The best piece of advice is to use scrap paper and a test plate while you are learning. Do not use the expensive paper you bought to print your wedding invites or baby announcements on. Use a similar weight card stock or less expensive papers to try everything out first. Remember there are always two sides to the paper so turn it over and try again. Here at Boxcar Press, we have makeready and set-up paper we use many times as we get everything just right. When you feel comfortable and ready to go ahead, switch to your real plates and paper and you’ll have a much better handle on the results. Don’t learn on paper and plates you are emotionally invested in while you are learning your way around letterpress. Remember you can have fun and be proud of something you made yourself for your special occasion.
Commercial Printing
What ink colors do you offer?
We can print in any ink listed in the Pantone Solid Uncoated Inks guide. Inks in our current library incur no additional charge. Custom inks (those not in our current library) are $50.00. This is a one-time charge. Let us know the color you have in mind and we can tell you if we have it.
Can you letterpress two sides of a sheet?
Yes! We strongly recommend using our heaviest weight papers (Crane’s Lettra 220# Cover or 4-ply Rising Museum Board) to minimize show through of impression from one side to the other. Images and position of images in relation to what’s on the other side will affect the depth of impression we can achieve without show through to the other side.
Do you offer rush service?
Yes, we offer three levels of rush service:
Yellow service – we ship 7 business days after PDF proof approval, add 15% to cost of order
Orange service – we ship 5 business days after PDF proof approval, add 35% to cost of order
Red service – we ship 3 business days after PDF proof approval, add 60% to the cost of the order This service is subject to availability so please call us with your specific needs and we will see if rush service is available for your order.
If I’m supplying paper or envelopes for you to print, how much do I need to send you?
Send us all the details on your project, as well as the name of the paper and envelopes you’d like to use. We also need the sheet size you plan to send. Once we have all that information we will figure how much paper we’ll use, taking into account what is needed for setup and waste and let you know how much stock you need to send for your job.
There are some things you should avoid. For instance, light ink letterpressed over dark paper does not work well; dark ink over light colored paper works better. Coated papers are not compatible with letterpress. Foil stamping is not compatible with all papers. Deckle edge papers are okay for 1 color letterpress but not for multiple colors; there is a high waste factor. Please call us for a consultation before you order paper or envelopes. We’ll need to know the paper type, sheet size and all your job specs in order to tell you how much paper or how many envelopes you should provide.
Do you offer design and or typesetting services?
Yes! Our designers can help turn your ideas into print-ready files suitable for our beautiful letterpress printing. Please call for a quote. Design service typically adds a week to your total production time. We ship 10 working days after you approve the final design proof.
In addition to letterpress, what other printing methods do you offer? Do you offer offset printing or foil stamping?
We have some offset printing capability. Most often we use our offset equipment to print a pattern or flood coat for an envelope liner or as a backing or background on a business card or invitation. We also foil stamp. Foil colors available are: Gold Shine, Silver Shine, Gold Matte, Silver Matte, Copper Shine, Red Shine, Blue Shine, Indigo Shine, Purple Shine, Fuchsia Shine, Forest Shine and Teal Shine.
Do you print on colored papers/envelopes?
Yes, we do print on colored papers and envelopes. See the papers and envelopes we stock. Some customers supply colored paper and envelopes which we can print on and we can special order some papers and envelopes.
There are some things you should avoid. For instance, light ink letterpressed over dark paper does not work well; dark ink over light colored paper works better. We now offer white digital addressing and return addresses on envelopes that are too bright or dark to accept letterpress inks. Foil stamping is also a good option for reply envelope addresses and return addresses.
How do I order samples?
Find our letterpress samples in our shop. We will be happy to send you a sample pack.
Does the print pricing include the cost of the plates?
Yes, it does. There will be additional charges if you make changes after plates have been made. We send you a final PDF proof before we make plates so please take advantage of that to check one more time for typos and misspellings.
What is the largest size sheet you can print?
22” x 30” is the largest sheet we can letterpress.
The largest paper size for a foil stamping job is 14 x 22 with the maximum foil image area being 12 x 16. If your piece is larger than 50 square inches please send it to us for review so we can make sure our presses can handle the impression.
What is the lead time?
Normal production time is 10 working days, with day 1 being the day after we receive your signed contract. We will email you a contract the day or day after we receive your order and you can return that to us via email or fax.
Do you offer wholesale pricing?
Yes! Please call us at 315-473-0930 to discuss your needs and we’ll be happy to prepare wholesale pricing tailored for your needs.
Do you print for stationery/invitation designers who need a letterpress printer and will resell the cards/invitations?
Yes, it’s a specialty of ours! Please contact us at printing@boxcarpress.com and we will be happy to introduce you to Boxcar Press and provide you with information, samples and pricing. We can also be reached by phone at 315-473-0930.
What are your stock papers?
Crane’s Lettra 110# and 220# Cover in Fluorescent White, Pearl White and Ecru. (We can also provide you with the matching envelopes and 32# Writing paper from the Lettra line.)
Rising Museum Board – White and Black – 2 ply and 4 ply
Mohawk Loop Smooth 160# DTC – White and Ivory. Both are 100% PCW! Chipboard – 28 pt and 60 pt Mohawk Loop Antique Vellum – 80# cover
Do you ship internationally?
Supplies: We ship supplies to Canada via UPS Standard or UPS Worldwide Saver and US Postal Service.
We ship international orders (outside of Canada) via UPS Worldwide Saver and US Postal Express Mail.
We think our online ordering system is pretty nifty but of course you can phone in your order to us by calling 315-473-0930. We love to talk to our customers.
Platemaking: We ship platemaking orders to Canada via UPS Standard or UPS Worldwide Saver and US Postal Service. We can ship Worldwide Saver to any international location or opt to use the US Postal Express Mail. These options are all at the click of a button through out platemaking site.
Printing: Yes, we love working with international clients and sending off printed letterpress beauties to destinations far and near.
Do you offer edge painting (by itself for supplied printed pieces or for pieces you print)?
We can edge paint cards that we print here but do not offer this service for pieces prepared elsewhere. We do not recommend edge painting when there is a bleed image.
How do I obtain pricing? Is there a letterpress printing price sheet you can send to me?
Fill out this form with all the particulars (quantity, number of ink colors, one or two sided printing, size, type of paper and so forth) for each piece and a pdf of your design, if available. We will be happy to provide you with a quote. If you are a designer or store who will be selling the pieces to your customers, let us know and we can prepare a wholesale price guide for you.
What file formats do you accept?
We prefer press quality PDF files and also accept Adobe Illustrator files and EPS files. (If sending an eps file please also send a pdf for reference.)
How do I submit artwork for print jobs or quote requests?
Send an email to printing@boxcarpress.com. If the file is too large try using yousendit.com. (Boxcar Press can accept up to 25MB via email but your email capacity may not allow a file that large to be sent.) Before you send, make sure you have outlined your type, included actual crop marks or a cut rule and that your files are set in solid, uncoated Pantone colors.
When do I need crops and / or registration marks?
You will need crop marks if you are sending the files to us for printing. This will aid us in setting up your files into its final layout. While we will have the info on the final size of your printed piece, your crop marks in your file will help us determine that we are including all the elements you intended and in their proper place. This is especially important when your design will bleed off the page. How to place crop marks on your file, in Illustrator will depend on your CS version.
In CS3 or older – Filter > Create > Crop marks
In CS4 and newer – Effect > Crop marks
If you created your design in Illustrator and set up your artboard to measure the finished size of your printed piece, the crop marks will be outside the artboard. You will need to save your file with an eps extension so the crop marks will be included. You can then save the file as a PDF and send us both EPS and PDF. If you save as an AI extension, the crop marks were left off outside your artboard and not included in your file.
If you created your design on a larger artboard, use the rectangle tool to draw a box the desired size around your design. It will temporarily block your design until you go to your Color window and click on the white square with the red diagonal stripe. Using the selection arrow, move your box around until it’s the correct size and in the preferred place of your design. Add crop marks and save as a PDF.
How do I set up my files for 2-color printing?
The easiest way of setting up a 2-color file in an image editing program, such as Illustrator or InDesign, is to set your first color’s objects in either 100% of a color channel in CMYK mode where the three other color channels not used are set to 0%. The second color would then use 100% of a different color channel. For example, your first color’s objects may be 100% black and your second color’s objects are set to 100% cyan. If you are using this method, be sure to let us know which color channel corresponds to the ink colors you have chosen for your printing.
Our Preferred Method: If you are very comfortable with Illustrator or InDesign, you may use Pantone Swatches from the Swatch Color Libraries palette in lieu of using 100% of individual CMYK color channels. We recommend using swatches from the Pantone Solid Uncoated color book.
Why can’t you rush my foil job?
Each foil stamped piece requires us to create a custom die that will be used in the foil stamping process. This die-making process is more time intensive than making plates for letterpress and doesn’t allow for a rush turnaround.
What’s the biggest piece I can print foil on?
We can print up to a 14 x 22 sheet with a maximum foil image area of 12 x 16.
Do foil stamped pieces have any additional handling or mailing concerns?
We have conducted mailing tests on foil stamped invitation sets and postcards with terrific results. There are no additional handling or mailing concerns for foil stamped pieces.
Are foil pieces recyclable?
Yes, you can place your foil pieces in your recycling bins along with your other paper products. And by the way, there are no solvents, inks, or vapors associated with foil stamping.
Is it true that foil does not print very crisply?
Art and type tends to look thicker or bolder in foil stamping, especially on thicker papers. However, we have done extensive testing with our dies to maximize our printing quality, and the type of foil that we use creates beautiful images with clean release.
What sorts of designs are appropriate for foil?
Overall, most designs that are appropriate for letterpress will translate well to foil stamping. Each customer file that is submitted is reviewed by our prepress team, who are experienced in the foil die making process. Any design that contains areas of intricate detail, thin line fonts, or reverses will be addressed by our prepress personnel and we’ll contact you with any concerns that need addressing.
Can you mix foil and letterpress in a job?
Yes you can – and what a wonderful combination!
Stock Papers & Envelopes
Do you print on colored papers/envelopes?
Yes, we do print on colored papers and envelopes. See the papers and envelopes we stock. Some customers supply colored paper and envelopes which we can print on and we can special order some papers and envelopes.
There are some things you should avoid. For instance, light ink letterpressed over dark paper does not work well; dark ink over light colored paper works better. We now offer white digital addressing and return addresses on envelopes that are too bright or dark to accept letterpress inks. Foil stamping is also a good option for reply envelope addresses and return addresses.
If I’m supplying paper or envelopes for you to print, how much do I need to send you?
Send us all the details on your project, as well as the name of the paper and envelopes you’d like to use. We also need the sheet size you plan to send. Once we have all that information we will figure how much paper we’ll use, taking into account what is needed for setup and waste and let you know how much stock you need to send for your job.
There are some things you should avoid. For instance, light ink letterpressed over dark paper does not work well; dark ink over light colored paper works better. Coated papers are not compatible with letterpress. Foil stamping is not compatible with all papers. Deckle edge papers are okay for 1 color letterpress but not for multiple colors; there is a high waste factor. Please call us for a consultation before you order paper or envelopes. We’ll need to know the paper type, sheet size and all your job specs in order to tell you how much paper or how many envelopes you should provide.
Pages
Do I send my files to size or scaled down?
You will need to send your files at 100% scale. We do not resize, scale up or down, or rotate any artwork. We highly recommend using the ruler feature available in Adobe Illustrator, Photoshop and InDesign to check your work to see if it is the size you want.
When exporting a PDF from Adobe Illustrator or Adobe InDesign, please double check to make sure it is the correct size by either re-opening it in Illustrator or placing it in InDesign to check the actual dimensions of your file. In InDesign you can use the Rectangle Frame tool to draw a box around your images/text to measure.
In Photoshop, use the Image Size tool to check your size. Saving your file as a .TIF locks your image size.
How do I select spot colors in my file instead of CMYK?
Spot color or Pantone swatch colors can be applied to objects via the Pantone Swatch Color Book or Spot color library found in Adobe Illustrator. For Adobe InDesign, Spot Colors are more easily accessed. First, activate the Swatch palette by selecting WINDOW>Swatches.
Notice the fly-down menu icon in the upper right-hand corner of the Color palette? The icon looks like a small downward black triangle with four small lines next to it. Clicking on this will open a fly-out window menu. Hover your mouse over “Open Swatch Library” to open another fly-out window menu of all the color books. Very carefully move your mouse to hover over “Color Books”, which will open up another fly-out menu. You’ll see a lot of different color book options, but we recommend using “PANTONE solid uncoated”. Clicking on this color book will open a new window filled to the brim with a plethora of color
Swatches that Pantone has to offer.
Finally, assign all your file’s artwork, objects, and text to their appropriate Pantone Swatches or spot colors.
In Indesign, open the swatch window. click on the downward black triangle to the right and choose New Color. This opens a New Color Swatch Window. Select Spot as color type and Pantone Solid Uncoated as the Color Mode. The PMS colors will load for you to select and click OK.
How do I outline fonts?
While either in Adobe Illustrator or InDesign, select all your text that needs to be outlined using the black arrow tool (the default arrow tool). Next, select TYPE>Create Outlines. This will automatically convert your text into vector shapes. Your text will temporarily look bolder and be highlighted in blue. Click anywhere on your artboard that is white to deselect your text and its appearance will look normal again.
What is the lead time?
Normal production time is 10 working days, with day 1 being the day after we receive your signed contract. We will email you a contract the day or day after we receive your order and you can return that to us via email or fax.
Do you print for stationery/invitation designers who need a letterpress printer and will resell the cards/invitations?
Yes, it’s a specialty of ours! Please contact us at printing@boxcarpress.com and we will be happy to introduce you to Boxcar Press and provide you with information, samples and pricing. We can also be reached by phone at 315-473-0930.
What file formats do you accept?
We prefer press quality PDF files and also accept Adobe Illustrator files and EPS files. (If sending an eps file please also send a pdf for reference.)
How do I submit artwork for print jobs or quote requests?
Send an email to printing@boxcarpress.com. If the file is too large try using yousendit.com. (Boxcar Press can accept up to 25MB via email but your email capacity may not allow a file that large to be sent.) Before you send, make sure you have outlined your type, included actual crop marks or a cut rule and that your files are set in solid, uncoated Pantone colors.
How should I upload corrected files?
Sometimes we may notify you that your files have an error and need correcting. Follow the instructions to make those corrections and rename your file, preferably with the words “New”, “Revised”, or “Corrected” in the file name. Please don’t upload a changed file with the same name as the original file as we won’t be able to tell it’s a replacement and new file.
Re-upload new files to your current platemaking ticket. Log in to Boxcarpress.com with your username and password. Click on the applicable ticket to upload or drag and drop the new revised file.
You can only upload files to your ticket if your platemaking ticket’s status is either set as “Received”, “Pending” or “On Hold”. We will see new files and get to work to process your plates.
If you find that your ticket’s status is “In Platemaking”, you will need to call us at 315-473-0930 to see if it is possible to still add corrected or revised files.
If your ticket status is “Billing Complete”, “Order Complete” or “Shipped”, your ticket is unable to be altered.
Do I send my files reversed for your processing?
No. Please send your artwork and text right-reading as you want it to appear as the final print. We will make a film negative here at Boxcar Press for you. However, if you are planning to use your files in a different process than printing, please call us to discuss how best to prep your files.
When do I need crops and / or registration marks?
You will need crop marks if you are sending the files to us for printing. This will aid us in setting up your files into its final layout. While we will have the info on the final size of your printed piece, your crop marks in your file will help us determine that we are including all the elements you intended and in their proper place. This is especially important when your design will bleed off the page. How to place crop marks on your file, in Illustrator will depend on your CS version.
In CS3 or older – Filter > Create > Crop marks
In CS4 and newer – Effect > Crop marks
If you created your design in Illustrator and set up your artboard to measure the finished size of your printed piece, the crop marks will be outside the artboard. You will need to save your file with an eps extension so the crop marks will be included. You can then save the file as a PDF and send us both EPS and PDF. If you save as an AI extension, the crop marks were left off outside your artboard and not included in your file.
If you created your design on a larger artboard, use the rectangle tool to draw a box the desired size around your design. It will temporarily block your design until you go to your Color window and click on the white square with the red diagonal stripe. Using the selection arrow, move your box around until it’s the correct size and in the preferred place of your design. Add crop marks and save as a PDF.
How do I set up my files for 2-color printing?
The easiest way of setting up a 2-color file in an image editing program, such as Illustrator or InDesign, is to set your first color’s objects in either 100% of a color channel in CMYK mode where the three other color channels not used are set to 0%. The second color would then use 100% of a different color channel. For example, your first color’s objects may be 100% black and your second color’s objects are set to 100% cyan. If you are using this method, be sure to let us know which color channel corresponds to the ink colors you have chosen for your printing.
Our Preferred Method: If you are very comfortable with Illustrator or InDesign, you may use Pantone Swatches from the Swatch Color Libraries palette in lieu of using 100% of individual CMYK color channels. We recommend using swatches from the Pantone Solid Uncoated color book.
Can you explain how you calculate the file dimensions for billing
Here is how we compute dimensions – we gang all your files up together and draw a box around the “black” part – the images and text. Now we know the length and the width. We multiply these two numbers together and this is your square inches total. We then multiply this square inch number by your square inch price of $0.62/sq inch or $0.67/sq inch.
Example:
9″ x 8″ is your “black part”
9” x 8” = 72 sq inches x $0.67 = $50.40
If your file has crop marks, we measure outside the crop marks. So if you don’t need crop marks, consider leaving them off to save a little cash.
Can you explain the same day rush service and fee?
Boxcar Press has a pretty fast platemaking turnaround service with our one business day turnaround. But if you have an even greater need for speed, consider our Same Day Rush Service. If you create your job ticket, upload your files before 1 pm EST, and choose Same Day, we’ll get your files out the door to arrive the next Business Day via UPS. Of course, speed comes at a price, the fee for Same Day Rush starts at $45 or 40% (whichever is greater) plus the regular cost of the plate plus your overnight shipping costs. Your minimum cost for a Same Day Rush plate is $75 before shipping and goes up from there.
So, we encourage you to make use of the one day turnaround as much as possible. Create your job ticket and upload your files before 5:30 pm EST and we’ll ship on the next business day, assuming your files are in tip-top A1 shape. File corrections may delay your shipping.
Do you print on colored papers/envelopes?
Yes, we do print on colored papers and envelopes. See the papers and envelopes we stock. Some customers supply colored paper and envelopes which we can print on and we can special order some papers and envelopes.
There are some things you should avoid. For instance, light ink letterpressed over dark paper does not work well; dark ink over light colored paper works better. We now offer white digital addressing and return addresses on envelopes that are too bright or dark to accept letterpress inks. Foil stamping is also a good option for reply envelope addresses and return addresses.
My letterpress plates are starting to curl. How do I flatten them out?
Like our skin, plates can be affected by the room temperature, humidity, and age. When humidity levels are low, the plates can look and feel brittle. With the passage of time, the thinner polymer on the plate edges are pulled towards the denser polymer text and images on the front—this causes curling. With a life expectancy of up to 1 year or more, polymer plates do age, but these simple steps can hydrate your plates and give them extra longevity.
Step 1. Place your plate back in your platemaking washout system for up to ½ a minute (or, if you don’t have a washout unit, simply immerse in water). We suggest room temperature for a quick dunking. A ½ minute may only be necessary if your plates are severely curled.
Step 2. Sponge off the water and place back in the drying oven of the platemaker for 5-10 minutes. If you don’t have a platemaker, use a hair dryer to warm the plate and make it more pliable. Placing your plate in a box and blowing the hair dryer into the box will keep the warm air more contained and warm the plates more effectively.
Step 3. After the plate warms and starts to become more pliable, place the plate in its bag and set a heavy object on it to keep the flattened shape.
This should help your plates relax so you can adhere them to your base for additional print runs.
Here’s some final advice:
- if using a hair dryer, take care to avoid putting it too close to the plates.
- be patient, as warming the plates takes time.
- watch that you don’t handle your letterpress plates too roughly after the wash and during drying so your relief images don’t chip.
- remember to store your plates flat out of direct light and in a bag so that fluctuations in humidity don’t affect the polymer.
- check your adhesive backing, to see if the adhesive needs to be re-applied to the back of your polymer plate for a secure hold on your base.
How do I take advantage of the free 2 day shipping?
Boxcar Press offers free two day shipping for platemaking orders that are over 120 square inches as of August 15th, 2014. If your order qualifies, this option will appear as the default shipping choice.
Please remember these details about this service:
- Two day service is ground service for those already within our 1 or 2 days service area (New York state, the Northeast to Maine, down to Virginia, and parts of Wisconsin, Illinois and Kentucky).
- If your usual UPS ground is 3 day – 6 days, you will receive UPS 2 day Air.
- If you have selected any overnight air services for shipping, we will NOT downgrade for free 2 day service. We will believe that you really need the faster overnight service.
- If you really do need 2 day Air service, please choose the 2 day Air and don’t wait for us to upgrade you from ground or a slower service. It’s hard to make UPS deliver faster once it’s out for shipping.
- Free 2 day air applies to business days and not Saturday delivery.
How can I check the progress of my order?
Log on to your account in platemaking. It will take you to your Orders page where the current status will be visible.
Status Explanations:
- Pending – Your order has been started but all the steps have not been completed. This requires further action on your part.
- Received – Waiting for us to review your files.
- On hold and awaiting action on your part.
- On Hold No Files Received – Please try uploading again or call for assistance.
- On Hold Bad Files – Your files need attention. You will receive an email indicating your order is on hold with the problem and asking you to correct and upload new files. File errors may include your files measure too large to plate, not in correct color mode, lines or dots too thin, files are in grayscale, etc.
- On Hold – Credit Card declined or expiration is passed. There is a problem with your payment, please contact us.
- In Platemaking – We are in production making your films to make plates. Your ticket is locked as we are moving ahead.
- Billing complete – Your platemaking job is billed and awaiting shipping.
- Shipping Complete – We have shipped and still need to Invoice your order.
- Order Complete – We closed out your order as we have created a shipping label and your package is out the door. The day your order was completed was the day it shipped.
After I scan my artwork that I want to letterpress print, what do I do now?
Your scanner will likely save your image as a grayscale.jpg. Many scanners will only allow you to scan up to 300 dpi. If you can scan higher, choose 600 dpi. You have some options now.
If looking for the crispest and cleanest impression, you will need to convert the file to black and white only (no grey pixels). You have two methods depending on what computer software you have available. If you only have Photoshop, you will need to convert your file to one that is in image mode of bitmap. If your image dpi is currently 300 dpi, you can choose Image > Image Size and change your dpi to 600 or higher without changing the inches. Your file will temporarily be quite large but you will then save as a .TIF with LZW compression and this will resize it to something smaller and more manageable. A higher DPI can help with preserving your details and smoother pixelation while bitmapping. For exact steps to Image Mode of Bitmap, see our File Prep Tips.
If you have both Photoshop and Illustrator, you can convert your image to image mode of bitmap as directed above, then place your TIF into Adobe Illustrator, and convert the file to a vector art file via the Live Trace option. This does not always work with all files to give satisfactory results, so with practice, you will learn to recognize which files will give you a vector result you like. After converting to vector, save the file as a PDF or EPS for upload.
I want to keep my files in grayscale, how can I make them look their best?
Grayscale is a range of shades of black on a spectrum from 1 to 100. Light gray is in the lower spectrum and darker grays are in the higher spectrum. While 100% black images and text will produce crisp line art and is the norm for letterpress, sometimes you may want to print something where you want to see all the details and subtleties of the shading.
If you are trying to print a photographic image, it’s best to choose one that has areas that provide high contrast between light and dark, that is, the photo has details that are both darker gray in the upper ranges (70 to 100% of black) and lighter gray in the lower ranges (5% to 35% of black). This contrast will give the most depth and interest to the photo. If your photo has mostly shades of black in a similar range (30 – 60% of black), it will look muddy to the eye because it’s harder to discern the shading without a lack of contrast. Experimenting with the image in Photoshop by changing levels of black or adding brightness and contrast can help some with this.
If you are printing a scanned image, where you want to keep the tonal imagery, you can send the file as grayscale and we’ll apply a line screen to it. Your image will be a large shape with the tones created as little dots on the surface of the plate. The films are very sensitive and will capture shades of black down to 5%. So if your background has some color, it may be picked up by the film and show on your plate.
Halftones and grayscale images can be challenging to print with relief plates on the commonly used uncoated papers of letterpress. Call us to discuss your particular image and the results you want to achieve.
It’s not necessary to reverse your files before submitting.
We need your files and proofs to appear the way you want your final design to print – commonly called right-reading (no backward text or images). When we create your film negatives, our software does the reversing to create proper negatives, so leave that part up to us.
In Illustrator, if you want crop marks on your plate, create crop marks, not crop areas!
While using Adobe Illustrator, you will first need to create a rectangle by using the marquee tool (M) in your standard tool palette located on the left-hand side of your screen. Create the rectangle so that its dimensions are your piece’s final trim down size (e.g such as 5.5″ x 7″ for an invitation, etc). Next, while the rectangle is still selected, drag it to its proper location with respects to the artwork. This location should be the correct position intended for the crop marks. Please note that we do not add crop marks to any file at Boxcar Press, as we do not know where or what your intended trim down size is.
While the rectangle is still selected, please select EFFECT>Crop Marks to create the correct type of crop marks in Illustrator. If you need to shorten the length of the crop mark lines or thicken the line weight, you will need to expand the crop marks by selecting OBJECT>Expand or OBJECT>EXPAND APPEARANCES.
If your file has linked images, embed them in Illustrator or Export them as a PDF from InDesign.
Before sending your Illustrator files to us, embed all linked images (an option in the Links palette). If linked images aren’t embedded, they can give an error message that your links are missing and we can’t output your plates! With InDesign, export your file as a press ready PDF.
When using Illustrator, how do I outline my fonts and why is it important?
Sending all your fonts packaged is not fail-safe: all needed fonts aren’t always provided, or all your fonts may not be recognized when we open your file, causing shifting and changes in your design. On the other hand, outlining fonts is fool-proof, safe, and ideal. So outline your fonts! In Illustrator, you do this by selecting TYPE>Create Outlines. This will automatically convert your text into vector shapes. Your type will temporarily look bolder and be highlighted in blue. Click on any white area of your file and it will look normal again.
In Illustrator, the only black your submitted file should use is 100% CMYK black (CM and Y are 0%)
When opening any new document in Illustrator, choose File > Document Color mode > CMYK. To Check this before submitting your file for upload – in illustrator versions CS4 and CS5, you can open your Output-Separations Preview window. Click on the drop down window showing Off and select Separations. Click off the black eye and everything left showing on your file is not in 100%K. If you select a part of your file that is left, and look at your color palette, anything that shows a percentage of C,M, or Y needs to be corrected. To correct this – go to Select > Same > Fill (or Stroke). It should highlight everything that looks like black (but isn’t). Than go to the color palette and using the eyedropper, click on the black part of the bar (far right). The C, M, and Y will go to 0% and the K should go to 100%. Now this part of the file should disappear because it is correctly set to 100%K.
Don’t use a jpeg or save as a bmp file for your images!
Our favorite image mode is a .tiff. Or send us vector art images (made in Illustrator or Freehand) instead of raster images (made in Photoshop). Jpeg files will create low-quality letterpress plates that will make you unhappy; its file format is best intended for the web. Files that end in .bmp can also give unwanted results by saving as the wrong size and are also lower quality.
Do foil stamped pieces have any additional handling or mailing concerns?
We have conducted mailing tests on foil stamped invitation sets and postcards with terrific results. There are no additional handling or mailing concerns for foil stamped pieces.
Home made presses and Instructable Presses – I’ve built a homemade press and would like to know the best advice for printing with it.
We applaud innovators and inventors, where would printing be without it? We offer two of the most common homemade press designs from the internet.
Links to homemade press info
Book Press Design
Hydraulic Jack Press
To print with a home-constructed press, here are the items suggested for printing:
- we offer our Boxcar Press platemaking services. Our KF152 photopolymer plate with the adhesive backing works beautifully for homemade presses.
- Inking with a homemade press requires a soft rubber brayer (6” minimum suggested) that can be purchased from your arts store or McClain Printmaking.
- Plate strips to serve as roller bearers for your brayer when inking. Just ask us to send you a few plate strips when placing your order.
- Boxcar Press Ink Knife.
- Henry Gage Pins for paper registration.
- Printing Inks – for best results -Rubber based or oil based from Boxcar Press.
- Old cotton tshirts for clean up rags.
- Extra 1 or 2 sheets of glass or smooth acrylic for inking.
Before you start printing, we encourage you to read our blog posting which has some instructional tips on inking on home machines.
Homemade presses are better suited for light impression printing. Suggested papers and where to buy are:
- Cotton and bamboo papers from Legion Paper’s letterpresspapers.com
- Crane’s Lettra from Neenah Papers
Enjoy your experience letterpress printing on your homemade press. Your results will be something you can be proud of.
It’s a Crazy Friday and I have to print over the weekend. Can you help?
We can help! Get your files into us by 1 p.m. EST on Friday (and make sure your design files are prepared just right!). Choose our rush service which means we’ll ship your plates Friday. Choose overnight AM for shipping and Saturday delivery and you’ll have your plates in hand by Saturday, noon. Hooray!
Do you offer rush service?
Yes, we offer three levels of rush service:
Yellow service – we ship 7 business days after PDF proof approval, add 15% to cost of order
Orange service – we ship 5 business days after PDF proof approval, add 35% to cost of order
Red service – we ship 3 business days after PDF proof approval, add 60% to the cost of the order This service is subject to availability so please call us with your specific needs and we will see if rush service is available for your order.
If I’m supplying paper or envelopes for you to print, how much do I need to send you?
Send us all the details on your project, as well as the name of the paper and envelopes you’d like to use. We also need the sheet size you plan to send. Once we have all that information we will figure how much paper we’ll use, taking into account what is needed for setup and waste and let you know how much stock you need to send for your job.
There are some things you should avoid. For instance, light ink letterpressed over dark paper does not work well; dark ink over light colored paper works better. Coated papers are not compatible with letterpress. Foil stamping is not compatible with all papers. Deckle edge papers are okay for 1 color letterpress but not for multiple colors; there is a high waste factor. Please call us for a consultation before you order paper or envelopes. We’ll need to know the paper type, sheet size and all your job specs in order to tell you how much paper or how many envelopes you should provide.
Which is a more environmental ink: soy ink, oil-based ink, or rubber-based ink?
We get asked a lot about soy ink from our customers, since there’s this general feeling that soy ink is THE greenest ink out there. That’s not really true. Soy sheet-fed ink has to be just 20% soy to be labeled a soy ink (the exact % of soy varies depending on the specific ink). Rubber-based and oil-based inks both have 20-30% vegetable-oil (soy and linseed). Linseed oil is the traditional letterpress ink vehicle: it’s what Gutenberg used when he first used ink. Also keep in mind that soy inks are really geared toward high speed printing and loaded with lots of driers—they’re usually very thin, liquidy inks, not ideal for letterpress. In our experience, soy inks don’t transfer well to letterpress printing, and you’ll get the same environmental impact from using oil-based or rubber-based inks.
When do you recommend I order a custom ink instead of mixing the ink myself?
Custom inks are a good alternative if you don’t have all the the Pantone Basic Colors but you still want to put a specific Pantone color on your press. Some printers prefer ordering custom mix inks for every job they print, though this can get expensive (and, since custom ink mixes come in 1 lb cans, you’ll have a lot leftover).
We recommend going with custom ink particularly in these two situations:
- you’re going to be printing the same color ink over an extended period of time—for example, we ordered custom ink mixes of all the ink colors in our Smock and Bella Figura ink libraries so we can offer consistent color for all customer jobs. This way, if you order a custom ink of say 476U, you’ll know when you need to reorder it a year later it will look exactly the same.
- you’re printing with very light colors or a pastel ink. The formulas for such inks require very precise measurements (.2% yellow plus 99.5% trans white, etc.) and it’s difficult to mix these colors accurately yourself.
My chase is rocking while it’s laying flat (before I try any lockup!). What should I do?
First, figure out why your chase isn’t lying level.
- Possibility 1. Your chase might have cracked some time in the past then was welded to repair it. If this is the case, you may need to file or shave off any excess metal that might interfere with your chase being level.
- Possibility 2. You may have a low spot on your chase. You’ll want to add a shim (a small piece of metal) to the chase to level things off.
In either case, use a professional machinist. They can expertly grind down your chase if needed to create a smooth surface, or they can add a shim to your chase to level things out.
What’s the maximum size polymer plate I can print on my base?
Your maximum plate size is actually the size of your base — your photopolymer plates can go right up to the edge of your base. Obviously your relief images and text should not hang over your edge. This is true for both magnetic bases and the Boxcar Base. If you need a little more base for occasional projects, consider a Boxcar Base scrap to add that extra ½” – 1”. Read more about maximum base size.
What happens if you use a Deep Relief Boxcar Base on a Vandercook, Heidelberg Cylinder, or Heidelberg Windmill–some info you need to know?
The Deep Relief Boxcar Base does work fine on cylinder presses or the Windmill — since its base + plates + adhesive still equals a type high surface (.918”) and that is the critical issue for all bases and plates. There is the advantage of holding a slightly finer line with a standard plate but let’s be realistic when we compare. The 94/95 plates will hold a 0.25pt line and the 152 plates will hold a 0.35pt line (when talking inches that is a .0035″ line compared to a .0048″ line. Not much to quibble about. We just like the way a 94 plate works on our windmills with our standard base and that is how we started years ago in the infancy of Boxcar Press. That said, some printers who use the Deep Relief base on their platen presses already may want to use the Deep Relief base on, say, their Vandercook too, so that both presses can share plates — this is totally okay too.
How are plastic-backed and steel-backed plates different?
When mounted on their appropriate bases, plastic-backed and steel-backed photopolymer plates both create type-high surfaces for letterpress printing. Both plate types are recyclable. We’ll talk about some of their differences below.
Plastic-backed polymer plates are flexible, transparent, easy to cut, and mount onto a Boxcar Base for simple registration. You’ll find these plates:
- can be cut with scissors in both their unexposed and exposed forms.
- are transparent, meaning you can see the Boxcar Base’s grid through your plate. This allows for simple alignment of your plates to your base: For perfect registration, align a certain element of your plate to the grid: take a horizontal or vertical element in your plate (this could be your registration marks, or a horizontal line in your artwork) and line it up to the grid.
- eliminate plate creep (steel-backed plate users sometimes experience this while on press). The plastic-backed plate’s adhesive is shift resistant, giving you a secure, strong hold during printing (but the adhesive also peels up easily when you’re done printing)
- allow printers to print two color jobs using one plate if the design elements don’t touch. Cut out the second color images/text with a craft knife or scissors and set aside. Print color #1. Set your second color images back in place and pull up the first plate for color #1—perfect registration!
- allow designs to be ganged up on plates closely to save space (and money).
- are reusable. You will be able to reuse the plate many times if you keep the adhesive protected with the blue overlay after printing. You can also replace adhesive for even more extended plate use.
- more prone to curling, especially with large solid areas over time.
- If purchasing unexposed plastic-backed polymer plates, you’ll also want to purchase film adhesive to adhere your plates to your base. If we’re making your plates for you, we include adhesive.
- are suitable for metal clay jewelry.
- Over here at Boxcar, we use plastic-backed plates for all our printing (the Jet 94 Clear plate paired with the Standard Boxcar Base).
Steel-backed polymer plates are compatible with magnetic bases, generally the Patmag or Bunting base. Steel-backed polymer plates:
- require cutting with a metal shear or heavy-duty trimmer. You can use tin snips, though you may end up with kinks in your plate, as tin snips won’t cut as cleanly.
- sometimes shift and creep on your base during printing. Magnets in the base effectively hold a plate from peeling but cannot always hold a plate from moving side to side. The cylinder or rollers of a press can move steel-backed plates out of register (that’s “plate creep”).
- are not transparent. Because magnetic bases aren’t gridded (and you can’t see through these plates), you’ll have to align your plates to your base with a line gauge and possibly registration marks. This works, but it is more time consuming and there’s more room for error.
- are rigid, meaning they don’t bend well. This inflexibility can cause plates to kink and warp when handled so that their corners may work up while on press. Steel-backed plates are, however, very durable and not prone to curling over time.
- can be more expensive than plastic-backed plates because you may require registration or crop marks which makes for a larger plate.
- are difficult to get on and off the base, especially when the base has inlaid magnets. When placing metal plates on a magnetic base, keep fingers clear so they don’t get pinched when the magnet grabs. When taking your plate off the base, try an ink knife to pry under the plates to release from the magnetic base.
- have sharp edges, which dictate extra care when handling.
- can be used for a wide range of printing and impression—on leather, metal clay jewelry, ultra heavy-weight paper stocks. Steel-backed plates can also be used on etching presses when relief printing is desired. They are not suitable for high temperatures of foil stamping though.
What’s the smallest size plate that I can print on my Boxcar Base?
The Boxcar Base is guaranteed to hold plates in register, provided they are standard thickness plastic-backed plates mounted with our film adhesive. But plates that are smaller than .25 square inches may drift under certain conditions due to their small area of contact with the base. Make sure your plates are larger than .5″ by .5″, even if your image is very small.
Why can’t you rush my foil job?
Each foil stamped piece requires us to create a custom die that will be used in the foil stamping process. This die-making process is more time intensive than making plates for letterpress and doesn’t allow for a rush turnaround.
If you want a lineart image, use bitmap mode (don’t use a linescreen or halftone)
Most of the time, if your file contains an image, you’ll want that image to be in bitmap mode for a nice clean bite into your paper. Otherwise your image will produce a halftone, which means your image will be made up of tiny dots on the surface of your plate.
If you zoom in on your image and it is made up of tiny grey and black pixels, it’s in grayscale. We want your images all in black pixels.
You can correct this by:
- Opening your image in Photoshop and selecting Image > Mode > Grayscale.
- Select Yes if a window asks about discarding color.
- Then Select Image > Mode > Bitmap. A window will pop up looking for info – use a resolution of 600-1200 dpi and an output method of 50% threshold.
- Save your files as a tif (with LZW Compression) and send us the tif. Or insert the Tif into your Illustrator or InDesign file.
Images in higher resolution (600-1200 dpi) will give better, finer results than images in lower resolutions (72-300 dpi). If your images lose a lot of detail, you can either re-scan or adjust your levels of black. A quick explanation about the 50% threshold method. A grayscale image is made up of pixels from 1 – 100% black. When you select 50% threshold, you are telling the computer to change all pixels less than 50% black to be white and all pixels greater than 50% black to be black. So sometimes adjusting the levels of gray pixels under 50% to a little darker and over the 50% mark will keep more details in your image. We suggest experimenting with the following: Image Adjustments > Levels or Image Adjustments > Brightness and Contrast. This may give you more pleasing results in your final bitmap tif.
Are foil pieces recyclable?
Yes, you can place your foil pieces in your recycling bins along with your other paper products. And by the way, there are no solvents, inks, or vapors associated with foil stamping.
What sorts of designs are appropriate for foil?
Overall, most designs that are appropriate for letterpress will translate well to foil stamping. Each customer file that is submitted is reviewed by our prepress team, who are experienced in the foil die making process. Any design that contains areas of intricate detail, thin line fonts, or reverses will be addressed by our prepress personnel and we’ll contact you with any concerns that need addressing.
Can you mix foil and letterpress in a job?
Yes you can – and what a wonderful combination!
How do I learn to print with good results on the L Letterpress?
The L Letterpress does take a little learning and practice. Follow all of our instructions and read our blog on getting the best results from this machine.
The best piece of advice is to use scrap paper and a test plate while you are learning. Do not use the expensive paper you bought to print your wedding invites or baby announcements on. Use a similar weight card stock or less expensive papers to try everything out first. Remember there are always two sides to the paper so turn it over and try again. Here at Boxcar Press, we have makeready and set-up paper we use many times as we get everything just right. When you feel comfortable and ready to go ahead, switch to your real plates and paper and you’ll have a much better handle on the results. Don’t learn on paper and plates you are emotionally invested in while you are learning your way around letterpress. Remember you can have fun and be proud of something you made yourself for your special occasion.
How do I design for printing on paper that is 100# and 200# weight?
We encourage you to read all our file prep tips for platemaking. A good design for letterpress will have crisp clean line art and fonts. If you are printing for 100# (or 110#) paper, you can gang up a lot of images together leaving ½” between them to cut with scissors. When you are ready to print, you can cut and paste and arrange your layout on the L Letterpress. When you print on this weight of paper, the edges of the plates will not leave marks on the paper.
However, when you are printing on the thicker weight 200# (or 220#) paper, you will need to set up your files a little differently. With this thicker paper, cut and pasting doesn’t work because the edges of the plates will also impress into the paper. Not the look you want. So you must design your whole plate completely so that everything is in its exact placement and the plate must be a fraction larger than your finished size of your paper. So if your paper is 5” x 7”, your finished plate must be 5 ⅛” x 7 ⅛”. The easiest way to do this is put registration marks at those dimensions so we can send a plate at the correct size. Cut off these marks when your plate arrives to a size so that the plate edges will be just outside your paper edge.
How do I properly place my photopolymer plate so it is aligned to print correctly in the right position on my paper?
Here is a printer tip we use on our presses. Set up your paper where you want it on your machine bed. Take a piece of scotch tape and make a loop. Place it on the front of your polymer plate. Stick that side down in the position desired on your paper. Peel off the protective blue covering of the plate adhesive on the back of your plate. Close the lid of your L Letterpress. Open it up and now your plate is securely in the place you need. Remove the tape loop. Close the lid again to make sure you are happy with your placement.
How do I hold my paper in place when I use this machine?
Use our Henry Gage Pins to hold your paper. They have a little plastic lip to hold your paper in place. Lay your paper in the position desired. Slide two of the Henry Gage Pins up to the longest side of your paper and one on the shortest side. When they are tight against the paper sides, adhere to the machine base. The Gage pins are re-usable.
Another option is to take one spare piece of the paper you are printing on. Cut out the paper to form an “L”. Adhere this L shape on the machine base with Removable double-sided tape so the inside of the “L” is the outside boundary for two sides of your paper to be printed. Tape a small piece of plastic over the corner of the inside angle of the “L”. Slide your paper up against the L shape so one corner should go just under the small plastic holder to hold it in place while the sides of the paper are tight against the inside of the L shape.
How do I clean my machine, plates and brayer?
Use baby wipes, an old soft cotton t-shirt and odorless mineral spirits. The L Letterpress machine can be cleaned with baby wipes.
If you used any Van Son ink from a can, return any extra ink back to the can from the plastic ink square. Clean the two ink squares, both glass and plastic with baby wipes. Take one side of the cotton rag and wipe off the ink on your plates with a light stroke. Your ink is only on the surface of the plates so it should clean easily. If you have any ink residue left, take part of the cotton rag and get a small amount of the mineral spirits from the bottle. Wipe lightly on your plates and then turn the cloth over to a dry spot and wipe the plates again to remove any spirits. Do not use baby wipes or water on your plates.
Clean your brayer with baby wipes and then finish with a wipe of the rag with mineral spirits. You always want your brayer (roller) to be completely clean.
Do not use any water to clean your polymer plates, we can’t say this enough.
How can I achieve proper inking with this press?
When inking for letterpress, very little is always better. You only need a very light layer of ink on the top of your plates. We suggest the 2-step method of inking.
You will need these items:
- A new brayer (throw out the one that came with the machine and purchase a soft rubber brayer)
- The hard plastic sheet that comes with your machine – approx 6”.
- An ink knife
- Another piece of glass (or plastic) for part two of your inking – at least 8” wide and long.
Steps:
- Squeeze out an inch or two of ink from the tube. Or if you have a can of our Van Son ink, take your ink knife and scoop out a tablespoon of ink from the surface of the ink can. Place it on the 6” square and start to mix the ink to make it more fluid and smooth. Use a motion like scrambling eggs where you turn the ink over, pull the knife through and repeat. The ink should soften a little while you mix.
- Take the ink knife and pull a small ⅛” thick roll of ink from the mixture with your blade. Move this ink to the second piece of glass. Dab that ink across the glass until it’s about equal to the width of your brayer. Roll your brayer back and forth and side to side through the ink until it’s spread out evenly on the brayer. The ink may make a little noise like its snapping as you spread it out.
You will need very little ink for printing and this two step method means that you can control your ink coverage better. Using your roller bearers (polymer strips we ship you), lay the strips on both sides of your design plate. These support your brayer for smooth inking. Take your brayer and ink up your polymer plate – usually 1-2 rolls of the brayer. If your inking is fuzzy and on the sides of your impression, you have too much ink. Wipe off your brayer and roll it through the ink again.
With a little practice you will learn to control inking. To add more ink to your second inked glass, pull a small bit from the first mixing square – always 1/8″ thick roll or less.
What kind of ink should I use when printing with KF152 polymer plates?
The L Letterpress comes with an oil based ink. You can continue to use those offered by the manufacturer but they are limited in colors. Boxcar Press sells a wide assortment of oil based and rubber based ink. We like rubber based inks for letterpress as they dry quickly on cotton papers and similar papers used for letterpress. Do not use any paints or water based inks on your photopolymer plates as they will soften and deteriorate the plates.
Creating Vector Art with Live Trace
Creating vector art via the Live Trace function in Adobe Illustrator will convert a rasterized (e.g a pixel-based) graphic into a vectorized graphic (e.g artwork made up of vectors or small points). Using the Live Trace feature to convert your artwork ensures the crispest and cleanest plate possible, as well as allows scaling and transforming the artwork without losing data or composition clarity.
Depending on what type of artwork one is looking to convert to vector, a few considerations must be taken for best results. Pixel-based graphics, such as calligraphy and line art, should be converted to image mode of bitmap beforehand and have a higher resolution of 300-600. The more graphic, stark, and higher contrast an image is, the better the Live Trace result will be. Live Trace will not always work for all images but with practice, you’ll learn to recognize what images will work best with Live Trace.
First, open the file in Adobe Illustrator. Next, double-click on the image with the default (black) arrow tool until the Live Trace toolbar appears at the top of the Illustrator tool bar.
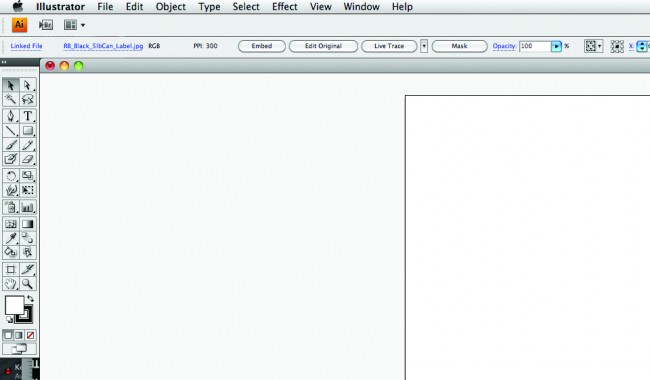
Live Trace Toolbar
Within the Live Trace toolbar in Adobe Illustrator, you have the ability to choose either between presets or experiment with different manual settings. The default is usually adequate for most purposes so click on Live Trace. The image will reshape and convert to 100% cmyk black. If you are satisfied with the conversion-to-vector on screen preview, then click “Expand” or “Live Paint” to immediately convert the file to vector. White and black anchor squares will appear on the Illustrator art board to denote the successful conversion. Click on your white artboard again to complete the trace.
Depending on the quality of the original pixel-based file and the desired effect in mind, Live Trace is a very powerful editing tool for scanned-in calligraphy and high-contrast line art.
Is there a checklist for me to review with my files before submitting to platemaking?
To ease file prep woes and to ensure a smooth production transition from file to plate, it is a great help to all to give your files one last review before submitting them. The first few things to make sure is that your file’s artwork is set to the right dimensions, that you’ve checked your artwork to make sure all plate type line minimums are met, that your file is in the proper color mode or image mode and that your file is in the proper file format and extension.
When working with a file that requires multiple colors for separations, please make sure all objects are assigned to their appropriate Pantone swatch or spot color. Adobe Illustrator and InDesign are excellent programs for setting up and checking such files.
Please also remember to check out any other file prep questions to answer any unresolved questions that you may have.
How do I know what plate type to choose?
This depends on the type of base you own. See the plate choices part of our web site for more information! In general, you will choose a plate with two things in mind, your base system (Boxcar or Magnetic) and your printing press. Our plastic backed plates correspond to a particular Boxcar Base and steel backed plates will correspond to either the Patmag or Bunting base.
If you are using one of the Do It Yourself home letterpress systems, we suggest the KF152 plastic backed plates.
If you are using an etching press, call us and we’ll suggest a plate, based upon a few questions about your setup.
As you are likely hand inking with these last two presses, please remember to ask us to SEND STRIPS in your platemaking order. They will be very helpful with your inking brayer for an easier inking.
How large can my file be while uploading?
The largest size, data-wise, that we accept is 26MB. If your file’s data size is larger than this, determine if it can be broken up into two or more files. If you actually have a large file in MB but not in inches, check to see if your images could be saved again in Photoshop with LZW compression and placed again into your document. This great compression feature will make your files more manageable.
For alternate electronic ways, we highly recommend compressing the file down with a program such as StuffIt or ZIP. There are also many numerous online free File Transfer Sites, such as YouSendIt.com or DropBox.com, that let you upload a file and send a link for Boxcar to download.
We will also always take your files on CD by mailing to: Platemaking Department; Boxcar Press; 509 W. Fayette St. #135; Syracuse, NY 13204.
Tell me more about the ink colors that you carry.
We offer all 14 base Pantone mixing inks. These inks, paired with the Pantone formula guide, will allow you to mix any of the guide’s hundreds of Pantone colors. The base inks are: Red (032); Pantone Black (mixing black); Blue (072); Green; Transparent White (mixing white); Orange (021); Process Blue; Purple; Reflex Blue; Rhodamine Red; Rubine Red; Violet; Warm Red; and Yellow. We also carry opaque white for printing white or printing on dark paper stock; universal printing black, the perfect black letterpress ink (available in oil-based or rubber-based only); and custom mixes that match any Pantone number. View a PDF of the Van Son color chart.
Once I’m done printing, how do I clean the letterpress ink off my rollers/plates?
To clean ink off your press, we recommend California Wash used with rags or disposable shop towels. This press wash cleans up acrylic, oil based and rubber based inks well, is a low VOC solvent, and has a mild somewhat citrus odor. For an occasional cleaning and deglazing of rollers, use Easy Street Additive after press wash.
Why shouldn’t I let oil-based letterpress ink dry on my rollers
Oil based inks will dry within a few hours if left unattended on press; dried oil-based inks can take a long time to clean and can even cause rollers to be permanently damaged.
How do I print with light toned letterpress inks on dark paper?
With letterpress, we most often print dark ink on light paper, because that is letterpress printing’s strength! Light ink on dark paper is really best suited for engraving. That said, if you really want light ink on dark paper, just be prepared for paper to show through. Think “chalkboard” for the end results. Letterpress uses transparent inks. Even with opaque white, printing light ink on dark paper will be like using a thin coat of white paint on a brown wall: you’ll see the brown color through the paint. If using a pure white ink, you can run a piece through the press twice to create a more dense color. Metallic inks will be more opaque and are the most popular choice for paper cover-up with dark papers.
How do I firm up my thin letterpress ink?
Add magnesium carbonate to your ink. Magnesium carbonate is available in our Supplies section from Boxcar Press. Inks are measured by their tackiness or stickiness and their body or how stiff it is. An ink’s body can be drippy like chocolate syrup topping or thicker like frosting or paste. The ink can also be described as being long or short. Long inks are tackier and when pulled up straight from the can will have a long tail. The white powder of magnesium carbonate will stiffen your ink and reduce tackiness.
What are the most essential basic letterpress ink colors for me to have in my shop?
Try our letterpress ink basic starter kit, which includes Printing Black; Warm Red; Reflex Blue; Yellow; Transparent White (mixing white); and Pantone Black (mixing black). With these 6 colors you can mix over 250 pantone colors. If you’re ready for more, you may want to try the remaining Pantone base colors.
What letterpress ink should I use: oil base, rubber base, or acrylic?
We recommend rubber-based inks for general letterpress printing—it’s the type of ink we use in our own print shop. Rubber-based inks dry by being absorbed into the paper. That makes them ideal for the cotton and bamboo blends of paper used in letterpress. Use the oil-based inks if you’d like a glossier ink that works well with coated papers . Oil based inks dry by oxidation or air drying. That is why they can form a skin on the top of the can after opening and why you won’t want to keep it on your press overnight. Try the acrylic if you’re looking for a glossier ink that can still stay open on the press. Acrylic inks will also harden in the can quicker than rubber-based inks so long term storage can be a factor.
It is best to mix only like inks from the same family—oil base with oil base, rubber base with rubber, and acrylic with acrylic.
Can I mix an oil-based letterpress ink with a rubber-based letterpress ink or an acrylic ink?
No, it’s not recommended to mix ink types. You can get unexpected results when you mix the different characteristics of oil-based, acrylic or rubber-based inks. The acidities, emulsifications, driers, and amounts of distillates can compete with each other and alter drying properties or tackiness.
Tell me how to put new adhesive on an old letterpress plate.
If you start to see gunk stuck in the adhesive (cat hair, human hair, your lunch crumbs, etc.), then it’s time to put new adhesive on your polymer plate. This should be a pretty easy process but does require a little muscle.
First, peel up the old adhesive to remove it. You’ll need some good fingernails to get between the adhesive and your plate. Since the adhesive holds onto the plate strongly, you can potentially kink the plastic backing if you’re not careful. We recommend that you lay the plate face down on a flat surface. Hold the plate down with one hand while peeling the adhesive off with the other. Try and keep the plate from flexing inordinately while you carefully tug the adhesive off the back of the plate. The adhesive might tear into pieces, but you can simply pull it up in strips.
Now, put on the new adhesive. If you have purchased a 12” x 18” sheet of adhesive, lay the blue release paper on a flat surface and have the brown silicone paper side face up. You will remove this silicone paper to show the sticky adhesive. If you have a roll of adhesive, pull out or unroll the adhesive so the sticky side is face up. When you first mount the adhesive to the plate, start with one side or corner of the plate and lay down the plate to the adhesive so that it makes as few air gaps or bubbles as possible. If the bubbles happen, work them out with your fingers or pierce them, through the back of the adhesive, with one prick of an Exacto knife or awl. You should be able to get all the bubbles out at this point.
If bubbles form underneath the plate when you mount it to the base, first try working these out to the edges of the plate with your fingers. If that fails, you can puncture the bubbles by sticking an Exacto knife through the BACK of the plastic backing of the plate (the blue side) to release the trapped air.
Can I lock up two different Boxcar Bases and use them together?
Yes, you can certainly lock up two Boxcar Bases into one chase and print, and in most situations print a letterpress plate that spans the two bases. We inspect our Boxcar Bases and verify they are within plus/minus 0.001” in thickness, parallel and flatness. Still, we’d like your bases to be even closer in height than +/- 0.001″ if possible. Here’s how to do this depending on your situation.
- You purchase one base and have it cut into two pieces: use each piece individually or lock them both back up together for a larger base surface. Your two cut sides should match up perfectly. Slide them together and using quoins, furniture and leading, fill the chase on all sides around the two bases to support the pieces and have a good strong lock-up.
- You already have two different bases in your shop: These should be fine to print. There may be slight variation within the +/- 0.001″ tolerance, so find the two sides most similar in thickness and slide them together.
- You have a base. You want to purchase another base to print with at the same time: We keep detailed specs on each base we sell. When you order your second base, let us know your original base’s serial number—we’ll make sure the bases we ship to you are identical heights so you can butt them together and have a very even printing surface. Where do you find your serial number – on the bottom edge under the Boxcar text.
- You are going to purchase two bases to print with at the same time: Just let us know that you’re planning to print with them at the same time, and we’ll choose the two closest in height from our inventory.
When do I replace my kreene in my platemaker? And how do I replace kreene?
Kreene, a flexible and matte transparent plastic, is used in a platemaker’s vacuum frame to hold films securely against photopolymer plates during exposure. But over time, it’s the nature of kreene to get wrinkled and lose flexibility. When you find that your kreene no longer creates a smooth seal, it’s time for a kreene replacement! At Boxcar Press, we replace our kreene every few days, but we process a lot of plates. With lower use, kreene can last for several months.
To replace your kreene: cut out a square of kreene to the size of the previous kreene piece (your kreene will be slightly larger than the grooves in the vacuum table). If your platemaker has one, pull the round bar out the previous sheet of kreene. Affix the new sheet of kreene to the bar with double-stick tape. Lay the kreene in position on the vacuum table and turn the vacuum on. Work out any wrinkles in the kreene so it remains flat. Using double-stick tape, affix the kreene edge opposite the bar to the vacuum table. You can then roll the kreene out over your vacuum table and start exposing your polymer plates. To increase the life of your Kreene, roll it out flat in your platemaker at the end of the day.
If I’m scanning an image, what resolution (DPI) should it be?
Most folks want clean line art, and if this is what you’re seeking, scan at least at 600 DPI, though 1200 DPI is even better. Open your scan in Photoshop to convert your file to the Image mode of Bitmap via the 50% threshold method and an output of 600 – 1200. If you lose too much detail, you can make adjustments to your image by using Image Adjustments > Levels or Image Adjustments > Brightnesss / Contrast.
If you’d like a halftone, you can use a 300 DPI scan. With halftones, keep the image in the grayscale color mode in Photoshop, and let us know the LPI / line screen.
Either way, save your image as a TIFF with LZW compression. This will make your file size more manageable when placing into another program like Illustrator or uploading to your job ticket.
Is there a preferred LPI (Lines Per Inch) for halftones?
The ideal LPI depends on your paper and presswork, but most printers printing on uncoated paper use a 100 LPI. It’s a good balance of fine screen and easy printing. The higher the line screen, the more difficult it will be to print, because the high line-screen plate plugs up with ink in the shadows and looks murky over-all. Some printers prefer playing it safe and order 85 or 65 LPI. Using a lower LPI does make the dots coarser and more obvious. The finest line screen that we usually process is 133 LPI, although we would even question the use of 133 LPI, except on coated or hard papers.
If you’d like a halftone for your image, don’t adjust or apply an LPI in your file. Just tell us what LPI you’d like us to use, and we’ll take care of the rest.
If you tell us the paper, the type of press you’re using, and what you hope to accomplish with your halftone, we would be happy to recommend a line screen for you!
What does LPI (Lines Per Inch) do? What do I need to know about LPI and my files?
The amount of dots in an inch of a halftone is determined by the LPI, also known as line screen. The higher the LPI, the more dots there are per inch. A higher LPI means the dots are smaller and less noticeable. Letterpress printers typically use between 85-133 LPI for their halftones. We find that 100 LPI is a good choice for all plate types and is the default we apply if you don’t specify.
What is a grayscale and a halftone?
The technical definition: a halftone is a matrix of different size dots which allow printers to simulate tonal variation when printing with a single ink on press. What this means: a halftone allows you, using one color ink, to approximate various shades of color. Take a magnifying glass and look at a black and white photo printed in your local newspaper. You’ll notice the image is actually made up of different size dots. The smaller the dot, the lighter the color in the halftone. A grayscale is made up of pixels that are in varying shades of black so the tones are represented by the different shades. Once a file has a line screen applied, the grayscale is now a halftone.
Should I gang up my images/smaller files into one larger file?
If you are ordering printing from us, no. Please send individual files and we will set up for most efficient production in our shop.
If you are ordering plates and doing your own printing, yes! By ganging up the plate yourself, you have more control over the margins and gaps between the ganged up artwork. Between each individual piece, we recommend .375” for plastic-backed plates and .5” for steel-backed plates. Our negatives come out of the imagesetter in 18″ strips, so ganging up onto a 17” wide strip, and up to max 22” long, is the most economical way to make negatives. Since we like to keep our maximum plate size at 17 x 22, please break larger files into two files.
That said, if you were to send us many individual files, we’d gang up the pieces in the most cost-effective manner. If you’re using plastic-backed plates, after we gang up your files, we’ll ship your job as a single plate and you can trim them easily yourself, using scissors or an Exacto.
If you’re using steel-backed plates and we gang up your files for you, we’ll ship your job as a single plate, unless you provide a cutting diagram for us. If you are submitting a ganged up file, keep in mind the fingers of our employees who have to trim your metal plates and leave us enough room around your text/images to hold the plate safely while we cut.
What programs do you support?
Our favorite ways to receive files for letterpress platemaking are by you sending us a press-ready PDF file (with fonts embedded) for platemaking. This PDF will serve as both your hard copy and your plate file. No additional faxing or email needed.
Our second favorite way is for you to send an EPS or AI file for platemaking. We also accept PDF digital files in current versions of other major design programs (i.e. Quark, InDesign, Freehand).
If you are creating your files in Photoshop, we like to say that this program is good for images but not so great for text. It’s best to convert your grayscale images in Photoshop and place them into Illustrator where you will add your text. If Photoshop is your only option, start with a file that is 600 dpi minimum so you can minimize the pixelation of your text when you convert files. More on file conversion to Image Mode of Bitmap under File Prep Tips. We prefer tif files from photoshop for upload.
Note, we can often make plates from PDFs created from Word files, however, Word is not able to format your file exactly the way we need. So please tell us your file was originally a Word document so we can anticipate and make corrections. If you are designing in Word, we suggest that you don’t use any funky or crazy fonts we won’t have access to. Oftentimes, they will just print as strange characters. Your images placed in Word will usually require some corrections too. You can email your files to plates@boxcarpress.com for an evaluation first and we’ll advise on how letterpress friendly it is.
Can you scan my camera-ready artwork?
Yes! Simply mail us your camera-ready art and we will scan it in for you. When possible, we love art work that’s on smooth, bright white paper or drafting vellum. Textured paper makes our job more difficult as the scan will pick up any background patterns, paper shadings, paper texture, etc. We are faithful to originals: if you require modification or retouching, you may be charged for additional file preparation time at our shop rate of $60/hour. We’ll contact you before we bill for additional file prep. We can scan, in house, artwork up to 12 x 17 inches.
What’s the largest size plate you can make?
For the 94FL, KF95, KF152, and 152SB plates, the largest size plate we can process is 17.5” x 22.5” (where your image area is 17” x 22”). For all other plates, the largest size plate is 16” x 22” (image area is 15.5” x 22”)
What’s the thinnest line and smallest dot you can hold on a plate?
It depends on the plate (though no hair lines, please!). If your plate has a 94 or 95 in the product name, we recommend at least a 0.25 point thickness (or larger). If your plate has 145 or 152 in the product name, we recommend at least a .35 point/.007″ thickness (or larger). Watch out for typefaces with swirly curves that thin or have breaks or fonts with fine cross bars.
For dots, we recommend at least a 1 pt diameter if your plate has a 94 or 95 in the product name. Boost that to 1.25pt diameter for plates that are 145 or 152 in thickness. Each of those dots has to stand on it’s own on the plate and that thickness will provide the support at the base of the plate to hold the dot. Watch out for typefaces where the dots on the “I’s or periods are small, as seen in many sans serif fonts that are decorative, free form or look hand drawn.
Undersize lines and dots may appear on your plate as wavy or be missing completely so checking this is very important for a good file and usable plate.
Mark as helpful. 204
What’s the smallest type size you can hold in your platemaking?
This question is not as straightforward as it seems. We can hold a 3 pt. Times New Roman type face on 94 and 95 plate material but the real question is the next one about the thinnest line and dots the plates can hold. The font choice and characteristics of the font may limit the point size.
What’s the biggest problem that printers new to photopolymer encounter?
Photopolymer plates offer an way to letterpress print extremely detailed designs with a deep heavy impression (or a kiss impression if you’re so inclined). The chief problem that new photopolymer users encounter usually deals with roller height/roller condition. But no worries! Unlike larger problems like war or global warming, roller issues do have concrete and relatively easy solutions. We recommend rubber rollers and, if using a platen press, solid trucks. If switching from lead type/magnesium plates, you’ll want to keep a much closer eye on your rollers. You may find our general printing FAQ’s useful, especially if you’ll be using a Boxcar Base.
When will I receive my order?
Photopolymer supply orders ship from our warehouse within 1-2 business days.
Custom Platemaking orders ship depending on the service you choose:
We offer a 1 business day turnaround, or Same Day Rush – an extra fee service.
For shipping in the USA, we offer UPS Ground, UPS 3 day air Service, UPS 2 day air Service, UPS Overnight morning, UPS afternoon Saver and UPS early Am (before coffee) 8:30 am service.
For International Customers, we offer US Postal Priority or Express Mail and UPS Worldwide Saver.
Remember that the days refer to business days and not weekends.
Can I mount your plates on wood?
We don’t recommend it. If you are determined to use wood, however—know that, even after your lengthy set-up time that will be required of you, you’ll still see uneven printing if using a wood base. Wood simply isn’t a flat enough surface to print on.
How should I store my polymer plates?
To preserve your plates, the manufacturers recommend storing polymer plates in a constant humidity between 50% and 60%. At the very least, avoid extreme fluctuations in humidity. If stored properly (and cleaned correctly), your letterpress plates can last for one year or more.
- For your exposed plates, maintain a constant humidity by storing plates in a ziplock bag. Keep your plates away from ultraviolet light that will crack the surface of your plate (i.e. store in a drawer or cabinet).
- For your unexposed plates, store in a black light-blocking bag that is taped shut.
Most of my plate is printing fine, but one or two areas of the plate are printing heavy. What do I do?
More often than not, this is a result of roller problems. It could be the height of your rollers or your rollers can have an uneven or flat spot on the surface (read more about roller gauges). If you processed your plates yourself, there’s the chance your plate wasn’t processed correctly and you have “fat” text, which can cause some areas to look heavier.
Why do I have ink on my Boxcar Base?
It’s important to keep the grid on your Boxcar Base clean so you can see its registration marks when printing. If your rollers ever lay ink down directly on the base’s surface, STOP! STOP! STOOOOOOOOOOOOOP! Don’t keep running the press because something is out of alignment. Then ask yourself:
- Are your rollers at type-high? Using a roller gauge, check to make sure your rollers are set for type-high printing material. The surface of the base is far below type high and should never come into contact with the rollers.
- Is your base flat in the press bed? Take a piece of onionskin paper and try to slide it between the base and the press bed – if the onionskin paper fits, one of the corners of your base is working up in the press. Frequently this is caused by tightening the quoins too much. Since the Boxcar Base won’t work up as easily as handset metal type or monotype, you don’t need to tighten the quoins quite as hard.
Still getting ink on your base? If, after checking the roller height and loosening the quoins, you still have problems with ink on your base – contact us and we’ll assist you in problem-solving further.
How do I use a Stouffer Gauge to help process my plates?
Instructions for using the Stouffer Gauge to accurately figure out the exposure time for your photopolymer plates: The Stouffer gauge is a reusable piece of continuous-tone film that you should use to test photopolymer plate exposures. Place the Stouffer Gauge in contact with a 1” x 6” strip of plate material (after you peel off the plate’s protective plastic cover). Then expose the plate.
You’ll have to guess the first exposure time because that varies depending on the equipment that you use. Start with the exposure time listed on your plate’s tech data sheet. For exposure times, please keep in mind that these times are for commercial photopolymer platemaking equipment. Any alternative photopolymer platemaking devices may have very different times and you’ll have to experiment more to find your ideal time.
Also check the plate’s tech data sheet for the Stouffer value you’re trying to hold during exposure. For example, the 94FL has a Stouffer value of 18. Make sure that the exposure used with the Stouffer Gauge hardens the plate for all the numbers up to and including #18. If you goal is #18, and #19 and #20 start to harden during your exposure time, then your exposure time is too long– decrease the exposure time. If your goal is #18, and #17 hardens but #18 washes out on the test plate, then increase the exposure time.
You most likely will have to expose several different test plates at several different exposure times to find the perfect exposure. Since the Stouffer gauge is small, you won’t waste much plate material in the process.
How often must I change the adhesive on my polymer plates?
As long as you’re careful about not getting dust or debris on the adhesive, and you carefully replace the blue protective release paper after use, the adhesive on your letterpress plates should remain sticky for many years. Keep in mind that adhesive can always be inexpensively replaced.
If I purchase unexposed photopolymer, do I need to purchase adhesive too?
It depends on the plate. If you’re purchasing unexposed plastic-backed plates, you’ll need adhesive to adhere the plate to your printing base. We sell adhesive in 12×18 sheets and 27 yard rolls. Apply to the back of the plate after processing. If you’re purchasing unexposed steel-backed plates, there’s no need to purchase adhesive. Adhesive is included if we process the plastic-backed plates for you.
How do I cancel an order?
For supplies, please call us as soon as possible to cancel your order. We will have to discuss refunds and crediting accounts as your online Supply Order has already been charged for payment.
For Platemaking – you can call us right away or you may be able to cancel your order online, if your status is still in RECEIVED or ON HOLD.
Log on to platemaking and you’ll see all current orders. Choose Complete Order to cancel your order. Confirm when it asks if you want to proceed. Your order status will reflect Order Cancelled.
The option to cancel is not available once we move your ticket into platemaking production. Cancelling after this step may incur some production costs. Please call us right away to minimize those costs, if possible.
Once my order is placed online, how do I make a change to it?
Supply orders: please call us or e-mail us as soon as possible.
Platemaking: First, log-in to see your order and check its current status. If we haven’t begun processing your order (STATUS – RECEIVED), you’ll be able to change your order details or upload files online. If we’ve already begun working on your order (STATUS – IN PLATEMAKING), please call us or e-mail us immediately, as you won’t be able to adjust your order online and we can see if the production process is already too far along. At this point, we can still change your shipping options and shipping addresses. If your status is BILLING COMPLETE, we will not be able to make any adjustments at this time.
Do you ship internationally?
Supplies: We ship supplies to Canada via UPS Standard or UPS Worldwide Saver and US Postal Service.
We ship international orders (outside of Canada) via UPS Worldwide Saver and US Postal Express Mail.
We think our online ordering system is pretty nifty but of course you can phone in your order to us by calling 315-473-0930. We love to talk to our customers.
Platemaking: We ship platemaking orders to Canada via UPS Standard or UPS Worldwide Saver and US Postal Service. We can ship Worldwide Saver to any international location or opt to use the US Postal Express Mail. These options are all at the click of a button through out platemaking site.
Printing: Yes, we love working with international clients and sending off printed letterpress beauties to destinations far and near.
I need my order shipped today. By what time do I need to place the order?
For supply orders: Orders typically ship within 1-2 business days. If you need your order immediately, we encourage you to request expedited overnight shipping. However, if you’re in a serious letterpress emergency, please place your order before noon EST and mention that you’d like same day shipping. We’ll do our best to make it happen!
For platemaking: place your same day rushes by 1 p.m. EST.
How do I know when my order has been shipped?
For platemaking, the day your order is completed (Order Complete) is the day your order ships. You will get a UPS tracking number via the log-in email on your account. Your invoice will be shipped in a separate email. Review your Order History to see all past and current orders for your status. For international orders using the US Postal Service, you will receive an email with your tracking number.
For Supplies – an email will be sent with the tracking number.
What do I need to be able to letterpress print with your photopolymer plates?
You’ll need:
- a printing base. The polymer plates we create aren’t type high by themselves. They need to be mounted on a base to make a type-high printing surface. We recommend our Boxcar Base system. Letterpress printers also use magnetic bases from Patmag or Bunting. If you are printing on a DIY press such as L Letterpress, please refer to this tutorial.
- a Printing press. Remember that most letterpress printing presses people purchase will not be ready to print beautifully right away and a little tender loving care will be needed. Be prepared to purchase new rollers or do other maintenance on your press!
- Ink. we recommend Van Son rubber-based letterpress inks, which you can order in any uncoated Pantone number! Or you can purchase the Van Son base colors and mix your own colors. View the inks we carry.
- various pressroom supplies, including printers furniture, quoins, tympan paper, type gauge, ink knife and (if using a platen press) Kort gauge pins or Henry gage pins.
- a fashionable printing apron
We now sell letterpress starter packs, which contain a lot of what you’ll need to get started.
I’m a metal clay artist. What photopolymer plates do I use?
We carry plates that are very similar to those recommended by Art Jewelry Magazine. Many metal clay artists have used our plates to great success. We have several plate types that will suit your needs and preferences.
Art Jewelry Suggests | Boxcar Press plate | Boxcar plate thickness | Plate material | Impression |
---|---|---|---|---|
0.8mm | 94FL | .94mm/.037” | plastic backed | shallower |
1.52mm | KF152 | 1.50mm/.060 | plastic backed | deep |
0.9mm or greater | 94SB | .94mm/.037” | metal backed | shallower |
0.9mm or greater | 145HSB | 1.40mm/.057″ | metal backed | medium |
1.52mm | 152SB | 1.50mm/.060″ | metal backed | deep |
Boxcar Press offers two options to metal clay artists. We can sell you unexposed polymer plates for do-it-yourself artists to create their own negatives and process themselves. Check out our new Plates by the Pound service for our plastic backed plates under our Supplies. Or we can take your digital files or images and professionally create plates for you, quickly and economically.
In either case, you will want to store your exposed plates in a zipper bag out of sunlight. You may also want to consider using a silicon spray to protect the plate from the moisture in the clay. You will want to clean the plate with vegetable oil. Exposure to too much light and moisture will cause your plates to deteriorate.
Remember, we’re a letterpress shop, and letterpress is our expertise. We can’t answer specific questions about how our plates work with your process, but we can offer information on the polymer plate material, thickness, exposure times, and processing.
For additional information, you may also want to check out:
- Metal Clay yahoo group: join this vibrant community of over 3,000 artists.
- Maggie Berman’s site features a great instructional article on using polymer plates for metal clay, PMC, or precious metal clay artists.
How do I process my photopolymer plates?
Because processing your own plates can get complicated – and the results need to be excellent for quality letterpress printing – we recommend using a dedicated photopolymer platemaker. If you don’t already own one of these machines, we can help you source out light boxes, washout and exposure units, whatever your budget. If you’d rather learn how to hand-process your plates, we recommend checking out Letterpress Commons and, if you can, taking a class at one of these great book arts centers: Center for Book Arts (NYC); Minnesota Center for Book Arts; San Francisco Center for Book Arts; Columbia College Center for Book and Paper Arts (Chicago). You’ll find essential exposure information in your plate’s datasheets, though you’ll want to use a Stouffer Gauge to perfect exposure. We can always process your plates professionally for you through our platemaking services.
Is processing a photopolymer plate toxic?
None of the byproducts of processing photopolymer plates are known to have health risks, except if you’re allergic by contact to plastic. Check out the MSDS’s for more specific health information. You can find each plate’s MSDS on it’s product page: plastic-backed plates; steel-backed plates; intaglio plates.
I want to use photopolymer to do something other than letterpress printing. How do I know what plate to use?
While our troubleshooting only extends to using photopolymer plates for letterpress printing, there are literally dozens of other uses for photopolymer plates. If you know the tech specs of the plate that you need, or if you can send us a sample of the plate required for your application, we would be happy to try and recommend a plate that we have in stock that will work for you.
We have innovative people using our plates for metal clay jewelry making, translucent porcelain, and leather work. We always like to hear what you want to try.
What are roller gauges and why do I need them?
Roller gauges are especially indispensable with a platen press. Letterpress rollers need to be positioned just right in order to deposit a thin film of ink onto the surface of the form, without squeezing ink over the edges. A roller gauge will help you accurately measure the height of your rollers so you can produce the crispest printing that your press is capable of. We sell roller gauges, precision ground to type high, which are also very fashionable.
When your rollers are positioned correctly, your printing will look beautifully crisp. But if your rollers aren’t positioned at the right height, your printing will have a halo effect: dark around the edges and/or chunkier/blotchier than it should be. If you ever notice ink on the back of your polymer plate or on your base — it’s a roller gauge emergency! Adjust your rollers now! We have a great video on setting roller gauge height in our Boxcar Training Videos and step by steps are listed here.
Step 1. While your press is inked up, remove the chase (on platen presses) or the base (on a Vandercook).
Step 2. We recommend checking the roller height in the four corners of the press bed. We’ll start in the upper right hand corner. Engage the form rollers and position them over the upper right corner of the bed.
Step 3. You will be pulling a stripe of ink on the round surface of the roller gauge. Pull the gauge underneath the form rollers so that a stripe of ink is transferred to the rounded surface of the gauge’s cylinder. Measure the stripe of the ink: you want your ink stripe to measure 3/32”. If the strip of ink is less than 1/16”, you’ll have difficulty consistently inking your plate (some areas will appear too light, and some areas will appear too dark). If your strip of ink is wider than 3/32”, your rollers put too much pressure on your plate and cause your printing to be chunky/blurry.
Step 4: On a platen press, to adjust the height of your form rollers: add tape to the rails that the roller trucks ride on. You may have to add several layers of tape. Strapping tape or plumber’s silver tape is frequently used for this. If you’re using a press other than a platen press, consult your manual as to how to raise your form rollers.
Step 5: Repeat steps three and four in each corner of your press bed.
Step 6: When your rollers are positioned correctly, you should pull identical 3/32” stripes of ink from the four corners of the press bed, and your printing should be both crisp and beautiful!
If you continue to notice inconsistencies in your inking after adjusting your roller height correctly, you may need to purchase new rollers and, if using a platen press, roller trucks as well.
What will I need to do to my platen press before printing with polymer and a Boxcar Base (especially if my printing is blobby and/or has a “halo”)? i.e. how do I add tape to my rails?
Every platen or lever press has wear on the rails and needs tape on the rails to raise the rollers to the right height. This is whether you use lead type or polymer—although the problem surfaces more frequently on polymer if the roller rails aren’t set correctly. You have to build up the rails that the roller trucks travel on so that the rollers just graze the surface of the form. The best way to do this is to add equal layers of masking or strapping tape to each rail. Keep building up the rails in this fashion until whatever you’re printing doesn’t ink up at all (i.e. bring the rollers up just past the point where the rollers ink the plate). Then take off one layer of tape so that the rollers drop down with minimum contact to the plate. This will keep ink from getting on the backing of the plate and the base, and it will also help make your printing crisper. It’s not uncommon to have to add as much as a 1/16″—or sometimes 1/8″—in tape in order to get the rails to the right height. These presses are often 100 years old and have 100 years of wear that you have to overcome. We do not recommend that you adjust your trucks or printing plate/base for this problem. Better printing results from type-high rollers. After you add tape to your rails, we recommend using a roller gauge to perfect the height of your rollers.
If I have a 10 x 15 chase on my press, why can’t I use a 10 x 15 base?
We totally understand that you want to get the most use and space out of your press. However, knowing about some of the challenges you will face can help you make decisions about the correct size.
First, keep in mind that every press, like every person, has a limit to its strength. A press with a 10 x 15 chase will never be able to hammer a 10 x 15 block of text. You’ll be able to get a good impression using about 60-70% of your chase, depending on your form. Secondly, your base needs to stay put in your chase with a good lockup. To secure your base in your chase, you need to make room for the quoins plus furniture for distributing the weight of the base, and gauge pins. Gauge pins fit in the space outside the base and over the furniture.
We recommend checking out our Base Selection Chart which recommends the ideal size base for your chase. With a 10×15 chase, we would recommend a 9×12 base, for instance.
If you really want to max out the base size, keep in mind your base should be at least 1 inch, preferably 1.5 inches, smaller than your chase. If you use a lot of paper that is precut, it is most likely smaller than your base. This can make it challenging to place your gauge pins and still hold the paper and not hit the base. One safety note, the larger the base in your platen press, the further you have to reach into the press to place your paper. This is very important with a larger press with a motor, so take into consideration your comfortable reach, the speed of the press, and your fingers when locking up a larger base.
I own both a Vandercook and a platen press – do you suggest that I buy two separate bases, the Deep Relief Base for the platen press, and the Standard Grid base for the Vandercook?
We suggest purchasing one type of base for both presses, so that your presses will be able to share the same plate. It really comes down to your experience: if you’re a new printer, go with the Deep Relief base. Setting roller height can be a longer adjustment process on platen presses and this base will be more forgiving as you work through this. If you can use a roller gauge in your sleep, and you have experience expertly adjusting your inking rollers on your C&P, go with the Standard Base. The Standard Base’s plates are less expensive per square inch as they are slightly thinner but all plates, when paired with the correct base, equal type high (.918) and that is the most critical factor.
How do I drain and refill my platemaker?
Drain the platemaker often, usually after every 10 to 12 processed plates. To drain, open the drain valve. The washout water is safe to go down the drain. To refill, close the drain and fill with water. Leave the tank full of water so the brushes don’t dry out. If you’re leaving the machine unused for an extended period of time, add half a cup of bleach to the water to resist algae. When you use the machine again, drain and refill the tank with fresh water.
How do I maintain the mounting rubber on my platemaker?
Magnetic mounting rubber and rigid mounting rubber come pre-sealed. Over time, this seal breaks down. You can make touch-up repairs with our green die sealer. Remove any old die sealer and apply green die sealer in a thin bead to the edge of the mounting rubber. Let dry overnight.
When do I replace my platemaker’s brushes?
A platemaker’s brushes wear out after prolonged use: these brushes should be replaced every 6-36 months. You can tell when a brush is tired out because the bristles are matted down. You can lengthen your brush life by keeping the brushes wet all the time and running your fingers through them to encourage the bristles to stand up. We sell replacement brushes for all of our platemakers: please e-mail or call us to order these.
Designing for Foil Stamping
Can you mix foil and letterpress in a job?
Yes you can – and what a wonderful combination!
What sorts of designs are appropriate for foil?
Overall, most designs that are appropriate for letterpress will translate well to foil stamping. Each customer file that is submitted is reviewed by our prepress team, who are experienced in the foil die making process. Any design that contains areas of intricate detail, thin line fonts, or reverses will be addressed by our prepress personnel and we’ll contact you with any concerns that need addressing.
Are foil pieces recyclable?
Yes, you can place your foil pieces in your recycling bins along with your other paper products. And by the way, there are no solvents, inks, or vapors associated with foil stamping.
Do foil stamped pieces have any additional handling or mailing concerns?
We have conducted mailing tests on foil stamped invitation sets and postcards with terrific results. There are no additional handling or mailing concerns for foil stamped pieces.
Why can’t you rush my foil job?
Each foil stamped piece requires us to create a custom die that will be used in the foil stamping process. This die-making process is more time intensive than making plates for letterpress and doesn’t allow for a rush turnaround.
Capabilities
Do you print for stationery/invitation designers who need a letterpress printer and will resell the cards/invitations?
Yes, it’s a specialty of ours! Please contact us at printing@boxcarpress.com and we will be happy to introduce you to Boxcar Press and provide you with information, samples and pricing. We can also be reached by phone at 315-473-0930.
What is the lead time?
Normal production time is 10 working days, with day 1 being the day after we receive your signed contract. We will email you a contract the day or day after we receive your order and you can return that to us via email or fax.
Do you offer rush service?
Yes, we offer three levels of rush service:
Yellow service – we ship 7 business days after PDF proof approval, add 15% to cost of order
Orange service – we ship 5 business days after PDF proof approval, add 35% to cost of order
Red service – we ship 3 business days after PDF proof approval, add 60% to the cost of the order This service is subject to availability so please call us with your specific needs and we will see if rush service is available for your order.
Designing for Letterpress
What’s the smallest type size you can hold in your platemaking?
This question is not as straightforward as it seems. We can hold a 3 pt. Times New Roman type face on 94 and 95 plate material but the real question is the next one about the thinnest line and dots the plates can hold. The font choice and characteristics of the font may limit the point size.
What’s the thinnest line and smallest dot you can hold on a plate?
It depends on the plate (though no hair lines, please!). If your plate has a 94 or 95 in the product name, we recommend at least a 0.25 point thickness (or larger). If your plate has 145 or 152 in the product name, we recommend at least a .35 point/.007″ thickness (or larger). Watch out for typefaces with swirly curves that thin or have breaks or fonts with fine cross bars.
For dots, we recommend at least a 1 pt diameter if your plate has a 94 or 95 in the product name. Boost that to 1.25pt diameter for plates that are 145 or 152 in thickness. Each of those dots has to stand on it’s own on the plate and that thickness will provide the support at the base of the plate to hold the dot. Watch out for typefaces where the dots on the “I’s or periods are small, as seen in many sans serif fonts that are decorative, free form or look hand drawn.
Undersize lines and dots may appear on your plate as wavy or be missing completely so checking this is very important for a good file and usable plate.
Mark as helpful. 204
Can you scan my camera-ready artwork?
Yes! Simply mail us your camera-ready art and we will scan it in for you. When possible, we love art work that’s on smooth, bright white paper or drafting vellum. Textured paper makes our job more difficult as the scan will pick up any background patterns, paper shadings, paper texture, etc. We are faithful to originals: if you require modification or retouching, you may be charged for additional file preparation time at our shop rate of $60/hour. We’ll contact you before we bill for additional file prep. We can scan, in house, artwork up to 12 x 17 inches.
If I’m scanning an image, what resolution (DPI) should it be?
Most folks want clean line art, and if this is what you’re seeking, scan at least at 600 DPI, though 1200 DPI is even better. Open your scan in Photoshop to convert your file to the Image mode of Bitmap via the 50% threshold method and an output of 600 – 1200. If you lose too much detail, you can make adjustments to your image by using Image Adjustments > Levels or Image Adjustments > Brightnesss / Contrast.
If you’d like a halftone, you can use a 300 DPI scan. With halftones, keep the image in the grayscale color mode in Photoshop, and let us know the LPI / line screen.
Either way, save your image as a TIFF with LZW compression. This will make your file size more manageable when placing into another program like Illustrator or uploading to your job ticket.
Don’t use a jpeg or save as a bmp file for your images!
Our favorite image mode is a .tiff. Or send us vector art images (made in Illustrator or Freehand) instead of raster images (made in Photoshop). Jpeg files will create low-quality letterpress plates that will make you unhappy; its file format is best intended for the web. Files that end in .bmp can also give unwanted results by saving as the wrong size and are also lower quality.
In Illustrator, the only black your submitted file should use is 100% CMYK black (CM and Y are 0%)
When opening any new document in Illustrator, choose File > Document Color mode > CMYK. To Check this before submitting your file for upload – in illustrator versions CS4 and CS5, you can open your Output-Separations Preview window. Click on the drop down window showing Off and select Separations. Click off the black eye and everything left showing on your file is not in 100%K. If you select a part of your file that is left, and look at your color palette, anything that shows a percentage of C,M, or Y needs to be corrected. To correct this – go to Select > Same > Fill (or Stroke). It should highlight everything that looks like black (but isn’t). Than go to the color palette and using the eyedropper, click on the black part of the bar (far right). The C, M, and Y will go to 0% and the K should go to 100%. Now this part of the file should disappear because it is correctly set to 100%K.
When using Illustrator, how do I outline my fonts and why is it important?
Sending all your fonts packaged is not fail-safe: all needed fonts aren’t always provided, or all your fonts may not be recognized when we open your file, causing shifting and changes in your design. On the other hand, outlining fonts is fool-proof, safe, and ideal. So outline your fonts! In Illustrator, you do this by selecting TYPE>Create Outlines. This will automatically convert your text into vector shapes. Your type will temporarily look bolder and be highlighted in blue. Click on any white area of your file and it will look normal again.
Do I send my files to size or scaled down?
You will need to send your files at 100% scale. We do not resize, scale up or down, or rotate any artwork. We highly recommend using the ruler feature available in Adobe Illustrator, Photoshop and InDesign to check your work to see if it is the size you want.
When exporting a PDF from Adobe Illustrator or Adobe InDesign, please double check to make sure it is the correct size by either re-opening it in Illustrator or placing it in InDesign to check the actual dimensions of your file. In InDesign you can use the Rectangle Frame tool to draw a box around your images/text to measure.
In Photoshop, use the Image Size tool to check your size. Saving your file as a .TIF locks your image size.
Do I send my files reversed for your processing?
No. Please send your artwork and text right-reading as you want it to appear as the final print. We will make a film negative here at Boxcar Press for you. However, if you are planning to use your files in a different process than printing, please call us to discuss how best to prep your files.
How do I submit artwork for print jobs or quote requests?
Send an email to printing@boxcarpress.com. If the file is too large try using yousendit.com. (Boxcar Press can accept up to 25MB via email but your email capacity may not allow a file that large to be sent.) Before you send, make sure you have outlined your type, included actual crop marks or a cut rule and that your files are set in solid, uncoated Pantone colors.
What file formats do you accept?
We prefer press quality PDF files and also accept Adobe Illustrator files and EPS files. (If sending an eps file please also send a pdf for reference.)
How do I outline fonts?
While either in Adobe Illustrator or InDesign, select all your text that needs to be outlined using the black arrow tool (the default arrow tool). Next, select TYPE>Create Outlines. This will automatically convert your text into vector shapes. Your text will temporarily look bolder and be highlighted in blue. Click anywhere on your artboard that is white to deselect your text and its appearance will look normal again.
How do I select spot colors in my file instead of CMYK?
Spot color or Pantone swatch colors can be applied to objects via the Pantone Swatch Color Book or Spot color library found in Adobe Illustrator. For Adobe InDesign, Spot Colors are more easily accessed. First, activate the Swatch palette by selecting WINDOW>Swatches.
Notice the fly-down menu icon in the upper right-hand corner of the Color palette? The icon looks like a small downward black triangle with four small lines next to it. Clicking on this will open a fly-out window menu. Hover your mouse over “Open Swatch Library” to open another fly-out window menu of all the color books. Very carefully move your mouse to hover over “Color Books”, which will open up another fly-out menu. You’ll see a lot of different color book options, but we recommend using “PANTONE solid uncoated”. Clicking on this color book will open a new window filled to the brim with a plethora of color
Swatches that Pantone has to offer.
Finally, assign all your file’s artwork, objects, and text to their appropriate Pantone Swatches or spot colors.
In Indesign, open the swatch window. click on the downward black triangle to the right and choose New Color. This opens a New Color Swatch Window. Select Spot as color type and Pantone Solid Uncoated as the Color Mode. The PMS colors will load for you to select and click OK.
Boxcar Base
I own both a Vandercook and a platen press – do you suggest that I buy two separate bases, the Deep Relief Base for the platen press, and the Standard Grid base for the Vandercook?
We suggest purchasing one type of base for both presses, so that your presses will be able to share the same plate. It really comes down to your experience: if you’re a new printer, go with the Deep Relief base. Setting roller height can be a longer adjustment process on platen presses and this base will be more forgiving as you work through this. If you can use a roller gauge in your sleep, and you have experience expertly adjusting your inking rollers on your C&P, go with the Standard Base. The Standard Base’s plates are less expensive per square inch as they are slightly thinner but all plates, when paired with the correct base, equal type high (.918) and that is the most critical factor.
If I have a 10 x 15 chase on my press, why can’t I use a 10 x 15 base?
We totally understand that you want to get the most use and space out of your press. However, knowing about some of the challenges you will face can help you make decisions about the correct size.
First, keep in mind that every press, like every person, has a limit to its strength. A press with a 10 x 15 chase will never be able to hammer a 10 x 15 block of text. You’ll be able to get a good impression using about 60-70% of your chase, depending on your form. Secondly, your base needs to stay put in your chase with a good lockup. To secure your base in your chase, you need to make room for the quoins plus furniture for distributing the weight of the base, and gauge pins. Gauge pins fit in the space outside the base and over the furniture.
We recommend checking out our Base Selection Chart which recommends the ideal size base for your chase. With a 10×15 chase, we would recommend a 9×12 base, for instance.
If you really want to max out the base size, keep in mind your base should be at least 1 inch, preferably 1.5 inches, smaller than your chase. If you use a lot of paper that is precut, it is most likely smaller than your base. This can make it challenging to place your gauge pins and still hold the paper and not hit the base. One safety note, the larger the base in your platen press, the further you have to reach into the press to place your paper. This is very important with a larger press with a motor, so take into consideration your comfortable reach, the speed of the press, and your fingers when locking up a larger base.
What’s the smallest size plate that I can print on my Boxcar Base?
The Boxcar Base is guaranteed to hold plates in register, provided they are standard thickness plastic-backed plates mounted with our film adhesive. But plates that are smaller than .25 square inches may drift under certain conditions due to their small area of contact with the base. Make sure your plates are larger than .5″ by .5″, even if your image is very small.
How are plastic-backed and steel-backed plates different?
When mounted on their appropriate bases, plastic-backed and steel-backed photopolymer plates both create type-high surfaces for letterpress printing. Both plate types are recyclable. We’ll talk about some of their differences below.
Plastic-backed polymer plates are flexible, transparent, easy to cut, and mount onto a Boxcar Base for simple registration. You’ll find these plates:
- can be cut with scissors in both their unexposed and exposed forms.
- are transparent, meaning you can see the Boxcar Base’s grid through your plate. This allows for simple alignment of your plates to your base: For perfect registration, align a certain element of your plate to the grid: take a horizontal or vertical element in your plate (this could be your registration marks, or a horizontal line in your artwork) and line it up to the grid.
- eliminate plate creep (steel-backed plate users sometimes experience this while on press). The plastic-backed plate’s adhesive is shift resistant, giving you a secure, strong hold during printing (but the adhesive also peels up easily when you’re done printing)
- allow printers to print two color jobs using one plate if the design elements don’t touch. Cut out the second color images/text with a craft knife or scissors and set aside. Print color #1. Set your second color images back in place and pull up the first plate for color #1—perfect registration!
- allow designs to be ganged up on plates closely to save space (and money).
- are reusable. You will be able to reuse the plate many times if you keep the adhesive protected with the blue overlay after printing. You can also replace adhesive for even more extended plate use.
- more prone to curling, especially with large solid areas over time.
- If purchasing unexposed plastic-backed polymer plates, you’ll also want to purchase film adhesive to adhere your plates to your base. If we’re making your plates for you, we include adhesive.
- are suitable for metal clay jewelry.
- Over here at Boxcar, we use plastic-backed plates for all our printing (the Jet 94 Clear plate paired with the Standard Boxcar Base).
Steel-backed polymer plates are compatible with magnetic bases, generally the Patmag or Bunting base. Steel-backed polymer plates:
- require cutting with a metal shear or heavy-duty trimmer. You can use tin snips, though you may end up with kinks in your plate, as tin snips won’t cut as cleanly.
- sometimes shift and creep on your base during printing. Magnets in the base effectively hold a plate from peeling but cannot always hold a plate from moving side to side. The cylinder or rollers of a press can move steel-backed plates out of register (that’s “plate creep”).
- are not transparent. Because magnetic bases aren’t gridded (and you can’t see through these plates), you’ll have to align your plates to your base with a line gauge and possibly registration marks. This works, but it is more time consuming and there’s more room for error.
- are rigid, meaning they don’t bend well. This inflexibility can cause plates to kink and warp when handled so that their corners may work up while on press. Steel-backed plates are, however, very durable and not prone to curling over time.
- can be more expensive than plastic-backed plates because you may require registration or crop marks which makes for a larger plate.
- are difficult to get on and off the base, especially when the base has inlaid magnets. When placing metal plates on a magnetic base, keep fingers clear so they don’t get pinched when the magnet grabs. When taking your plate off the base, try an ink knife to pry under the plates to release from the magnetic base.
- have sharp edges, which dictate extra care when handling.
- can be used for a wide range of printing and impression—on leather, metal clay jewelry, ultra heavy-weight paper stocks. Steel-backed plates can also be used on etching presses when relief printing is desired. They are not suitable for high temperatures of foil stamping though.
What happens if you use a Deep Relief Boxcar Base on a Vandercook, Heidelberg Cylinder, or Heidelberg Windmill–some info you need to know?
The Deep Relief Boxcar Base does work fine on cylinder presses or the Windmill — since its base + plates + adhesive still equals a type high surface (.918”) and that is the critical issue for all bases and plates. There is the advantage of holding a slightly finer line with a standard plate but let’s be realistic when we compare. The 94/95 plates will hold a 0.25pt line and the 152 plates will hold a 0.35pt line (when talking inches that is a .0035″ line compared to a .0048″ line. Not much to quibble about. We just like the way a 94 plate works on our windmills with our standard base and that is how we started years ago in the infancy of Boxcar Press. That said, some printers who use the Deep Relief base on their platen presses already may want to use the Deep Relief base on, say, their Vandercook too, so that both presses can share plates — this is totally okay too.
What’s the maximum size polymer plate I can print on my base?
Your maximum plate size is actually the size of your base — your photopolymer plates can go right up to the edge of your base. Obviously your relief images and text should not hang over your edge. This is true for both magnetic bases and the Boxcar Base. If you need a little more base for occasional projects, consider a Boxcar Base scrap to add that extra ½” – 1”. Read more about maximum base size.
Rubber Base Inks category
What letterpress ink should I use: oil base, rubber base, or acrylic?
We recommend rubber-based inks for general letterpress printing—it’s the type of ink we use in our own print shop. Rubber-based inks dry by being absorbed into the paper. That makes them ideal for the cotton and bamboo blends of paper used in letterpress. Use the oil-based inks if you’d like a glossier ink that works well with coated papers . Oil based inks dry by oxidation or air drying. That is why they can form a skin on the top of the can after opening and why you won’t want to keep it on your press overnight. Try the acrylic if you’re looking for a glossier ink that can still stay open on the press. Acrylic inks will also harden in the can quicker than rubber-based inks so long term storage can be a factor.
It is best to mix only like inks from the same family—oil base with oil base, rubber base with rubber, and acrylic with acrylic.
What are the most essential basic letterpress ink colors for me to have in my shop?
Try our letterpress ink basic starter kit, which includes Printing Black; Warm Red; Reflex Blue; Yellow; Transparent White (mixing white); and Pantone Black (mixing black). With these 6 colors you can mix over 250 pantone colors. If you’re ready for more, you may want to try the remaining Pantone base colors.
How do I firm up my thin letterpress ink?
Add magnesium carbonate to your ink. Magnesium carbonate is available in our Supplies section from Boxcar Press. Inks are measured by their tackiness or stickiness and their body or how stiff it is. An ink’s body can be drippy like chocolate syrup topping or thicker like frosting or paste. The ink can also be described as being long or short. Long inks are tackier and when pulled up straight from the can will have a long tail. The white powder of magnesium carbonate will stiffen your ink and reduce tackiness.
How do I print with light toned letterpress inks on dark paper?
With letterpress, we most often print dark ink on light paper, because that is letterpress printing’s strength! Light ink on dark paper is really best suited for engraving. That said, if you really want light ink on dark paper, just be prepared for paper to show through. Think “chalkboard” for the end results. Letterpress uses transparent inks. Even with opaque white, printing light ink on dark paper will be like using a thin coat of white paint on a brown wall: you’ll see the brown color through the paint. If using a pure white ink, you can run a piece through the press twice to create a more dense color. Metallic inks will be more opaque and are the most popular choice for paper cover-up with dark papers.
Why shouldn’t I let oil-based letterpress ink dry on my rollers
Oil based inks will dry within a few hours if left unattended on press; dried oil-based inks can take a long time to clean and can even cause rollers to be permanently damaged.
Once I’m done printing, how do I clean the letterpress ink off my rollers/plates?
To clean ink off your press, we recommend California Wash used with rags or disposable shop towels. This press wash cleans up acrylic, oil based and rubber based inks well, is a low VOC solvent, and has a mild somewhat citrus odor. For an occasional cleaning and deglazing of rollers, use Easy Street Additive after press wash.
Tell me more about the ink colors that you carry.
We offer all 14 base Pantone mixing inks. These inks, paired with the Pantone formula guide, will allow you to mix any of the guide’s hundreds of Pantone colors. The base inks are: Red (032); Pantone Black (mixing black); Blue (072); Green; Transparent White (mixing white); Orange (021); Process Blue; Purple; Reflex Blue; Rhodamine Red; Rubine Red; Violet; Warm Red; and Yellow. We also carry opaque white for printing white or printing on dark paper stock; universal printing black, the perfect black letterpress ink (available in oil-based or rubber-based only); and custom mixes that match any Pantone number. View a PDF of the Van Son color chart.
When do you recommend I order a custom ink instead of mixing the ink myself?
Custom inks are a good alternative if you don’t have all the the Pantone Basic Colors but you still want to put a specific Pantone color on your press. Some printers prefer ordering custom mix inks for every job they print, though this can get expensive (and, since custom ink mixes come in 1 lb cans, you’ll have a lot leftover).
We recommend going with custom ink particularly in these two situations:
- you’re going to be printing the same color ink over an extended period of time—for example, we ordered custom ink mixes of all the ink colors in our Smock and Bella Figura ink libraries so we can offer consistent color for all customer jobs. This way, if you order a custom ink of say 476U, you’ll know when you need to reorder it a year later it will look exactly the same.
- you’re printing with very light colors or a pastel ink. The formulas for such inks require very precise measurements (.2% yellow plus 99.5% trans white, etc.) and it’s difficult to mix these colors accurately yourself.
Which is a more environmental ink: soy ink, oil-based ink, or rubber-based ink?
We get asked a lot about soy ink from our customers, since there’s this general feeling that soy ink is THE greenest ink out there. That’s not really true. Soy sheet-fed ink has to be just 20% soy to be labeled a soy ink (the exact % of soy varies depending on the specific ink). Rubber-based and oil-based inks both have 20-30% vegetable-oil (soy and linseed). Linseed oil is the traditional letterpress ink vehicle: it’s what Gutenberg used when he first used ink. Also keep in mind that soy inks are really geared toward high speed printing and loaded with lots of driers—they’re usually very thin, liquidy inks, not ideal for letterpress. In our experience, soy inks don’t transfer well to letterpress printing, and you’ll get the same environmental impact from using oil-based or rubber-based inks.
CML Oil Base Inks Category
What letterpress ink should I use: oil base, rubber base, or acrylic?
We recommend rubber-based inks for general letterpress printing—it’s the type of ink we use in our own print shop. Rubber-based inks dry by being absorbed into the paper. That makes them ideal for the cotton and bamboo blends of paper used in letterpress. Use the oil-based inks if you’d like a glossier ink that works well with coated papers . Oil based inks dry by oxidation or air drying. That is why they can form a skin on the top of the can after opening and why you won’t want to keep it on your press overnight. Try the acrylic if you’re looking for a glossier ink that can still stay open on the press. Acrylic inks will also harden in the can quicker than rubber-based inks so long term storage can be a factor.
It is best to mix only like inks from the same family—oil base with oil base, rubber base with rubber, and acrylic with acrylic.
What are the most essential basic letterpress ink colors for me to have in my shop?
Try our letterpress ink basic starter kit, which includes Printing Black; Warm Red; Reflex Blue; Yellow; Transparent White (mixing white); and Pantone Black (mixing black). With these 6 colors you can mix over 250 pantone colors. If you’re ready for more, you may want to try the remaining Pantone base colors.
How do I firm up my thin letterpress ink?
Add magnesium carbonate to your ink. Magnesium carbonate is available in our Supplies section from Boxcar Press. Inks are measured by their tackiness or stickiness and their body or how stiff it is. An ink’s body can be drippy like chocolate syrup topping or thicker like frosting or paste. The ink can also be described as being long or short. Long inks are tackier and when pulled up straight from the can will have a long tail. The white powder of magnesium carbonate will stiffen your ink and reduce tackiness.
How do I print with light toned letterpress inks on dark paper?
With letterpress, we most often print dark ink on light paper, because that is letterpress printing’s strength! Light ink on dark paper is really best suited for engraving. That said, if you really want light ink on dark paper, just be prepared for paper to show through. Think “chalkboard” for the end results. Letterpress uses transparent inks. Even with opaque white, printing light ink on dark paper will be like using a thin coat of white paint on a brown wall: you’ll see the brown color through the paint. If using a pure white ink, you can run a piece through the press twice to create a more dense color. Metallic inks will be more opaque and are the most popular choice for paper cover-up with dark papers.
Why shouldn’t I let oil-based letterpress ink dry on my rollers
Oil based inks will dry within a few hours if left unattended on press; dried oil-based inks can take a long time to clean and can even cause rollers to be permanently damaged.
Once I’m done printing, how do I clean the letterpress ink off my rollers/plates?
To clean ink off your press, we recommend California Wash used with rags or disposable shop towels. This press wash cleans up acrylic, oil based and rubber based inks well, is a low VOC solvent, and has a mild somewhat citrus odor. For an occasional cleaning and deglazing of rollers, use Easy Street Additive after press wash.
Tell me more about the ink colors that you carry.
We offer all 14 base Pantone mixing inks. These inks, paired with the Pantone formula guide, will allow you to mix any of the guide’s hundreds of Pantone colors. The base inks are: Red (032); Pantone Black (mixing black); Blue (072); Green; Transparent White (mixing white); Orange (021); Process Blue; Purple; Reflex Blue; Rhodamine Red; Rubine Red; Violet; Warm Red; and Yellow. We also carry opaque white for printing white or printing on dark paper stock; universal printing black, the perfect black letterpress ink (available in oil-based or rubber-based only); and custom mixes that match any Pantone number. View a PDF of the Van Son color chart.
When do you recommend I order a custom ink instead of mixing the ink myself?
Custom inks are a good alternative if you don’t have all the the Pantone Basic Colors but you still want to put a specific Pantone color on your press. Some printers prefer ordering custom mix inks for every job they print, though this can get expensive (and, since custom ink mixes come in 1 lb cans, you’ll have a lot leftover).
We recommend going with custom ink particularly in these two situations:
- you’re going to be printing the same color ink over an extended period of time—for example, we ordered custom ink mixes of all the ink colors in our Smock and Bella Figura ink libraries so we can offer consistent color for all customer jobs. This way, if you order a custom ink of say 476U, you’ll know when you need to reorder it a year later it will look exactly the same.
- you’re printing with very light colors or a pastel ink. The formulas for such inks require very precise measurements (.2% yellow plus 99.5% trans white, etc.) and it’s difficult to mix these colors accurately yourself.
Which is a more environmental ink: soy ink, oil-based ink, or rubber-based ink?
We get asked a lot about soy ink from our customers, since there’s this general feeling that soy ink is THE greenest ink out there. That’s not really true. Soy sheet-fed ink has to be just 20% soy to be labeled a soy ink (the exact % of soy varies depending on the specific ink). Rubber-based and oil-based inks both have 20-30% vegetable-oil (soy and linseed). Linseed oil is the traditional letterpress ink vehicle: it’s what Gutenberg used when he first used ink. Also keep in mind that soy inks are really geared toward high speed printing and loaded with lots of driers—they’re usually very thin, liquidy inks, not ideal for letterpress. In our experience, soy inks don’t transfer well to letterpress printing, and you’ll get the same environmental impact from using oil-based or rubber-based inks.
Platemaking Supplies Category
Tell me how to put new adhesive on an old letterpress plate.
If you start to see gunk stuck in the adhesive (cat hair, human hair, your lunch crumbs, etc.), then it’s time to put new adhesive on your polymer plate. This should be a pretty easy process but does require a little muscle.
First, peel up the old adhesive to remove it. You’ll need some good fingernails to get between the adhesive and your plate. Since the adhesive holds onto the plate strongly, you can potentially kink the plastic backing if you’re not careful. We recommend that you lay the plate face down on a flat surface. Hold the plate down with one hand while peeling the adhesive off with the other. Try and keep the plate from flexing inordinately while you carefully tug the adhesive off the back of the plate. The adhesive might tear into pieces, but you can simply pull it up in strips.
Now, put on the new adhesive. If you have purchased a 12” x 18” sheet of adhesive, lay the blue release paper on a flat surface and have the brown silicone paper side face up. You will remove this silicone paper to show the sticky adhesive. If you have a roll of adhesive, pull out or unroll the adhesive so the sticky side is face up. When you first mount the adhesive to the plate, start with one side or corner of the plate and lay down the plate to the adhesive so that it makes as few air gaps or bubbles as possible. If the bubbles happen, work them out with your fingers or pierce them, through the back of the adhesive, with one prick of an Exacto knife or awl. You should be able to get all the bubbles out at this point.
If bubbles form underneath the plate when you mount it to the base, first try working these out to the edges of the plate with your fingers. If that fails, you can puncture the bubbles by sticking an Exacto knife through the BACK of the plastic backing of the plate (the blue side) to release the trapped air.
When do I replace my kreene in my platemaker? And how do I replace kreene?
Kreene, a flexible and matte transparent plastic, is used in a platemaker’s vacuum frame to hold films securely against photopolymer plates during exposure. But over time, it’s the nature of kreene to get wrinkled and lose flexibility. When you find that your kreene no longer creates a smooth seal, it’s time for a kreene replacement! At Boxcar Press, we replace our kreene every few days, but we process a lot of plates. With lower use, kreene can last for several months.
To replace your kreene: cut out a square of kreene to the size of the previous kreene piece (your kreene will be slightly larger than the grooves in the vacuum table). If your platemaker has one, pull the round bar out the previous sheet of kreene. Affix the new sheet of kreene to the bar with double-stick tape. Lay the kreene in position on the vacuum table and turn the vacuum on. Work out any wrinkles in the kreene so it remains flat. Using double-stick tape, affix the kreene edge opposite the bar to the vacuum table. You can then roll the kreene out over your vacuum table and start exposing your polymer plates. To increase the life of your Kreene, roll it out flat in your platemaker at the end of the day.
When do I replace my platemaker’s brushes?
A platemaker’s brushes wear out after prolonged use: these brushes should be replaced every 6-36 months. You can tell when a brush is tired out because the bristles are matted down. You can lengthen your brush life by keeping the brushes wet all the time and running your fingers through them to encourage the bristles to stand up. We sell replacement brushes for all of our platemakers: please e-mail or call us to order these.
How do I maintain the mounting rubber on my platemaker?
Magnetic mounting rubber and rigid mounting rubber come pre-sealed. Over time, this seal breaks down. You can make touch-up repairs with our green die sealer. Remove any old die sealer and apply green die sealer in a thin bead to the edge of the mounting rubber. Let dry overnight.
Is processing a photopolymer plate toxic?
None of the byproducts of processing photopolymer plates are known to have health risks, except if you’re allergic by contact to plastic. Check out the MSDS’s for more specific health information. You can find each plate’s MSDS on it’s product page: plastic-backed plates; steel-backed plates; intaglio plates.
How do I process my photopolymer plates?
Because processing your own plates can get complicated – and the results need to be excellent for quality letterpress printing – we recommend using a dedicated photopolymer platemaker. If you don’t already own one of these machines, we can help you source out light boxes, washout and exposure units, whatever your budget. If you’d rather learn how to hand-process your plates, we recommend checking out Letterpress Commons and, if you can, taking a class at one of these great book arts centers: Center for Book Arts (NYC); Minnesota Center for Book Arts; San Francisco Center for Book Arts; Columbia College Center for Book and Paper Arts (Chicago). You’ll find essential exposure information in your plate’s datasheets, though you’ll want to use a Stouffer Gauge to perfect exposure. We can always process your plates professionally for you through our platemaking services.
If I purchase unexposed photopolymer, do I need to purchase adhesive too?
It depends on the plate. If you’re purchasing unexposed plastic-backed plates, you’ll need adhesive to adhere the plate to your printing base. We sell adhesive in 12×18 sheets and 27 yard rolls. Apply to the back of the plate after processing. If you’re purchasing unexposed steel-backed plates, there’s no need to purchase adhesive. Adhesive is included if we process the plastic-backed plates for you.
How often must I change the adhesive on my polymer plates?
As long as you’re careful about not getting dust or debris on the adhesive, and you carefully replace the blue protective release paper after use, the adhesive on your letterpress plates should remain sticky for many years. Keep in mind that adhesive can always be inexpensively replaced.
How do I use a Stouffer Gauge to help process my plates?
Instructions for using the Stouffer Gauge to accurately figure out the exposure time for your photopolymer plates: The Stouffer gauge is a reusable piece of continuous-tone film that you should use to test photopolymer plate exposures. Place the Stouffer Gauge in contact with a 1” x 6” strip of plate material (after you peel off the plate’s protective plastic cover). Then expose the plate.
You’ll have to guess the first exposure time because that varies depending on the equipment that you use. Start with the exposure time listed on your plate’s tech data sheet. For exposure times, please keep in mind that these times are for commercial photopolymer platemaking equipment. Any alternative photopolymer platemaking devices may have very different times and you’ll have to experiment more to find your ideal time.
Also check the plate’s tech data sheet for the Stouffer value you’re trying to hold during exposure. For example, the 94FL has a Stouffer value of 18. Make sure that the exposure used with the Stouffer Gauge hardens the plate for all the numbers up to and including #18. If you goal is #18, and #19 and #20 start to harden during your exposure time, then your exposure time is too long– decrease the exposure time. If your goal is #18, and #17 hardens but #18 washes out on the test plate, then increase the exposure time.
You most likely will have to expose several different test plates at several different exposure times to find the perfect exposure. Since the Stouffer gauge is small, you won’t waste much plate material in the process.
How should I store my polymer plates?
To preserve your plates, the manufacturers recommend storing polymer plates in a constant humidity between 50% and 60%. At the very least, avoid extreme fluctuations in humidity. If stored properly (and cleaned correctly), your letterpress plates can last for one year or more.
- For your exposed plates, maintain a constant humidity by storing plates in a ziplock bag. Keep your plates away from ultraviolet light that will crack the surface of your plate (i.e. store in a drawer or cabinet).
- For your unexposed plates, store in a black light-blocking bag that is taped shut.
My letterpress plates are starting to curl. How do I flatten them out?
Like our skin, plates can be affected by the room temperature, humidity, and age. When humidity levels are low, the plates can look and feel brittle. With the passage of time, the thinner polymer on the plate edges are pulled towards the denser polymer text and images on the front—this causes curling. With a life expectancy of up to 1 year or more, polymer plates do age, but these simple steps can hydrate your plates and give them extra longevity.
Step 1. Place your plate back in your platemaking washout system for up to ½ a minute (or, if you don’t have a washout unit, simply immerse in water). We suggest room temperature for a quick dunking. A ½ minute may only be necessary if your plates are severely curled.
Step 2. Sponge off the water and place back in the drying oven of the platemaker for 5-10 minutes. If you don’t have a platemaker, use a hair dryer to warm the plate and make it more pliable. Placing your plate in a box and blowing the hair dryer into the box will keep the warm air more contained and warm the plates more effectively.
Step 3. After the plate warms and starts to become more pliable, place the plate in its bag and set a heavy object on it to keep the flattened shape.
This should help your plates relax so you can adhere them to your base for additional print runs.
Here’s some final advice:
- if using a hair dryer, take care to avoid putting it too close to the plates.
- be patient, as warming the plates takes time.
- watch that you don’t handle your letterpress plates too roughly after the wash and during drying so your relief images don’t chip.
- remember to store your plates flat out of direct light and in a bag so that fluctuations in humidity don’t affect the polymer.
- check your adhesive backing, to see if the adhesive needs to be re-applied to the back of your polymer plate for a secure hold on your base.
L Letterpress Supplies Category
What kind of ink should I use when printing with KF152 polymer plates?
The L Letterpress comes with an oil based ink. You can continue to use those offered by the manufacturer but they are limited in colors. Boxcar Press sells a wide assortment of oil based and rubber based ink. We like rubber based inks for letterpress as they dry quickly on cotton papers and similar papers used for letterpress. Do not use any paints or water based inks on your photopolymer plates as they will soften and deteriorate the plates.
How can I achieve proper inking with this press?
When inking for letterpress, very little is always better. You only need a very light layer of ink on the top of your plates. We suggest the 2-step method of inking.
You will need these items:
- A new brayer (throw out the one that came with the machine and purchase a soft rubber brayer)
- The hard plastic sheet that comes with your machine – approx 6”.
- An ink knife
- Another piece of glass (or plastic) for part two of your inking – at least 8” wide and long.
Steps:
- Squeeze out an inch or two of ink from the tube. Or if you have a can of our Van Son ink, take your ink knife and scoop out a tablespoon of ink from the surface of the ink can. Place it on the 6” square and start to mix the ink to make it more fluid and smooth. Use a motion like scrambling eggs where you turn the ink over, pull the knife through and repeat. The ink should soften a little while you mix.
- Take the ink knife and pull a small ⅛” thick roll of ink from the mixture with your blade. Move this ink to the second piece of glass. Dab that ink across the glass until it’s about equal to the width of your brayer. Roll your brayer back and forth and side to side through the ink until it’s spread out evenly on the brayer. The ink may make a little noise like its snapping as you spread it out.
You will need very little ink for printing and this two step method means that you can control your ink coverage better. Using your roller bearers (polymer strips we ship you), lay the strips on both sides of your design plate. These support your brayer for smooth inking. Take your brayer and ink up your polymer plate – usually 1-2 rolls of the brayer. If your inking is fuzzy and on the sides of your impression, you have too much ink. Wipe off your brayer and roll it through the ink again.
With a little practice you will learn to control inking. To add more ink to your second inked glass, pull a small bit from the first mixing square – always 1/8″ thick roll or less.
How do I clean my machine, plates and brayer?
Use baby wipes, an old soft cotton t-shirt and odorless mineral spirits. The L Letterpress machine can be cleaned with baby wipes.
If you used any Van Son ink from a can, return any extra ink back to the can from the plastic ink square. Clean the two ink squares, both glass and plastic with baby wipes. Take one side of the cotton rag and wipe off the ink on your plates with a light stroke. Your ink is only on the surface of the plates so it should clean easily. If you have any ink residue left, take part of the cotton rag and get a small amount of the mineral spirits from the bottle. Wipe lightly on your plates and then turn the cloth over to a dry spot and wipe the plates again to remove any spirits. Do not use baby wipes or water on your plates.
Clean your brayer with baby wipes and then finish with a wipe of the rag with mineral spirits. You always want your brayer (roller) to be completely clean.
Do not use any water to clean your polymer plates, we can’t say this enough.
How do I hold my paper in place when I use this machine?
Use our Henry Gage Pins to hold your paper. They have a little plastic lip to hold your paper in place. Lay your paper in the position desired. Slide two of the Henry Gage Pins up to the longest side of your paper and one on the shortest side. When they are tight against the paper sides, adhere to the machine base. The Gage pins are re-usable.
Another option is to take one spare piece of the paper you are printing on. Cut out the paper to form an “L”. Adhere this L shape on the machine base with Removable double-sided tape so the inside of the “L” is the outside boundary for two sides of your paper to be printed. Tape a small piece of plastic over the corner of the inside angle of the “L”. Slide your paper up against the L shape so one corner should go just under the small plastic holder to hold it in place while the sides of the paper are tight against the inside of the L shape.
How do I properly place my photopolymer plate so it is aligned to print correctly in the right position on my paper?
Here is a printer tip we use on our presses. Set up your paper where you want it on your machine bed. Take a piece of scotch tape and make a loop. Place it on the front of your polymer plate. Stick that side down in the position desired on your paper. Peel off the protective blue covering of the plate adhesive on the back of your plate. Close the lid of your L Letterpress. Open it up and now your plate is securely in the place you need. Remove the tape loop. Close the lid again to make sure you are happy with your placement.
How do I design for printing on paper that is 100# and 200# weight?
We encourage you to read all our file prep tips for platemaking. A good design for letterpress will have crisp clean line art and fonts. If you are printing for 100# (or 110#) paper, you can gang up a lot of images together leaving ½” between them to cut with scissors. When you are ready to print, you can cut and paste and arrange your layout on the L Letterpress. When you print on this weight of paper, the edges of the plates will not leave marks on the paper.
However, when you are printing on the thicker weight 200# (or 220#) paper, you will need to set up your files a little differently. With this thicker paper, cut and pasting doesn’t work because the edges of the plates will also impress into the paper. Not the look you want. So you must design your whole plate completely so that everything is in its exact placement and the plate must be a fraction larger than your finished size of your paper. So if your paper is 5” x 7”, your finished plate must be 5 ⅛” x 7 ⅛”. The easiest way to do this is put registration marks at those dimensions so we can send a plate at the correct size. Cut off these marks when your plate arrives to a size so that the plate edges will be just outside your paper edge.
How do I learn to print with good results on the L Letterpress?
The L Letterpress does take a little learning and practice. Follow all of our instructions and read our blog on getting the best results from this machine.
The best piece of advice is to use scrap paper and a test plate while you are learning. Do not use the expensive paper you bought to print your wedding invites or baby announcements on. Use a similar weight card stock or less expensive papers to try everything out first. Remember there are always two sides to the paper so turn it over and try again. Here at Boxcar Press, we have makeready and set-up paper we use many times as we get everything just right. When you feel comfortable and ready to go ahead, switch to your real plates and paper and you’ll have a much better handle on the results. Don’t learn on paper and plates you are emotionally invested in while you are learning your way around letterpress. Remember you can have fun and be proud of something you made yourself for your special occasion.
My letterpress plates are starting to curl. How do I flatten them out?
Like our skin, plates can be affected by the room temperature, humidity, and age. When humidity levels are low, the plates can look and feel brittle. With the passage of time, the thinner polymer on the plate edges are pulled towards the denser polymer text and images on the front—this causes curling. With a life expectancy of up to 1 year or more, polymer plates do age, but these simple steps can hydrate your plates and give them extra longevity.
Step 1. Place your plate back in your platemaking washout system for up to ½ a minute (or, if you don’t have a washout unit, simply immerse in water). We suggest room temperature for a quick dunking. A ½ minute may only be necessary if your plates are severely curled.
Step 2. Sponge off the water and place back in the drying oven of the platemaker for 5-10 minutes. If you don’t have a platemaker, use a hair dryer to warm the plate and make it more pliable. Placing your plate in a box and blowing the hair dryer into the box will keep the warm air more contained and warm the plates more effectively.
Step 3. After the plate warms and starts to become more pliable, place the plate in its bag and set a heavy object on it to keep the flattened shape.
This should help your plates relax so you can adhere them to your base for additional print runs.
Here’s some final advice:
- if using a hair dryer, take care to avoid putting it too close to the plates.
- be patient, as warming the plates takes time.
- watch that you don’t handle your letterpress plates too roughly after the wash and during drying so your relief images don’t chip.
- remember to store your plates flat out of direct light and in a bag so that fluctuations in humidity don’t affect the polymer.
- check your adhesive backing, to see if the adhesive needs to be re-applied to the back of your polymer plate for a secure hold on your base.
Home made presses and Instructable Presses – I’ve built a homemade press and would like to know the best advice for printing with it.
We applaud innovators and inventors, where would printing be without it? We offer two of the most common homemade press designs from the internet.
Links to homemade press info
Book Press Design
Hydraulic Jack Press
To print with a home-constructed press, here are the items suggested for printing:
- we offer our Boxcar Press platemaking services. Our KF152 photopolymer plate with the adhesive backing works beautifully for homemade presses.
- Inking with a homemade press requires a soft rubber brayer (6” minimum suggested) that can be purchased from your arts store or McClain Printmaking.
- Plate strips to serve as roller bearers for your brayer when inking. Just ask us to send you a few plate strips when placing your order.
- Boxcar Press Ink Knife.
- Henry Gage Pins for paper registration.
- Printing Inks – for best results -Rubber based or oil based from Boxcar Press.
- Old cotton tshirts for clean up rags.
- Extra 1 or 2 sheets of glass or smooth acrylic for inking.
Before you start printing, we encourage you to read our blog posting which has some instructional tips on inking on home machines.
Homemade presses are better suited for light impression printing. Suggested papers and where to buy are:
- Cotton and bamboo papers from Legion Paper’s letterpresspapers.com
- Crane’s Lettra from Neenah Papers
Enjoy your experience letterpress printing on your homemade press. Your results will be something you can be proud of.
Pressroom Supplies Category
What do I need to be able to letterpress print with your photopolymer plates?
You’ll need:
- a printing base. The polymer plates we create aren’t type high by themselves. They need to be mounted on a base to make a type-high printing surface. We recommend our Boxcar Base system. Letterpress printers also use magnetic bases from Patmag or Bunting. If you are printing on a DIY press such as L Letterpress, please refer to this tutorial.
- a Printing press. Remember that most letterpress printing presses people purchase will not be ready to print beautifully right away and a little tender loving care will be needed. Be prepared to purchase new rollers or do other maintenance on your press!
- Ink. we recommend Van Son rubber-based letterpress inks, which you can order in any uncoated Pantone number! Or you can purchase the Van Son base colors and mix your own colors. View the inks we carry.
- various pressroom supplies, including printers furniture, quoins, tympan paper, type gauge, ink knife and (if using a platen press) Kort gauge pins or Henry gage pins.
- a fashionable printing apron
We now sell letterpress starter packs, which contain a lot of what you’ll need to get started.
What’s the biggest problem that printers new to photopolymer encounter?
Photopolymer plates offer an way to letterpress print extremely detailed designs with a deep heavy impression (or a kiss impression if you’re so inclined). The chief problem that new photopolymer users encounter usually deals with roller height/roller condition. But no worries! Unlike larger problems like war or global warming, roller issues do have concrete and relatively easy solutions. We recommend rubber rollers and, if using a platen press, solid trucks. If switching from lead type/magnesium plates, you’ll want to keep a much closer eye on your rollers. You may find our general printing FAQ’s useful, especially if you’ll be using a Boxcar Base.
How do I drain and refill my platemaker?
Drain the platemaker often, usually after every 10 to 12 processed plates. To drain, open the drain valve. The washout water is safe to go down the drain. To refill, close the drain and fill with water. Leave the tank full of water so the brushes don’t dry out. If you’re leaving the machine unused for an extended period of time, add half a cup of bleach to the water to resist algae. When you use the machine again, drain and refill the tank with fresh water.
Letterpress Ink Starter Pack Category
What are the most essential basic letterpress ink colors for me to have in my shop?
Try our letterpress ink basic starter kit, which includes Printing Black; Warm Red; Reflex Blue; Yellow; Transparent White (mixing white); and Pantone Black (mixing black). With these 6 colors you can mix over 250 pantone colors. If you’re ready for more, you may want to try the remaining Pantone base colors.
How do I firm up my thin letterpress ink?
Add magnesium carbonate to your ink. Magnesium carbonate is available in our Supplies section from Boxcar Press. Inks are measured by their tackiness or stickiness and their body or how stiff it is. An ink’s body can be drippy like chocolate syrup topping or thicker like frosting or paste. The ink can also be described as being long or short. Long inks are tackier and when pulled up straight from the can will have a long tail. The white powder of magnesium carbonate will stiffen your ink and reduce tackiness.
How do I print with light toned letterpress inks on dark paper?
With letterpress, we most often print dark ink on light paper, because that is letterpress printing’s strength! Light ink on dark paper is really best suited for engraving. That said, if you really want light ink on dark paper, just be prepared for paper to show through. Think “chalkboard” for the end results. Letterpress uses transparent inks. Even with opaque white, printing light ink on dark paper will be like using a thin coat of white paint on a brown wall: you’ll see the brown color through the paint. If using a pure white ink, you can run a piece through the press twice to create a more dense color. Metallic inks will be more opaque and are the most popular choice for paper cover-up with dark papers.
Why shouldn’t I let oil-based letterpress ink dry on my rollers
Oil based inks will dry within a few hours if left unattended on press; dried oil-based inks can take a long time to clean and can even cause rollers to be permanently damaged.
Once I’m done printing, how do I clean the letterpress ink off my rollers/plates?
To clean ink off your press, we recommend California Wash used with rags or disposable shop towels. This press wash cleans up acrylic, oil based and rubber based inks well, is a low VOC solvent, and has a mild somewhat citrus odor. For an occasional cleaning and deglazing of rollers, use Easy Street Additive after press wash.
Tell me more about the ink colors that you carry.
We offer all 14 base Pantone mixing inks. These inks, paired with the Pantone formula guide, will allow you to mix any of the guide’s hundreds of Pantone colors. The base inks are: Red (032); Pantone Black (mixing black); Blue (072); Green; Transparent White (mixing white); Orange (021); Process Blue; Purple; Reflex Blue; Rhodamine Red; Rubine Red; Violet; Warm Red; and Yellow. We also carry opaque white for printing white or printing on dark paper stock; universal printing black, the perfect black letterpress ink (available in oil-based or rubber-based only); and custom mixes that match any Pantone number. View a PDF of the Van Son color chart.
Boxcar Base manual
What’s the biggest problem that printers new to photopolymer encounter?
Photopolymer plates offer an way to letterpress print extremely detailed designs with a deep heavy impression (or a kiss impression if you’re so inclined). The chief problem that new photopolymer users encounter usually deals with roller height/roller condition. But no worries! Unlike larger problems like war or global warming, roller issues do have concrete and relatively easy solutions. We recommend rubber rollers and, if using a platen press, solid trucks. If switching from lead type/magnesium plates, you’ll want to keep a much closer eye on your rollers. You may find our general printing FAQ’s useful, especially if you’ll be using a Boxcar Base.
What will I need to do to my platen press before printing with polymer and a Boxcar Base (especially if my printing is blobby and/or has a “halo”)? i.e. how do I add tape to my rails?
Every platen or lever press has wear on the rails and needs tape on the rails to raise the rollers to the right height. This is whether you use lead type or polymer—although the problem surfaces more frequently on polymer if the roller rails aren’t set correctly. You have to build up the rails that the roller trucks travel on so that the rollers just graze the surface of the form. The best way to do this is to add equal layers of masking or strapping tape to each rail. Keep building up the rails in this fashion until whatever you’re printing doesn’t ink up at all (i.e. bring the rollers up just past the point where the rollers ink the plate). Then take off one layer of tape so that the rollers drop down with minimum contact to the plate. This will keep ink from getting on the backing of the plate and the base, and it will also help make your printing crisper. It’s not uncommon to have to add as much as a 1/16″—or sometimes 1/8″—in tape in order to get the rails to the right height. These presses are often 100 years old and have 100 years of wear that you have to overcome. We do not recommend that you adjust your trucks or printing plate/base for this problem. Better printing results from type-high rollers. After you add tape to your rails, we recommend using a roller gauge to perfect the height of your rollers.
Why do I have ink on my Boxcar Base?
It’s important to keep the grid on your Boxcar Base clean so you can see its registration marks when printing. If your rollers ever lay ink down directly on the base’s surface, STOP! STOP! STOOOOOOOOOOOOOP! Don’t keep running the press because something is out of alignment. Then ask yourself:
- Are your rollers at type-high? Using a roller gauge, check to make sure your rollers are set for type-high printing material. The surface of the base is far below type high and should never come into contact with the rollers.
- Is your base flat in the press bed? Take a piece of onionskin paper and try to slide it between the base and the press bed – if the onionskin paper fits, one of the corners of your base is working up in the press. Frequently this is caused by tightening the quoins too much. Since the Boxcar Base won’t work up as easily as handset metal type or monotype, you don’t need to tighten the quoins quite as hard.
Still getting ink on your base? If, after checking the roller height and loosening the quoins, you still have problems with ink on your base – contact us and we’ll assist you in problem-solving further.
Most of my plate is printing fine, but one or two areas of the plate are printing heavy. What do I do?
More often than not, this is a result of roller problems. It could be the height of your rollers or your rollers can have an uneven or flat spot on the surface (read more about roller gauges). If you processed your plates yourself, there’s the chance your plate wasn’t processed correctly and you have “fat” text, which can cause some areas to look heavier.
My chase is rocking while it’s laying flat (before I try any lockup!). What should I do?
First, figure out why your chase isn’t lying level.
- Possibility 1. Your chase might have cracked some time in the past then was welded to repair it. If this is the case, you may need to file or shave off any excess metal that might interfere with your chase being level.
- Possibility 2. You may have a low spot on your chase. You’ll want to add a shim (a small piece of metal) to the chase to level things off.
In either case, use a professional machinist. They can expertly grind down your chase if needed to create a smooth surface, or they can add a shim to your chase to level things out.
My letterpress plates are starting to curl. How do I flatten them out?
Like our skin, plates can be affected by the room temperature, humidity, and age. When humidity levels are low, the plates can look and feel brittle. With the passage of time, the thinner polymer on the plate edges are pulled towards the denser polymer text and images on the front—this causes curling. With a life expectancy of up to 1 year or more, polymer plates do age, but these simple steps can hydrate your plates and give them extra longevity.
Step 1. Place your plate back in your platemaking washout system for up to ½ a minute (or, if you don’t have a washout unit, simply immerse in water). We suggest room temperature for a quick dunking. A ½ minute may only be necessary if your plates are severely curled.
Step 2. Sponge off the water and place back in the drying oven of the platemaker for 5-10 minutes. If you don’t have a platemaker, use a hair dryer to warm the plate and make it more pliable. Placing your plate in a box and blowing the hair dryer into the box will keep the warm air more contained and warm the plates more effectively.
Step 3. After the plate warms and starts to become more pliable, place the plate in its bag and set a heavy object on it to keep the flattened shape.
This should help your plates relax so you can adhere them to your base for additional print runs.
Here’s some final advice:
- if using a hair dryer, take care to avoid putting it too close to the plates.
- be patient, as warming the plates takes time.
- watch that you don’t handle your letterpress plates too roughly after the wash and during drying so your relief images don’t chip.
- remember to store your plates flat out of direct light and in a bag so that fluctuations in humidity don’t affect the polymer.
- check your adhesive backing, to see if the adhesive needs to be re-applied to the back of your polymer plate for a secure hold on your base.
What ink should you use?
What are the most essential basic letterpress ink colors for me to have in my shop?
Try our letterpress ink basic starter kit, which includes Printing Black; Warm Red; Reflex Blue; Yellow; Transparent White (mixing white); and Pantone Black (mixing black). With these 6 colors you can mix over 250 pantone colors. If you’re ready for more, you may want to try the remaining Pantone base colors.
Which is a more environmental ink: soy ink, oil-based ink, or rubber-based ink?
We get asked a lot about soy ink from our customers, since there’s this general feeling that soy ink is THE greenest ink out there. That’s not really true. Soy sheet-fed ink has to be just 20% soy to be labeled a soy ink (the exact % of soy varies depending on the specific ink). Rubber-based and oil-based inks both have 20-30% vegetable-oil (soy and linseed). Linseed oil is the traditional letterpress ink vehicle: it’s what Gutenberg used when he first used ink. Also keep in mind that soy inks are really geared toward high speed printing and loaded with lots of driers—they’re usually very thin, liquidy inks, not ideal for letterpress. In our experience, soy inks don’t transfer well to letterpress printing, and you’ll get the same environmental impact from using oil-based or rubber-based inks.
Mix and Store Letterpress ink
Can I mix an oil-based letterpress ink with a rubber-based letterpress ink or an acrylic ink?
No, it’s not recommended to mix ink types. You can get unexpected results when you mix the different characteristics of oil-based, acrylic or rubber-based inks. The acidities, emulsifications, driers, and amounts of distillates can compete with each other and alter drying properties or tackiness.
What letterpress ink should I use: oil base, rubber base, or acrylic?
We recommend rubber-based inks for general letterpress printing—it’s the type of ink we use in our own print shop. Rubber-based inks dry by being absorbed into the paper. That makes them ideal for the cotton and bamboo blends of paper used in letterpress. Use the oil-based inks if you’d like a glossier ink that works well with coated papers . Oil based inks dry by oxidation or air drying. That is why they can form a skin on the top of the can after opening and why you won’t want to keep it on your press overnight. Try the acrylic if you’re looking for a glossier ink that can still stay open on the press. Acrylic inks will also harden in the can quicker than rubber-based inks so long term storage can be a factor.
It is best to mix only like inks from the same family—oil base with oil base, rubber base with rubber, and acrylic with acrylic.
What are the most essential basic letterpress ink colors for me to have in my shop?
Try our letterpress ink basic starter kit, which includes Printing Black; Warm Red; Reflex Blue; Yellow; Transparent White (mixing white); and Pantone Black (mixing black). With these 6 colors you can mix over 250 pantone colors. If you’re ready for more, you may want to try the remaining Pantone base colors.
How do I firm up my thin letterpress ink?
Add magnesium carbonate to your ink. Magnesium carbonate is available in our Supplies section from Boxcar Press. Inks are measured by their tackiness or stickiness and their body or how stiff it is. An ink’s body can be drippy like chocolate syrup topping or thicker like frosting or paste. The ink can also be described as being long or short. Long inks are tackier and when pulled up straight from the can will have a long tail. The white powder of magnesium carbonate will stiffen your ink and reduce tackiness.
How do I print with light toned letterpress inks on dark paper?
With letterpress, we most often print dark ink on light paper, because that is letterpress printing’s strength! Light ink on dark paper is really best suited for engraving. That said, if you really want light ink on dark paper, just be prepared for paper to show through. Think “chalkboard” for the end results. Letterpress uses transparent inks. Even with opaque white, printing light ink on dark paper will be like using a thin coat of white paint on a brown wall: you’ll see the brown color through the paint. If using a pure white ink, you can run a piece through the press twice to create a more dense color. Metallic inks will be more opaque and are the most popular choice for paper cover-up with dark papers.
Why shouldn’t I let oil-based letterpress ink dry on my rollers
Oil based inks will dry within a few hours if left unattended on press; dried oil-based inks can take a long time to clean and can even cause rollers to be permanently damaged.
Once I’m done printing, how do I clean the letterpress ink off my rollers/plates?
To clean ink off your press, we recommend California Wash used with rags or disposable shop towels. This press wash cleans up acrylic, oil based and rubber based inks well, is a low VOC solvent, and has a mild somewhat citrus odor. For an occasional cleaning and deglazing of rollers, use Easy Street Additive after press wash.
File Preparation
Don’t use a jpeg or save as a bmp file for your images!
Our favorite image mode is a .tiff. Or send us vector art images (made in Illustrator or Freehand) instead of raster images (made in Photoshop). Jpeg files will create low-quality letterpress plates that will make you unhappy; its file format is best intended for the web. Files that end in .bmp can also give unwanted results by saving as the wrong size and are also lower quality.
Creating Vector Art with Live Trace
Creating vector art via the Live Trace function in Adobe Illustrator will convert a rasterized (e.g a pixel-based) graphic into a vectorized graphic (e.g artwork made up of vectors or small points). Using the Live Trace feature to convert your artwork ensures the crispest and cleanest plate possible, as well as allows scaling and transforming the artwork without losing data or composition clarity.
Depending on what type of artwork one is looking to convert to vector, a few considerations must be taken for best results. Pixel-based graphics, such as calligraphy and line art, should be converted to image mode of bitmap beforehand and have a higher resolution of 300-600. The more graphic, stark, and higher contrast an image is, the better the Live Trace result will be. Live Trace will not always work for all images but with practice, you’ll learn to recognize what images will work best with Live Trace.
First, open the file in Adobe Illustrator. Next, double-click on the image with the default (black) arrow tool until the Live Trace toolbar appears at the top of the Illustrator tool bar.
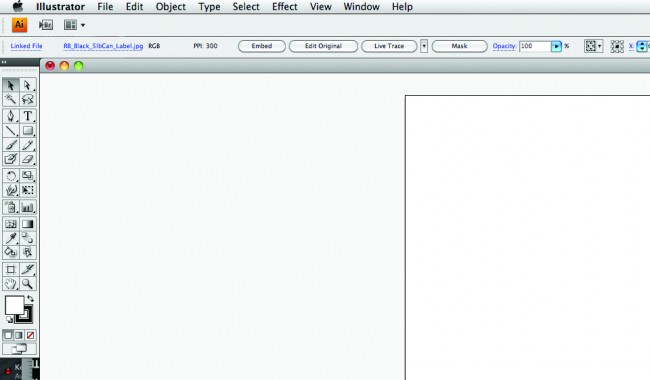
Live Trace Toolbar
Within the Live Trace toolbar in Adobe Illustrator, you have the ability to choose either between presets or experiment with different manual settings. The default is usually adequate for most purposes so click on Live Trace. The image will reshape and convert to 100% cmyk black. If you are satisfied with the conversion-to-vector on screen preview, then click “Expand” or “Live Paint” to immediately convert the file to vector. White and black anchor squares will appear on the Illustrator art board to denote the successful conversion. Click on your white artboard again to complete the trace.
Depending on the quality of the original pixel-based file and the desired effect in mind, Live Trace is a very powerful editing tool for scanned-in calligraphy and high-contrast line art.
When do I need crops and / or registration marks?
You will need crop marks if you are sending the files to us for printing. This will aid us in setting up your files into its final layout. While we will have the info on the final size of your printed piece, your crop marks in your file will help us determine that we are including all the elements you intended and in their proper place. This is especially important when your design will bleed off the page. How to place crop marks on your file, in Illustrator will depend on your CS version.
In CS3 or older – Filter > Create > Crop marks
In CS4 and newer – Effect > Crop marks
If you created your design in Illustrator and set up your artboard to measure the finished size of your printed piece, the crop marks will be outside the artboard. You will need to save your file with an eps extension so the crop marks will be included. You can then save the file as a PDF and send us both EPS and PDF. If you save as an AI extension, the crop marks were left off outside your artboard and not included in your file.
If you created your design on a larger artboard, use the rectangle tool to draw a box the desired size around your design. It will temporarily block your design until you go to your Color window and click on the white square with the red diagonal stripe. Using the selection arrow, move your box around until it’s the correct size and in the preferred place of your design. Add crop marks and save as a PDF.
How do I set up my files for 2-color printing?
The easiest way of setting up a 2-color file in an image editing program, such as Illustrator or InDesign, is to set your first color’s objects in either 100% of a color channel in CMYK mode where the three other color channels not used are set to 0%. The second color would then use 100% of a different color channel. For example, your first color’s objects may be 100% black and your second color’s objects are set to 100% cyan. If you are using this method, be sure to let us know which color channel corresponds to the ink colors you have chosen for your printing.
Our Preferred Method: If you are very comfortable with Illustrator or InDesign, you may use Pantone Swatches from the Swatch Color Libraries palette in lieu of using 100% of individual CMYK color channels. We recommend using swatches from the Pantone Solid Uncoated color book.
Do I send my files to size or scaled down?
You will need to send your files at 100% scale. We do not resize, scale up or down, or rotate any artwork. We highly recommend using the ruler feature available in Adobe Illustrator, Photoshop and InDesign to check your work to see if it is the size you want.
When exporting a PDF from Adobe Illustrator or Adobe InDesign, please double check to make sure it is the correct size by either re-opening it in Illustrator or placing it in InDesign to check the actual dimensions of your file. In InDesign you can use the Rectangle Frame tool to draw a box around your images/text to measure.
In Photoshop, use the Image Size tool to check your size. Saving your file as a .TIF locks your image size.
After I scan my artwork that I want to letterpress print, what do I do now?
Your scanner will likely save your image as a grayscale.jpg. Many scanners will only allow you to scan up to 300 dpi. If you can scan higher, choose 600 dpi. You have some options now.
If looking for the crispest and cleanest impression, you will need to convert the file to black and white only (no grey pixels). You have two methods depending on what computer software you have available. If you only have Photoshop, you will need to convert your file to one that is in image mode of bitmap. If your image dpi is currently 300 dpi, you can choose Image > Image Size and change your dpi to 600 or higher without changing the inches. Your file will temporarily be quite large but you will then save as a .TIF with LZW compression and this will resize it to something smaller and more manageable. A higher DPI can help with preserving your details and smoother pixelation while bitmapping. For exact steps to Image Mode of Bitmap, see our File Prep Tips.
If you have both Photoshop and Illustrator, you can convert your image to image mode of bitmap as directed above, then place your TIF into Adobe Illustrator, and convert the file to a vector art file via the Live Trace option. This does not always work with all files to give satisfactory results, so with practice, you will learn to recognize which files will give you a vector result you like. After converting to vector, save the file as a PDF or EPS for upload.
I want to keep my files in grayscale, how can I make them look their best?
Grayscale is a range of shades of black on a spectrum from 1 to 100. Light gray is in the lower spectrum and darker grays are in the higher spectrum. While 100% black images and text will produce crisp line art and is the norm for letterpress, sometimes you may want to print something where you want to see all the details and subtleties of the shading.
If you are trying to print a photographic image, it’s best to choose one that has areas that provide high contrast between light and dark, that is, the photo has details that are both darker gray in the upper ranges (70 to 100% of black) and lighter gray in the lower ranges (5% to 35% of black). This contrast will give the most depth and interest to the photo. If your photo has mostly shades of black in a similar range (30 – 60% of black), it will look muddy to the eye because it’s harder to discern the shading without a lack of contrast. Experimenting with the image in Photoshop by changing levels of black or adding brightness and contrast can help some with this.
If you are printing a scanned image, where you want to keep the tonal imagery, you can send the file as grayscale and we’ll apply a line screen to it. Your image will be a large shape with the tones created as little dots on the surface of the plate. The films are very sensitive and will capture shades of black down to 5%. So if your background has some color, it may be picked up by the film and show on your plate.
Halftones and grayscale images can be challenging to print with relief plates on the commonly used uncoated papers of letterpress. Call us to discuss your particular image and the results you want to achieve.
It’s not necessary to reverse your files before submitting.
We need your files and proofs to appear the way you want your final design to print – commonly called right-reading (no backward text or images). When we create your film negatives, our software does the reversing to create proper negatives, so leave that part up to us.
In Illustrator, if you want crop marks on your plate, create crop marks, not crop areas!
While using Adobe Illustrator, you will first need to create a rectangle by using the marquee tool (M) in your standard tool palette located on the left-hand side of your screen. Create the rectangle so that its dimensions are your piece’s final trim down size (e.g such as 5.5″ x 7″ for an invitation, etc). Next, while the rectangle is still selected, drag it to its proper location with respects to the artwork. This location should be the correct position intended for the crop marks. Please note that we do not add crop marks to any file at Boxcar Press, as we do not know where or what your intended trim down size is.
While the rectangle is still selected, please select EFFECT>Crop Marks to create the correct type of crop marks in Illustrator. If you need to shorten the length of the crop mark lines or thicken the line weight, you will need to expand the crop marks by selecting OBJECT>Expand or OBJECT>EXPAND APPEARANCES.
If your file has linked images, embed them in Illustrator or Export them as a PDF from InDesign.
Before sending your Illustrator files to us, embed all linked images (an option in the Links palette). If linked images aren’t embedded, they can give an error message that your links are missing and we can’t output your plates! With InDesign, export your file as a press ready PDF.
When using Illustrator, how do I outline my fonts and why is it important?
Sending all your fonts packaged is not fail-safe: all needed fonts aren’t always provided, or all your fonts may not be recognized when we open your file, causing shifting and changes in your design. On the other hand, outlining fonts is fool-proof, safe, and ideal. So outline your fonts! In Illustrator, you do this by selecting TYPE>Create Outlines. This will automatically convert your text into vector shapes. Your type will temporarily look bolder and be highlighted in blue. Click on any white area of your file and it will look normal again.
In Illustrator, the only black your submitted file should use is 100% CMYK black (CM and Y are 0%)
When opening any new document in Illustrator, choose File > Document Color mode > CMYK. To Check this before submitting your file for upload – in illustrator versions CS4 and CS5, you can open your Output-Separations Preview window. Click on the drop down window showing Off and select Separations. Click off the black eye and everything left showing on your file is not in 100%K. If you select a part of your file that is left, and look at your color palette, anything that shows a percentage of C,M, or Y needs to be corrected. To correct this – go to Select > Same > Fill (or Stroke). It should highlight everything that looks like black (but isn’t). Than go to the color palette and using the eyedropper, click on the black part of the bar (far right). The C, M, and Y will go to 0% and the K should go to 100%. Now this part of the file should disappear because it is correctly set to 100%K.
What’s the smallest type size you can hold in your platemaking?
This question is not as straightforward as it seems. We can hold a 3 pt. Times New Roman type face on 94 and 95 plate material but the real question is the next one about the thinnest line and dots the plates can hold. The font choice and characteristics of the font may limit the point size.
If you want a lineart image, use bitmap mode (don’t use a linescreen or halftone)
Most of the time, if your file contains an image, you’ll want that image to be in bitmap mode for a nice clean bite into your paper. Otherwise your image will produce a halftone, which means your image will be made up of tiny dots on the surface of your plate.
If you zoom in on your image and it is made up of tiny grey and black pixels, it’s in grayscale. We want your images all in black pixels.
You can correct this by:
- Opening your image in Photoshop and selecting Image > Mode > Grayscale.
- Select Yes if a window asks about discarding color.
- Then Select Image > Mode > Bitmap. A window will pop up looking for info – use a resolution of 600-1200 dpi and an output method of 50% threshold.
- Save your files as a tif (with LZW Compression) and send us the tif. Or insert the Tif into your Illustrator or InDesign file.
Images in higher resolution (600-1200 dpi) will give better, finer results than images in lower resolutions (72-300 dpi). If your images lose a lot of detail, you can either re-scan or adjust your levels of black. A quick explanation about the 50% threshold method. A grayscale image is made up of pixels from 1 – 100% black. When you select 50% threshold, you are telling the computer to change all pixels less than 50% black to be white and all pixels greater than 50% black to be black. So sometimes adjusting the levels of gray pixels under 50% to a little darker and over the 50% mark will keep more details in your image. We suggest experimenting with the following: Image Adjustments > Levels or Image Adjustments > Brightness and Contrast. This may give you more pleasing results in your final bitmap tif.
How large can my file be while uploading?
The largest size, data-wise, that we accept is 26MB. If your file’s data size is larger than this, determine if it can be broken up into two or more files. If you actually have a large file in MB but not in inches, check to see if your images could be saved again in Photoshop with LZW compression and placed again into your document. This great compression feature will make your files more manageable.
For alternate electronic ways, we highly recommend compressing the file down with a program such as StuffIt or ZIP. There are also many numerous online free File Transfer Sites, such as YouSendIt.com or DropBox.com, that let you upload a file and send a link for Boxcar to download.
We will also always take your files on CD by mailing to: Platemaking Department; Boxcar Press; 509 W. Fayette St. #135; Syracuse, NY 13204.
Is there a checklist for me to review with my files before submitting to platemaking?
To ease file prep woes and to ensure a smooth production transition from file to plate, it is a great help to all to give your files one last review before submitting them. The first few things to make sure is that your file’s artwork is set to the right dimensions, that you’ve checked your artwork to make sure all plate type line minimums are met, that your file is in the proper color mode or image mode and that your file is in the proper file format and extension.
When working with a file that requires multiple colors for separations, please make sure all objects are assigned to their appropriate Pantone swatch or spot color. Adobe Illustrator and InDesign are excellent programs for setting up and checking such files.
Please also remember to check out any other file prep questions to answer any unresolved questions that you may have.
If I’m scanning an image, what resolution (DPI) should it be?
Most folks want clean line art, and if this is what you’re seeking, scan at least at 600 DPI, though 1200 DPI is even better. Open your scan in Photoshop to convert your file to the Image mode of Bitmap via the 50% threshold method and an output of 600 – 1200. If you lose too much detail, you can make adjustments to your image by using Image Adjustments > Levels or Image Adjustments > Brightnesss / Contrast.
If you’d like a halftone, you can use a 300 DPI scan. With halftones, keep the image in the grayscale color mode in Photoshop, and let us know the LPI / line screen.
Either way, save your image as a TIFF with LZW compression. This will make your file size more manageable when placing into another program like Illustrator or uploading to your job ticket.
Is there a preferred LPI (Lines Per Inch) for halftones?
The ideal LPI depends on your paper and presswork, but most printers printing on uncoated paper use a 100 LPI. It’s a good balance of fine screen and easy printing. The higher the line screen, the more difficult it will be to print, because the high line-screen plate plugs up with ink in the shadows and looks murky over-all. Some printers prefer playing it safe and order 85 or 65 LPI. Using a lower LPI does make the dots coarser and more obvious. The finest line screen that we usually process is 133 LPI, although we would even question the use of 133 LPI, except on coated or hard papers.
If you’d like a halftone for your image, don’t adjust or apply an LPI in your file. Just tell us what LPI you’d like us to use, and we’ll take care of the rest.
If you tell us the paper, the type of press you’re using, and what you hope to accomplish with your halftone, we would be happy to recommend a line screen for you!
What does LPI (Lines Per Inch) do? What do I need to know about LPI and my files?
The amount of dots in an inch of a halftone is determined by the LPI, also known as line screen. The higher the LPI, the more dots there are per inch. A higher LPI means the dots are smaller and less noticeable. Letterpress printers typically use between 85-133 LPI for their halftones. We find that 100 LPI is a good choice for all plate types and is the default we apply if you don’t specify.
What is a grayscale and a halftone?
The technical definition: a halftone is a matrix of different size dots which allow printers to simulate tonal variation when printing with a single ink on press. What this means: a halftone allows you, using one color ink, to approximate various shades of color. Take a magnifying glass and look at a black and white photo printed in your local newspaper. You’ll notice the image is actually made up of different size dots. The smaller the dot, the lighter the color in the halftone. A grayscale is made up of pixels that are in varying shades of black so the tones are represented by the different shades. Once a file has a line screen applied, the grayscale is now a halftone.
Should I gang up my images/smaller files into one larger file?
If you are ordering printing from us, no. Please send individual files and we will set up for most efficient production in our shop.
If you are ordering plates and doing your own printing, yes! By ganging up the plate yourself, you have more control over the margins and gaps between the ganged up artwork. Between each individual piece, we recommend .375” for plastic-backed plates and .5” for steel-backed plates. Our negatives come out of the imagesetter in 18″ strips, so ganging up onto a 17” wide strip, and up to max 22” long, is the most economical way to make negatives. Since we like to keep our maximum plate size at 17 x 22, please break larger files into two files.
That said, if you were to send us many individual files, we’d gang up the pieces in the most cost-effective manner. If you’re using plastic-backed plates, after we gang up your files, we’ll ship your job as a single plate and you can trim them easily yourself, using scissors or an Exacto.
If you’re using steel-backed plates and we gang up your files for you, we’ll ship your job as a single plate, unless you provide a cutting diagram for us. If you are submitting a ganged up file, keep in mind the fingers of our employees who have to trim your metal plates and leave us enough room around your text/images to hold the plate safely while we cut.
Can you scan my camera-ready artwork?
Yes! Simply mail us your camera-ready art and we will scan it in for you. When possible, we love art work that’s on smooth, bright white paper or drafting vellum. Textured paper makes our job more difficult as the scan will pick up any background patterns, paper shadings, paper texture, etc. We are faithful to originals: if you require modification or retouching, you may be charged for additional file preparation time at our shop rate of $60/hour. We’ll contact you before we bill for additional file prep. We can scan, in house, artwork up to 12 x 17 inches.
What’s the largest size plate you can make?
For the 94FL, KF95, KF152, and 152SB plates, the largest size plate we can process is 17.5” x 22.5” (where your image area is 17” x 22”). For all other plates, the largest size plate is 16” x 22” (image area is 15.5” x 22”)
What’s the thinnest line and smallest dot you can hold on a plate?
It depends on the plate (though no hair lines, please!). If your plate has a 94 or 95 in the product name, we recommend at least a 0.25 point thickness (or larger). If your plate has 145 or 152 in the product name, we recommend at least a .35 point/.007″ thickness (or larger). Watch out for typefaces with swirly curves that thin or have breaks or fonts with fine cross bars.
For dots, we recommend at least a 1 pt diameter if your plate has a 94 or 95 in the product name. Boost that to 1.25pt diameter for plates that are 145 or 152 in thickness. Each of those dots has to stand on it’s own on the plate and that thickness will provide the support at the base of the plate to hold the dot. Watch out for typefaces where the dots on the “I’s or periods are small, as seen in many sans serif fonts that are decorative, free form or look hand drawn.
Undersize lines and dots may appear on your plate as wavy or be missing completely so checking this is very important for a good file and usable plate.
Mark as helpful. 204
L Letterpress Machine
What do I need to be able to letterpress print with your photopolymer plates?
You’ll need:
- a printing base. The polymer plates we create aren’t type high by themselves. They need to be mounted on a base to make a type-high printing surface. We recommend our Boxcar Base system. Letterpress printers also use magnetic bases from Patmag or Bunting. If you are printing on a DIY press such as L Letterpress, please refer to this tutorial.
- a Printing press. Remember that most letterpress printing presses people purchase will not be ready to print beautifully right away and a little tender loving care will be needed. Be prepared to purchase new rollers or do other maintenance on your press!
- Ink. we recommend Van Son rubber-based letterpress inks, which you can order in any uncoated Pantone number! Or you can purchase the Van Son base colors and mix your own colors. View the inks we carry.
- various pressroom supplies, including printers furniture, quoins, tympan paper, type gauge, ink knife and (if using a platen press) Kort gauge pins or Henry gage pins.
- a fashionable printing apron
We now sell letterpress starter packs, which contain a lot of what you’ll need to get started.
What’s the biggest problem that printers new to photopolymer encounter?
Photopolymer plates offer an way to letterpress print extremely detailed designs with a deep heavy impression (or a kiss impression if you’re so inclined). The chief problem that new photopolymer users encounter usually deals with roller height/roller condition. But no worries! Unlike larger problems like war or global warming, roller issues do have concrete and relatively easy solutions. We recommend rubber rollers and, if using a platen press, solid trucks. If switching from lead type/magnesium plates, you’ll want to keep a much closer eye on your rollers. You may find our general printing FAQ’s useful, especially if you’ll be using a Boxcar Base.
Why Use Us
I need my order shipped today. By what time do I need to place the order?
For supply orders: Orders typically ship within 1-2 business days. If you need your order immediately, we encourage you to request expedited overnight shipping. However, if you’re in a serious letterpress emergency, please place your order before noon EST and mention that you’d like same day shipping. We’ll do our best to make it happen!
For platemaking: place your same day rushes by 1 p.m. EST.
How should I upload corrected files?
Sometimes we may notify you that your files have an error and need correcting. Follow the instructions to make those corrections and rename your file, preferably with the words “New”, “Revised”, or “Corrected” in the file name. Please don’t upload a changed file with the same name as the original file as we won’t be able to tell it’s a replacement and new file.
Re-upload new files to your current platemaking ticket. Log in to Boxcarpress.com with your username and password. Click on the applicable ticket to upload or drag and drop the new revised file.
You can only upload files to your ticket if your platemaking ticket’s status is either set as “Received”, “Pending” or “On Hold”. We will see new files and get to work to process your plates.
If you find that your ticket’s status is “In Platemaking”, you will need to call us at 315-473-0930 to see if it is possible to still add corrected or revised files.
If your ticket status is “Billing Complete”, “Order Complete” or “Shipped”, your ticket is unable to be altered.
Do I send my files reversed for your processing?
No. Please send your artwork and text right-reading as you want it to appear as the final print. We will make a film negative here at Boxcar Press for you. However, if you are planning to use your files in a different process than printing, please call us to discuss how best to prep your files.
Can you explain how you calculate the file dimensions for billing
Here is how we compute dimensions – we gang all your files up together and draw a box around the “black” part – the images and text. Now we know the length and the width. We multiply these two numbers together and this is your square inches total. We then multiply this square inch number by your square inch price of $0.62/sq inch or $0.67/sq inch.
Example:
9″ x 8″ is your “black part”
9” x 8” = 72 sq inches x $0.67 = $50.40
If your file has crop marks, we measure outside the crop marks. So if you don’t need crop marks, consider leaving them off to save a little cash.
Can you explain the same day rush service and fee?
Boxcar Press has a pretty fast platemaking turnaround service with our one business day turnaround. But if you have an even greater need for speed, consider our Same Day Rush Service. If you create your job ticket, upload your files before 1 pm EST, and choose Same Day, we’ll get your files out the door to arrive the next Business Day via UPS. Of course, speed comes at a price, the fee for Same Day Rush starts at $45 or 40% (whichever is greater) plus the regular cost of the plate plus your overnight shipping costs. Your minimum cost for a Same Day Rush plate is $75 before shipping and goes up from there.
So, we encourage you to make use of the one day turnaround as much as possible. Create your job ticket and upload your files before 5:30 pm EST and we’ll ship on the next business day, assuming your files are in tip-top A1 shape. File corrections may delay your shipping.
How do I take advantage of the free 2 day shipping?
Boxcar Press offers free two day shipping for platemaking orders that are over 120 square inches as of August 15th, 2014. If your order qualifies, this option will appear as the default shipping choice.
Please remember these details about this service:
- Two day service is ground service for those already within our 1 or 2 days service area (New York state, the Northeast to Maine, down to Virginia, and parts of Wisconsin, Illinois and Kentucky).
- If your usual UPS ground is 3 day – 6 days, you will receive UPS 2 day Air.
- If you have selected any overnight air services for shipping, we will NOT downgrade for free 2 day service. We will believe that you really need the faster overnight service.
- If you really do need 2 day Air service, please choose the 2 day Air and don’t wait for us to upgrade you from ground or a slower service. It’s hard to make UPS deliver faster once it’s out for shipping.
- Free 2 day air applies to business days and not Saturday delivery.
How can I check the progress of my order?
Log on to your account in platemaking. It will take you to your Orders page where the current status will be visible.
Status Explanations:
- Pending – Your order has been started but all the steps have not been completed. This requires further action on your part.
- Received – Waiting for us to review your files.
- On hold and awaiting action on your part.
- On Hold No Files Received – Please try uploading again or call for assistance.
- On Hold Bad Files – Your files need attention. You will receive an email indicating your order is on hold with the problem and asking you to correct and upload new files. File errors may include your files measure too large to plate, not in correct color mode, lines or dots too thin, files are in grayscale, etc.
- On Hold – Credit Card declined or expiration is passed. There is a problem with your payment, please contact us.
- In Platemaking – We are in production making your films to make plates. Your ticket is locked as we are moving ahead.
- Billing complete – Your platemaking job is billed and awaiting shipping.
- Shipping Complete – We have shipped and still need to Invoice your order.
- Order Complete – We closed out your order as we have created a shipping label and your package is out the door. The day your order was completed was the day it shipped.
How do I cancel an order?
For supplies, please call us as soon as possible to cancel your order. We will have to discuss refunds and crediting accounts as your online Supply Order has already been charged for payment.
For Platemaking – you can call us right away or you may be able to cancel your order online, if your status is still in RECEIVED or ON HOLD.
Log on to platemaking and you’ll see all current orders. Choose Complete Order to cancel your order. Confirm when it asks if you want to proceed. Your order status will reflect Order Cancelled.
The option to cancel is not available once we move your ticket into platemaking production. Cancelling after this step may incur some production costs. Please call us right away to minimize those costs, if possible.
Once my order is placed online, how do I make a change to it?
Supply orders: please call us or e-mail us as soon as possible.
Platemaking: First, log-in to see your order and check its current status. If we haven’t begun processing your order (STATUS – RECEIVED), you’ll be able to change your order details or upload files online. If we’ve already begun working on your order (STATUS – IN PLATEMAKING), please call us or e-mail us immediately, as you won’t be able to adjust your order online and we can see if the production process is already too far along. At this point, we can still change your shipping options and shipping addresses. If your status is BILLING COMPLETE, we will not be able to make any adjustments at this time.
Do you ship internationally?
Supplies: We ship supplies to Canada via UPS Standard or UPS Worldwide Saver and US Postal Service.
We ship international orders (outside of Canada) via UPS Worldwide Saver and US Postal Express Mail.
We think our online ordering system is pretty nifty but of course you can phone in your order to us by calling 315-473-0930. We love to talk to our customers.
Platemaking: We ship platemaking orders to Canada via UPS Standard or UPS Worldwide Saver and US Postal Service. We can ship Worldwide Saver to any international location or opt to use the US Postal Express Mail. These options are all at the click of a button through out platemaking site.
Printing: Yes, we love working with international clients and sending off printed letterpress beauties to destinations far and near.
What’s the largest size plate you can make?
For the 94FL, KF95, KF152, and 152SB plates, the largest size plate we can process is 17.5” x 22.5” (where your image area is 17” x 22”). For all other plates, the largest size plate is 16” x 22” (image area is 15.5” x 22”)
How do I know when my order has been shipped?
For platemaking, the day your order is completed (Order Complete) is the day your order ships. You will get a UPS tracking number via the log-in email on your account. Your invoice will be shipped in a separate email. Review your Order History to see all past and current orders for your status. For international orders using the US Postal Service, you will receive an email with your tracking number.
For Supplies – an email will be sent with the tracking number.
When will I receive my order?
Photopolymer supply orders ship from our warehouse within 1-2 business days.
Custom Platemaking orders ship depending on the service you choose:
We offer a 1 business day turnaround, or Same Day Rush – an extra fee service.
For shipping in the USA, we offer UPS Ground, UPS 3 day air Service, UPS 2 day air Service, UPS Overnight morning, UPS afternoon Saver and UPS early Am (before coffee) 8:30 am service.
For International Customers, we offer US Postal Priority or Express Mail and UPS Worldwide Saver.
Remember that the days refer to business days and not weekends.
I want to use photopolymer to do something other than letterpress printing. How do I know what plate to use?
While our troubleshooting only extends to using photopolymer plates for letterpress printing, there are literally dozens of other uses for photopolymer plates. If you know the tech specs of the plate that you need, or if you can send us a sample of the plate required for your application, we would be happy to try and recommend a plate that we have in stock that will work for you.
We have innovative people using our plates for metal clay jewelry making, translucent porcelain, and leather work. We always like to hear what you want to try.
How do I know what plate type to choose?
This depends on the type of base you own. See the plate choices part of our web site for more information! In general, you will choose a plate with two things in mind, your base system (Boxcar or Magnetic) and your printing press. Our plastic backed plates correspond to a particular Boxcar Base and steel backed plates will correspond to either the Patmag or Bunting base.
If you are using one of the Do It Yourself home letterpress systems, we suggest the KF152 plastic backed plates.
If you are using an etching press, call us and we’ll suggest a plate, based upon a few questions about your setup.
As you are likely hand inking with these last two presses, please remember to ask us to SEND STRIPS in your platemaking order. They will be very helpful with your inking brayer for an easier inking.
How large can my file be while uploading?
The largest size, data-wise, that we accept is 26MB. If your file’s data size is larger than this, determine if it can be broken up into two or more files. If you actually have a large file in MB but not in inches, check to see if your images could be saved again in Photoshop with LZW compression and placed again into your document. This great compression feature will make your files more manageable.
For alternate electronic ways, we highly recommend compressing the file down with a program such as StuffIt or ZIP. There are also many numerous online free File Transfer Sites, such as YouSendIt.com or DropBox.com, that let you upload a file and send a link for Boxcar to download.
We will also always take your files on CD by mailing to: Platemaking Department; Boxcar Press; 509 W. Fayette St. #135; Syracuse, NY 13204.
Is there a checklist for me to review with my files before submitting to platemaking?
To ease file prep woes and to ensure a smooth production transition from file to plate, it is a great help to all to give your files one last review before submitting them. The first few things to make sure is that your file’s artwork is set to the right dimensions, that you’ve checked your artwork to make sure all plate type line minimums are met, that your file is in the proper color mode or image mode and that your file is in the proper file format and extension.
When working with a file that requires multiple colors for separations, please make sure all objects are assigned to their appropriate Pantone swatch or spot color. Adobe Illustrator and InDesign are excellent programs for setting up and checking such files.
Please also remember to check out any other file prep questions to answer any unresolved questions that you may have.
Should I gang up my images/smaller files into one larger file?
If you are ordering printing from us, no. Please send individual files and we will set up for most efficient production in our shop.
If you are ordering plates and doing your own printing, yes! By ganging up the plate yourself, you have more control over the margins and gaps between the ganged up artwork. Between each individual piece, we recommend .375” for plastic-backed plates and .5” for steel-backed plates. Our negatives come out of the imagesetter in 18″ strips, so ganging up onto a 17” wide strip, and up to max 22” long, is the most economical way to make negatives. Since we like to keep our maximum plate size at 17 x 22, please break larger files into two files.
That said, if you were to send us many individual files, we’d gang up the pieces in the most cost-effective manner. If you’re using plastic-backed plates, after we gang up your files, we’ll ship your job as a single plate and you can trim them easily yourself, using scissors or an Exacto.
If you’re using steel-backed plates and we gang up your files for you, we’ll ship your job as a single plate, unless you provide a cutting diagram for us. If you are submitting a ganged up file, keep in mind the fingers of our employees who have to trim your metal plates and leave us enough room around your text/images to hold the plate safely while we cut.
What programs do you support?
Our favorite ways to receive files for letterpress platemaking are by you sending us a press-ready PDF file (with fonts embedded) for platemaking. This PDF will serve as both your hard copy and your plate file. No additional faxing or email needed.
Our second favorite way is for you to send an EPS or AI file for platemaking. We also accept PDF digital files in current versions of other major design programs (i.e. Quark, InDesign, Freehand).
If you are creating your files in Photoshop, we like to say that this program is good for images but not so great for text. It’s best to convert your grayscale images in Photoshop and place them into Illustrator where you will add your text. If Photoshop is your only option, start with a file that is 600 dpi minimum so you can minimize the pixelation of your text when you convert files. More on file conversion to Image Mode of Bitmap under File Prep Tips. We prefer tif files from photoshop for upload.
Note, we can often make plates from PDFs created from Word files, however, Word is not able to format your file exactly the way we need. So please tell us your file was originally a Word document so we can anticipate and make corrections. If you are designing in Word, we suggest that you don’t use any funky or crazy fonts we won’t have access to. Oftentimes, they will just print as strange characters. Your images placed in Word will usually require some corrections too. You can email your files to plates@boxcarpress.com for an evaluation first and we’ll advise on how letterpress friendly it is.
Ordering Plates Info
Should I gang up my images/smaller files into one larger file?
If you are ordering printing from us, no. Please send individual files and we will set up for most efficient production in our shop.
If you are ordering plates and doing your own printing, yes! By ganging up the plate yourself, you have more control over the margins and gaps between the ganged up artwork. Between each individual piece, we recommend .375” for plastic-backed plates and .5” for steel-backed plates. Our negatives come out of the imagesetter in 18″ strips, so ganging up onto a 17” wide strip, and up to max 22” long, is the most economical way to make negatives. Since we like to keep our maximum plate size at 17 x 22, please break larger files into two files.
That said, if you were to send us many individual files, we’d gang up the pieces in the most cost-effective manner. If you’re using plastic-backed plates, after we gang up your files, we’ll ship your job as a single plate and you can trim them easily yourself, using scissors or an Exacto.
If you’re using steel-backed plates and we gang up your files for you, we’ll ship your job as a single plate, unless you provide a cutting diagram for us. If you are submitting a ganged up file, keep in mind the fingers of our employees who have to trim your metal plates and leave us enough room around your text/images to hold the plate safely while we cut.
How do I know what plate type to choose?
This depends on the type of base you own. See the plate choices part of our web site for more information! In general, you will choose a plate with two things in mind, your base system (Boxcar or Magnetic) and your printing press. Our plastic backed plates correspond to a particular Boxcar Base and steel backed plates will correspond to either the Patmag or Bunting base.
If you are using one of the Do It Yourself home letterpress systems, we suggest the KF152 plastic backed plates.
If you are using an etching press, call us and we’ll suggest a plate, based upon a few questions about your setup.
As you are likely hand inking with these last two presses, please remember to ask us to SEND STRIPS in your platemaking order. They will be very helpful with your inking brayer for an easier inking.
When will I receive my order?
Photopolymer supply orders ship from our warehouse within 1-2 business days.
Custom Platemaking orders ship depending on the service you choose:
We offer a 1 business day turnaround, or Same Day Rush – an extra fee service.
For shipping in the USA, we offer UPS Ground, UPS 3 day air Service, UPS 2 day air Service, UPS Overnight morning, UPS afternoon Saver and UPS early Am (before coffee) 8:30 am service.
For International Customers, we offer US Postal Priority or Express Mail and UPS Worldwide Saver.
Remember that the days refer to business days and not weekends.
How do I know when my order has been shipped?
For platemaking, the day your order is completed (Order Complete) is the day your order ships. You will get a UPS tracking number via the log-in email on your account. Your invoice will be shipped in a separate email. Review your Order History to see all past and current orders for your status. For international orders using the US Postal Service, you will receive an email with your tracking number.
For Supplies – an email will be sent with the tracking number.
Do you ship internationally?
Supplies: We ship supplies to Canada via UPS Standard or UPS Worldwide Saver and US Postal Service.
We ship international orders (outside of Canada) via UPS Worldwide Saver and US Postal Express Mail.
We think our online ordering system is pretty nifty but of course you can phone in your order to us by calling 315-473-0930. We love to talk to our customers.
Platemaking: We ship platemaking orders to Canada via UPS Standard or UPS Worldwide Saver and US Postal Service. We can ship Worldwide Saver to any international location or opt to use the US Postal Express Mail. These options are all at the click of a button through out platemaking site.
Printing: Yes, we love working with international clients and sending off printed letterpress beauties to destinations far and near.
How do I take advantage of the free 2 day shipping?
Boxcar Press offers free two day shipping for platemaking orders that are over 120 square inches as of August 15th, 2014. If your order qualifies, this option will appear as the default shipping choice.
Please remember these details about this service:
- Two day service is ground service for those already within our 1 or 2 days service area (New York state, the Northeast to Maine, down to Virginia, and parts of Wisconsin, Illinois and Kentucky).
- If your usual UPS ground is 3 day – 6 days, you will receive UPS 2 day Air.
- If you have selected any overnight air services for shipping, we will NOT downgrade for free 2 day service. We will believe that you really need the faster overnight service.
- If you really do need 2 day Air service, please choose the 2 day Air and don’t wait for us to upgrade you from ground or a slower service. It’s hard to make UPS deliver faster once it’s out for shipping.
- Free 2 day air applies to business days and not Saturday delivery.
Do I send my files to size or scaled down?
You will need to send your files at 100% scale. We do not resize, scale up or down, or rotate any artwork. We highly recommend using the ruler feature available in Adobe Illustrator, Photoshop and InDesign to check your work to see if it is the size you want.
When exporting a PDF from Adobe Illustrator or Adobe InDesign, please double check to make sure it is the correct size by either re-opening it in Illustrator or placing it in InDesign to check the actual dimensions of your file. In InDesign you can use the Rectangle Frame tool to draw a box around your images/text to measure.
In Photoshop, use the Image Size tool to check your size. Saving your file as a .TIF locks your image size.
Can you explain how you calculate the file dimensions for billing
Here is how we compute dimensions – we gang all your files up together and draw a box around the “black” part – the images and text. Now we know the length and the width. We multiply these two numbers together and this is your square inches total. We then multiply this square inch number by your square inch price of $0.62/sq inch or $0.67/sq inch.
Example:
9″ x 8″ is your “black part”
9” x 8” = 72 sq inches x $0.67 = $50.40
If your file has crop marks, we measure outside the crop marks. So if you don’t need crop marks, consider leaving them off to save a little cash.
Order History
When will I receive my order?
Photopolymer supply orders ship from our warehouse within 1-2 business days.
Custom Platemaking orders ship depending on the service you choose:
We offer a 1 business day turnaround, or Same Day Rush – an extra fee service.
For shipping in the USA, we offer UPS Ground, UPS 3 day air Service, UPS 2 day air Service, UPS Overnight morning, UPS afternoon Saver and UPS early Am (before coffee) 8:30 am service.
For International Customers, we offer US Postal Priority or Express Mail and UPS Worldwide Saver.
Remember that the days refer to business days and not weekends.
How do I know when my order has been shipped?
For platemaking, the day your order is completed (Order Complete) is the day your order ships. You will get a UPS tracking number via the log-in email on your account. Your invoice will be shipped in a separate email. Review your Order History to see all past and current orders for your status. For international orders using the US Postal Service, you will receive an email with your tracking number.
For Supplies – an email will be sent with the tracking number.
Once my order is placed online, how do I make a change to it?
Supply orders: please call us or e-mail us as soon as possible.
Platemaking: First, log-in to see your order and check its current status. If we haven’t begun processing your order (STATUS – RECEIVED), you’ll be able to change your order details or upload files online. If we’ve already begun working on your order (STATUS – IN PLATEMAKING), please call us or e-mail us immediately, as you won’t be able to adjust your order online and we can see if the production process is already too far along. At this point, we can still change your shipping options and shipping addresses. If your status is BILLING COMPLETE, we will not be able to make any adjustments at this time.
How do I cancel an order?
For supplies, please call us as soon as possible to cancel your order. We will have to discuss refunds and crediting accounts as your online Supply Order has already been charged for payment.
For Platemaking – you can call us right away or you may be able to cancel your order online, if your status is still in RECEIVED or ON HOLD.
Log on to platemaking and you’ll see all current orders. Choose Complete Order to cancel your order. Confirm when it asks if you want to proceed. Your order status will reflect Order Cancelled.
The option to cancel is not available once we move your ticket into platemaking production. Cancelling after this step may incur some production costs. Please call us right away to minimize those costs, if possible.
How can I check the progress of my order?
Log on to your account in platemaking. It will take you to your Orders page where the current status will be visible.
Status Explanations:
- Pending – Your order has been started but all the steps have not been completed. This requires further action on your part.
- Received – Waiting for us to review your files.
- On hold and awaiting action on your part.
- On Hold No Files Received – Please try uploading again or call for assistance.
- On Hold Bad Files – Your files need attention. You will receive an email indicating your order is on hold with the problem and asking you to correct and upload new files. File errors may include your files measure too large to plate, not in correct color mode, lines or dots too thin, files are in grayscale, etc.
- On Hold – Credit Card declined or expiration is passed. There is a problem with your payment, please contact us.
- In Platemaking – We are in production making your films to make plates. Your ticket is locked as we are moving ahead.
- Billing complete – Your platemaking job is billed and awaiting shipping.
- Shipping Complete – We have shipped and still need to Invoice your order.
- Order Complete – We closed out your order as we have created a shipping label and your package is out the door. The day your order was completed was the day it shipped.
Can you explain how you calculate the file dimensions for billing
Here is how we compute dimensions – we gang all your files up together and draw a box around the “black” part – the images and text. Now we know the length and the width. We multiply these two numbers together and this is your square inches total. We then multiply this square inch number by your square inch price of $0.62/sq inch or $0.67/sq inch.
Example:
9″ x 8″ is your “black part”
9” x 8” = 72 sq inches x $0.67 = $50.40
If your file has crop marks, we measure outside the crop marks. So if you don’t need crop marks, consider leaving them off to save a little cash.
Pricing
Should I gang up my images/smaller files into one larger file?
If you are ordering printing from us, no. Please send individual files and we will set up for most efficient production in our shop.
If you are ordering plates and doing your own printing, yes! By ganging up the plate yourself, you have more control over the margins and gaps between the ganged up artwork. Between each individual piece, we recommend .375” for plastic-backed plates and .5” for steel-backed plates. Our negatives come out of the imagesetter in 18″ strips, so ganging up onto a 17” wide strip, and up to max 22” long, is the most economical way to make negatives. Since we like to keep our maximum plate size at 17 x 22, please break larger files into two files.
That said, if you were to send us many individual files, we’d gang up the pieces in the most cost-effective manner. If you’re using plastic-backed plates, after we gang up your files, we’ll ship your job as a single plate and you can trim them easily yourself, using scissors or an Exacto.
If you’re using steel-backed plates and we gang up your files for you, we’ll ship your job as a single plate, unless you provide a cutting diagram for us. If you are submitting a ganged up file, keep in mind the fingers of our employees who have to trim your metal plates and leave us enough room around your text/images to hold the plate safely while we cut.
How do I know what plate type to choose?
This depends on the type of base you own. See the plate choices part of our web site for more information! In general, you will choose a plate with two things in mind, your base system (Boxcar or Magnetic) and your printing press. Our plastic backed plates correspond to a particular Boxcar Base and steel backed plates will correspond to either the Patmag or Bunting base.
If you are using one of the Do It Yourself home letterpress systems, we suggest the KF152 plastic backed plates.
If you are using an etching press, call us and we’ll suggest a plate, based upon a few questions about your setup.
As you are likely hand inking with these last two presses, please remember to ask us to SEND STRIPS in your platemaking order. They will be very helpful with your inking brayer for an easier inking.
Do I send my files to size or scaled down?
You will need to send your files at 100% scale. We do not resize, scale up or down, or rotate any artwork. We highly recommend using the ruler feature available in Adobe Illustrator, Photoshop and InDesign to check your work to see if it is the size you want.
When exporting a PDF from Adobe Illustrator or Adobe InDesign, please double check to make sure it is the correct size by either re-opening it in Illustrator or placing it in InDesign to check the actual dimensions of your file. In InDesign you can use the Rectangle Frame tool to draw a box around your images/text to measure.
In Photoshop, use the Image Size tool to check your size. Saving your file as a .TIF locks your image size.
Turnaround
I need my order shipped today. By what time do I need to place the order?
For supply orders: Orders typically ship within 1-2 business days. If you need your order immediately, we encourage you to request expedited overnight shipping. However, if you’re in a serious letterpress emergency, please place your order before noon EST and mention that you’d like same day shipping. We’ll do our best to make it happen!
For platemaking: place your same day rushes by 1 p.m. EST.
Can you explain the same day rush service and fee?
Boxcar Press has a pretty fast platemaking turnaround service with our one business day turnaround. But if you have an even greater need for speed, consider our Same Day Rush Service. If you create your job ticket, upload your files before 1 pm EST, and choose Same Day, we’ll get your files out the door to arrive the next Business Day via UPS. Of course, speed comes at a price, the fee for Same Day Rush starts at $45 or 40% (whichever is greater) plus the regular cost of the plate plus your overnight shipping costs. Your minimum cost for a Same Day Rush plate is $75 before shipping and goes up from there.
So, we encourage you to make use of the one day turnaround as much as possible. Create your job ticket and upload your files before 5:30 pm EST and we’ll ship on the next business day, assuming your files are in tip-top A1 shape. File corrections may delay your shipping.
It’s a Crazy Friday and I have to print over the weekend. Can you help?
We can help! Get your files into us by 1 p.m. EST on Friday (and make sure your design files are prepared just right!). Choose our rush service which means we’ll ship your plates Friday. Choose overnight AM for shipping and Saturday delivery and you’ll have your plates in hand by Saturday, noon. Hooray!
Shipping
When will I receive my order?
Photopolymer supply orders ship from our warehouse within 1-2 business days.
Custom Platemaking orders ship depending on the service you choose:
We offer a 1 business day turnaround, or Same Day Rush – an extra fee service.
For shipping in the USA, we offer UPS Ground, UPS 3 day air Service, UPS 2 day air Service, UPS Overnight morning, UPS afternoon Saver and UPS early Am (before coffee) 8:30 am service.
For International Customers, we offer US Postal Priority or Express Mail and UPS Worldwide Saver.
Remember that the days refer to business days and not weekends.
How do I know when my order has been shipped?
For platemaking, the day your order is completed (Order Complete) is the day your order ships. You will get a UPS tracking number via the log-in email on your account. Your invoice will be shipped in a separate email. Review your Order History to see all past and current orders for your status. For international orders using the US Postal Service, you will receive an email with your tracking number.
For Supplies – an email will be sent with the tracking number.
Do you ship internationally?
Supplies: We ship supplies to Canada via UPS Standard or UPS Worldwide Saver and US Postal Service.
We ship international orders (outside of Canada) via UPS Worldwide Saver and US Postal Express Mail.
We think our online ordering system is pretty nifty but of course you can phone in your order to us by calling 315-473-0930. We love to talk to our customers.
Platemaking: We ship platemaking orders to Canada via UPS Standard or UPS Worldwide Saver and US Postal Service. We can ship Worldwide Saver to any international location or opt to use the US Postal Express Mail. These options are all at the click of a button through out platemaking site.
Printing: Yes, we love working with international clients and sending off printed letterpress beauties to destinations far and near.
How do I take advantage of the free 2 day shipping?
Boxcar Press offers free two day shipping for platemaking orders that are over 120 square inches as of August 15th, 2014. If your order qualifies, this option will appear as the default shipping choice.
Please remember these details about this service:
- Two day service is ground service for those already within our 1 or 2 days service area (New York state, the Northeast to Maine, down to Virginia, and parts of Wisconsin, Illinois and Kentucky).
- If your usual UPS ground is 3 day – 6 days, you will receive UPS 2 day Air.
- If you have selected any overnight air services for shipping, we will NOT downgrade for free 2 day service. We will believe that you really need the faster overnight service.
- If you really do need 2 day Air service, please choose the 2 day Air and don’t wait for us to upgrade you from ground or a slower service. It’s hard to make UPS deliver faster once it’s out for shipping.
- Free 2 day air applies to business days and not Saturday delivery.
Base and Plate 1
Can I lock up two different Boxcar Bases and use them together?
Yes, you can certainly lock up two Boxcar Bases into one chase and print, and in most situations print a letterpress plate that spans the two bases. We inspect our Boxcar Bases and verify they are within plus/minus 0.001” in thickness, parallel and flatness. Still, we’d like your bases to be even closer in height than +/- 0.001″ if possible. Here’s how to do this depending on your situation.
- You purchase one base and have it cut into two pieces: use each piece individually or lock them both back up together for a larger base surface. Your two cut sides should match up perfectly. Slide them together and using quoins, furniture and leading, fill the chase on all sides around the two bases to support the pieces and have a good strong lock-up.
- You already have two different bases in your shop: These should be fine to print. There may be slight variation within the +/- 0.001″ tolerance, so find the two sides most similar in thickness and slide them together.
- You have a base. You want to purchase another base to print with at the same time: We keep detailed specs on each base we sell. When you order your second base, let us know your original base’s serial number—we’ll make sure the bases we ship to you are identical heights so you can butt them together and have a very even printing surface. Where do you find your serial number – on the bottom edge under the Boxcar text.
- You are going to purchase two bases to print with at the same time: Just let us know that you’re planning to print with them at the same time, and we’ll choose the two closest in height from our inventory.
If I have a 10 x 15 chase on my press, why can’t I use a 10 x 15 base?
We totally understand that you want to get the most use and space out of your press. However, knowing about some of the challenges you will face can help you make decisions about the correct size.
First, keep in mind that every press, like every person, has a limit to its strength. A press with a 10 x 15 chase will never be able to hammer a 10 x 15 block of text. You’ll be able to get a good impression using about 60-70% of your chase, depending on your form. Secondly, your base needs to stay put in your chase with a good lockup. To secure your base in your chase, you need to make room for the quoins plus furniture for distributing the weight of the base, and gauge pins. Gauge pins fit in the space outside the base and over the furniture.
We recommend checking out our Base Selection Chart which recommends the ideal size base for your chase. With a 10×15 chase, we would recommend a 9×12 base, for instance.
If you really want to max out the base size, keep in mind your base should be at least 1 inch, preferably 1.5 inches, smaller than your chase. If you use a lot of paper that is precut, it is most likely smaller than your base. This can make it challenging to place your gauge pins and still hold the paper and not hit the base. One safety note, the larger the base in your platen press, the further you have to reach into the press to place your paper. This is very important with a larger press with a motor, so take into consideration your comfortable reach, the speed of the press, and your fingers when locking up a larger base.
What’s the maximum size polymer plate I can print on my base?
Your maximum plate size is actually the size of your base — your photopolymer plates can go right up to the edge of your base. Obviously your relief images and text should not hang over your edge. This is true for both magnetic bases and the Boxcar Base. If you need a little more base for occasional projects, consider a Boxcar Base scrap to add that extra ½” – 1”. Read more about maximum base size.
Letterpress Manual
How do I firm up my thin letterpress ink?
Add magnesium carbonate to your ink. Magnesium carbonate is available in our Supplies section from Boxcar Press. Inks are measured by their tackiness or stickiness and their body or how stiff it is. An ink’s body can be drippy like chocolate syrup topping or thicker like frosting or paste. The ink can also be described as being long or short. Long inks are tackier and when pulled up straight from the can will have a long tail. The white powder of magnesium carbonate will stiffen your ink and reduce tackiness.
Why shouldn’t I let oil-based letterpress ink dry on my rollers
Oil based inks will dry within a few hours if left unattended on press; dried oil-based inks can take a long time to clean and can even cause rollers to be permanently damaged.
What will I need to do to my platen press before printing with polymer and a Boxcar Base (especially if my printing is blobby and/or has a “halo”)? i.e. how do I add tape to my rails?
Every platen or lever press has wear on the rails and needs tape on the rails to raise the rollers to the right height. This is whether you use lead type or polymer—although the problem surfaces more frequently on polymer if the roller rails aren’t set correctly. You have to build up the rails that the roller trucks travel on so that the rollers just graze the surface of the form. The best way to do this is to add equal layers of masking or strapping tape to each rail. Keep building up the rails in this fashion until whatever you’re printing doesn’t ink up at all (i.e. bring the rollers up just past the point where the rollers ink the plate). Then take off one layer of tape so that the rollers drop down with minimum contact to the plate. This will keep ink from getting on the backing of the plate and the base, and it will also help make your printing crisper. It’s not uncommon to have to add as much as a 1/16″—or sometimes 1/8″—in tape in order to get the rails to the right height. These presses are often 100 years old and have 100 years of wear that you have to overcome. We do not recommend that you adjust your trucks or printing plate/base for this problem. Better printing results from type-high rollers. After you add tape to your rails, we recommend using a roller gauge to perfect the height of your rollers.
What are roller gauges and why do I need them?
Roller gauges are especially indispensable with a platen press. Letterpress rollers need to be positioned just right in order to deposit a thin film of ink onto the surface of the form, without squeezing ink over the edges. A roller gauge will help you accurately measure the height of your rollers so you can produce the crispest printing that your press is capable of. We sell roller gauges, precision ground to type high, which are also very fashionable.
When your rollers are positioned correctly, your printing will look beautifully crisp. But if your rollers aren’t positioned at the right height, your printing will have a halo effect: dark around the edges and/or chunkier/blotchier than it should be. If you ever notice ink on the back of your polymer plate or on your base — it’s a roller gauge emergency! Adjust your rollers now! We have a great video on setting roller gauge height in our Boxcar Training Videos and step by steps are listed here.
Step 1. While your press is inked up, remove the chase (on platen presses) or the base (on a Vandercook).
Step 2. We recommend checking the roller height in the four corners of the press bed. We’ll start in the upper right hand corner. Engage the form rollers and position them over the upper right corner of the bed.
Step 3. You will be pulling a stripe of ink on the round surface of the roller gauge. Pull the gauge underneath the form rollers so that a stripe of ink is transferred to the rounded surface of the gauge’s cylinder. Measure the stripe of the ink: you want your ink stripe to measure 3/32”. If the strip of ink is less than 1/16”, you’ll have difficulty consistently inking your plate (some areas will appear too light, and some areas will appear too dark). If your strip of ink is wider than 3/32”, your rollers put too much pressure on your plate and cause your printing to be chunky/blurry.
Step 4: On a platen press, to adjust the height of your form rollers: add tape to the rails that the roller trucks ride on. You may have to add several layers of tape. Strapping tape or plumber’s silver tape is frequently used for this. If you’re using a press other than a platen press, consult your manual as to how to raise your form rollers.
Step 5: Repeat steps three and four in each corner of your press bed.
Step 6: When your rollers are positioned correctly, you should pull identical 3/32” stripes of ink from the four corners of the press bed, and your printing should be both crisp and beautiful!
If you continue to notice inconsistencies in your inking after adjusting your roller height correctly, you may need to purchase new rollers and, if using a platen press, roller trucks as well.
Why do I have ink on my Boxcar Base?
It’s important to keep the grid on your Boxcar Base clean so you can see its registration marks when printing. If your rollers ever lay ink down directly on the base’s surface, STOP! STOP! STOOOOOOOOOOOOOP! Don’t keep running the press because something is out of alignment. Then ask yourself:
- Are your rollers at type-high? Using a roller gauge, check to make sure your rollers are set for type-high printing material. The surface of the base is far below type high and should never come into contact with the rollers.
- Is your base flat in the press bed? Take a piece of onionskin paper and try to slide it between the base and the press bed – if the onionskin paper fits, one of the corners of your base is working up in the press. Frequently this is caused by tightening the quoins too much. Since the Boxcar Base won’t work up as easily as handset metal type or monotype, you don’t need to tighten the quoins quite as hard.
Still getting ink on your base? If, after checking the roller height and loosening the quoins, you still have problems with ink on your base – contact us and we’ll assist you in problem-solving further.
Ideal Letterpress Shop
What do I need to be able to letterpress print with your photopolymer plates?
You’ll need:
- a printing base. The polymer plates we create aren’t type high by themselves. They need to be mounted on a base to make a type-high printing surface. We recommend our Boxcar Base system. Letterpress printers also use magnetic bases from Patmag or Bunting. If you are printing on a DIY press such as L Letterpress, please refer to this tutorial.
- a Printing press. Remember that most letterpress printing presses people purchase will not be ready to print beautifully right away and a little tender loving care will be needed. Be prepared to purchase new rollers or do other maintenance on your press!
- Ink. we recommend Van Son rubber-based letterpress inks, which you can order in any uncoated Pantone number! Or you can purchase the Van Son base colors and mix your own colors. View the inks we carry.
- various pressroom supplies, including printers furniture, quoins, tympan paper, type gauge, ink knife and (if using a platen press) Kort gauge pins or Henry gage pins.
- a fashionable printing apron
We now sell letterpress starter packs, which contain a lot of what you’ll need to get started.
What’s the biggest problem that printers new to photopolymer encounter?
Photopolymer plates offer an way to letterpress print extremely detailed designs with a deep heavy impression (or a kiss impression if you’re so inclined). The chief problem that new photopolymer users encounter usually deals with roller height/roller condition. But no worries! Unlike larger problems like war or global warming, roller issues do have concrete and relatively easy solutions. We recommend rubber rollers and, if using a platen press, solid trucks. If switching from lead type/magnesium plates, you’ll want to keep a much closer eye on your rollers. You may find our general printing FAQ’s useful, especially if you’ll be using a Boxcar Base.
What are roller gauges and why do I need them?
Roller gauges are especially indispensable with a platen press. Letterpress rollers need to be positioned just right in order to deposit a thin film of ink onto the surface of the form, without squeezing ink over the edges. A roller gauge will help you accurately measure the height of your rollers so you can produce the crispest printing that your press is capable of. We sell roller gauges, precision ground to type high, which are also very fashionable.
When your rollers are positioned correctly, your printing will look beautifully crisp. But if your rollers aren’t positioned at the right height, your printing will have a halo effect: dark around the edges and/or chunkier/blotchier than it should be. If you ever notice ink on the back of your polymer plate or on your base — it’s a roller gauge emergency! Adjust your rollers now! We have a great video on setting roller gauge height in our Boxcar Training Videos and step by steps are listed here.
Step 1. While your press is inked up, remove the chase (on platen presses) or the base (on a Vandercook).
Step 2. We recommend checking the roller height in the four corners of the press bed. We’ll start in the upper right hand corner. Engage the form rollers and position them over the upper right corner of the bed.
Step 3. You will be pulling a stripe of ink on the round surface of the roller gauge. Pull the gauge underneath the form rollers so that a stripe of ink is transferred to the rounded surface of the gauge’s cylinder. Measure the stripe of the ink: you want your ink stripe to measure 3/32”. If the strip of ink is less than 1/16”, you’ll have difficulty consistently inking your plate (some areas will appear too light, and some areas will appear too dark). If your strip of ink is wider than 3/32”, your rollers put too much pressure on your plate and cause your printing to be chunky/blurry.
Step 4: On a platen press, to adjust the height of your form rollers: add tape to the rails that the roller trucks ride on. You may have to add several layers of tape. Strapping tape or plumber’s silver tape is frequently used for this. If you’re using a press other than a platen press, consult your manual as to how to raise your form rollers.
Step 5: Repeat steps three and four in each corner of your press bed.
Step 6: When your rollers are positioned correctly, you should pull identical 3/32” stripes of ink from the four corners of the press bed, and your printing should be both crisp and beautiful!
If you continue to notice inconsistencies in your inking after adjusting your roller height correctly, you may need to purchase new rollers and, if using a platen press, roller trucks as well.
Plate Club
What is the Plate Club?
Plate Club is a new rewards program offered by Boxcar Press that provides a 5% discount for platemaking customers whose orders totaled more than 7,500 square inches in the past year. Eligible orders are for the period from January 1 to December 31st. If you ordered more than 7,500 square inches of processed plate material last year, you will automatically be enrolled in the Plate Club. Membership eligibility recalculates at the beginning of each calendar year (January 1st).
How do I see my growing total of square inches?
Click on your Account Page when logged into boxcarpress.com. There will be a section near the bottom of your account page called “Platemaking Usage”. This is where you can find the current tally of square inches plated (as well as a date of this accrual).
If I’m eligible for Plate Club, do I need to do anything?
No action is needed. The platemaking system is keeping track of your square inches. Your Plate Club discount is applied to your billing total on every job ticket for the year. No fuss, no muss.
How do I get my rewards from Plate Club
Your rewards and savings are automatic. This discount is applied to every order for the current year. The details page of your job ticket will reflect this discount with the dollar amount identified in your billing details. The type of discount – Plate Club – will be shown. Your emailed invoice will also have a line item with your Plate Club discount. All of your orders are also adding to your new square inch total for membership in the next year.