Six years working at a cozy letterpress shop– especially one that’s basking in sunny Pennsylvania — is going to create some nifty pieces and fine design. Or at least it will inspire an entire weekend devoted to the art of the letterpress, ala The Ladies of Letterpress conference. After working in Mainz, Germany for a half-year of traditional typesetting and printing before opening up shop (Thoma-Printers), Kseniya Thomas’s love of letterpress is founded on skill, encouragement, and a big scoop of care. Here, Kseniya weighs in on the letterpress community, printing adventures, and her love of miniatures.
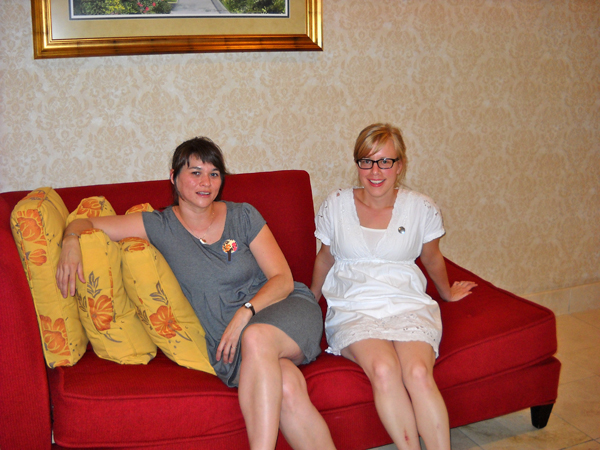
LIVE, WORK & DIRECT I’m Kseniya Thomas, and I’m a recovering English major from Salt Lake City. I currently live and work in Pennsylvania, where I’ve been happy to call myself a letterpress printer since 2005. I own Thomas-Printers, a commercial letterpress shop, and, with Jessica White of Heroes and Criminals Press, am the co-director of Ladies of Letterpress. I’m crazy for the Tour de France, old houses, running, newspapers, and anything in miniature.
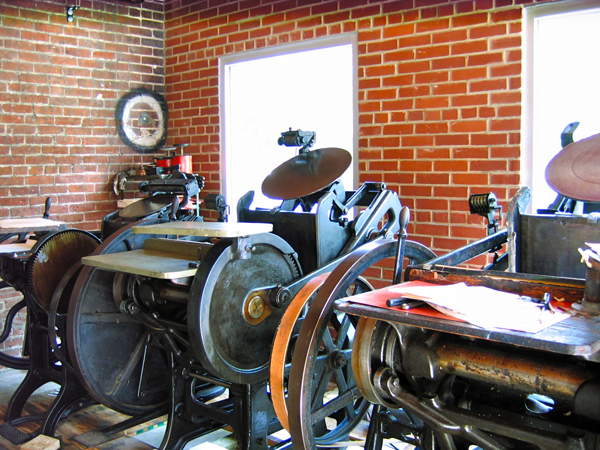
INSPIRED BY GUTENBERG After graduating from college, I had a fellowship to study and work in Germany for a year. A friend and I happened to go to Mainz one weekend (I loved movable type, but didn’t yet fully understand the implications!), where the Gutenberg Museum has a working letterpress print shop. I wrote and asked if they accepted interns, and they did, so I moved to Mainz. I worked there for six months, and learned how to set type and print from guys who had spent their whole careers in print shops as pressmen, stonemen, or compositors before offset printing edged them out.
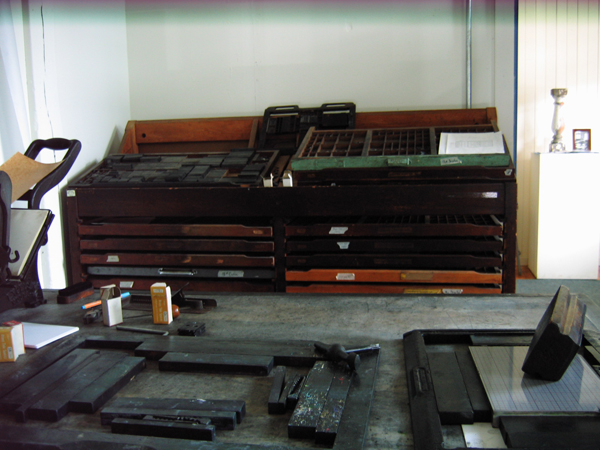
It was great: the shop has hundreds of lead typefaces, and I could print whatever I wanted. I also once printed a birth announcement for a princess, which was neat. I had no idea at the time that I had found my calling in life; even after I returned to the U.S., and realized that letterpress was happening here, I still only knew the basics of the history of printing and the craft of letterpress. And I knew nothing about running a small business!
A SUNNY SHOP My shop is located in the corner of an old shoe factory, with a room for shipping, receiving, and communications (ie, email), and a pressroom with a loading dock. The best thing about it is the tall, south-facing windows; in the summer, the only light I need is my color-correct lamp. I don’t think I’ll ever have another shop so sunny. It’s not decorated per se, except in a paper-stack, envelope-inventory, sample-shelf sort of way. It’s more workshop than showroom, so I don’t worry about hanging too much on the walls.
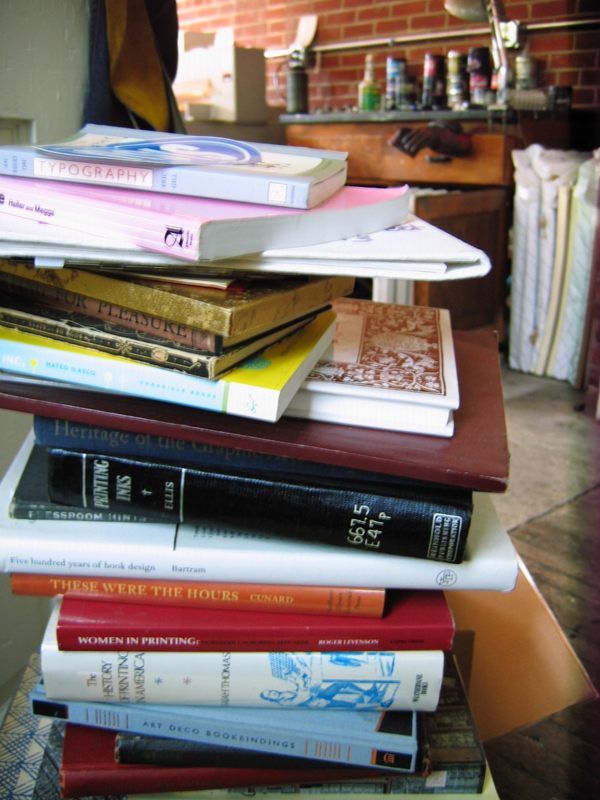
CARE FOR YOUR BUSINESS My best business advice is to learn to love your customers like family. They need care and attention just like family, and are the single thing, even more than hard work, that will keep you in business. Also, if you’re just starting out, don’t get caught up in playing catch-up with more established printers; there is no right way or one way to get where you want in this business, so your way is as likely to succeed as anyone else’s.
DESIGNED FOR PRINT I’m a printer who can design in a pinch, but I work with several great designers who can handle it when things get complicated. It’s nice being able to have designers who are familiar enough with the letterpress process that the finished product is going to print up great.
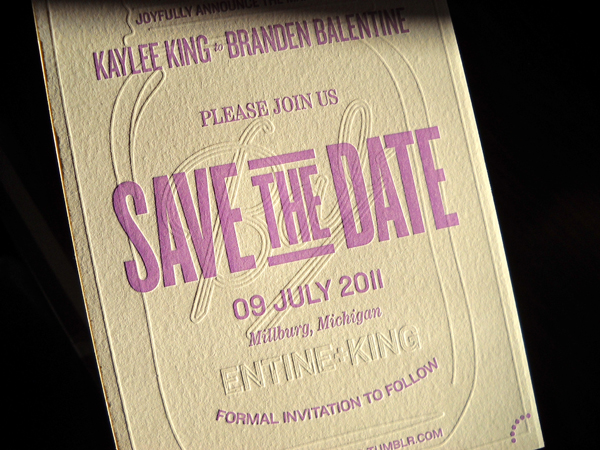
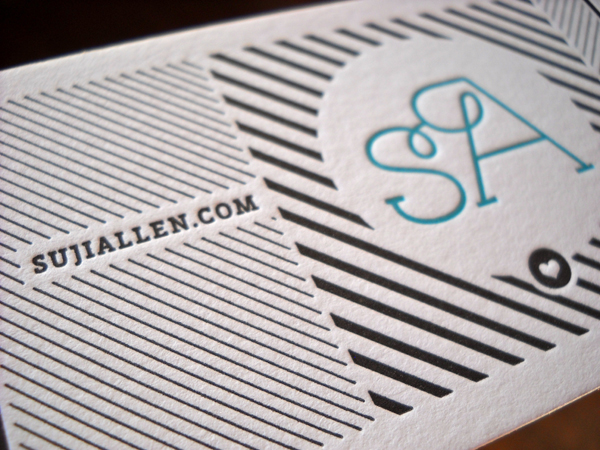
THE DAILY GRIND I do print full time. And when I’m not printing, I’m doing the 1000 other things a small business owner must do. Chief among them: worry, answer emails, write estimates, talk with clients, and a host of other pre-press, post-press, finishing, and ordering duties. Every day is different and yet comfortably similar, and now that I’ve been doing it full time for six years or so, I wouldn’t have it any other way.
ADVANCING A COMMUNITY I’m proud that Thomas-Printers is surviving the economy and doing well. Most recently, I’m proud of Jessica and I for organizing the best conference I’ve ever attended. The Ladies of Letterpress conference was such a happy, fun letterpress-fest, and it was thrilling to see so many ardent letterpress supporters and printers in one place.
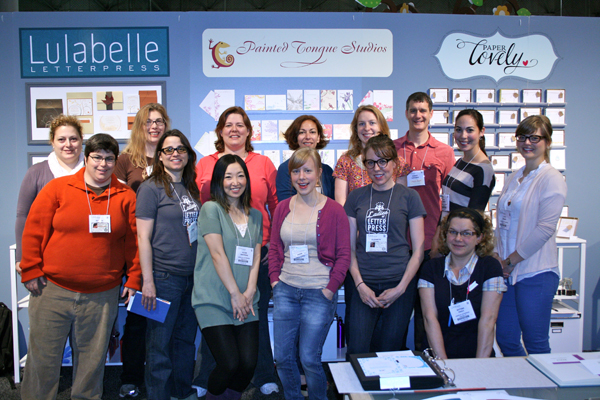
It was also encouraging to see that letterpress is still going strong, new people are starting to print every day, and people are loving what we make more than ever. I cannot wait for a repeat next year!
BOXCAR’S ROLE It’s not an exaggeration to say that, without Boxcar, neither Thomas-Printers nor Ladies of Letterpress would exist. I got my start setting type, but setting type for every client isn’t a good business model for me. So the Boxcar Base is as important and valuable a tool as the press itself. Aside from the base and plates, Boxcar is the friendliest, fastest, nicest supplier I work with; the positive attitude and enthusiasm of the owners and staff has in turn contributed to the good-feeling and camaraderie in the letterpress community.
PRESS HISTORY My first press was a 12×18 Chandler & Price that I bought from Bill Welliver through the Letpres listserv. I used it for everything, large and small, for almost three years, until I bought a 10×15 C&P that allegedly only had had one owner and then sat in storage for 30 years. I also have a treadle-powered 8×12, which is handy when the power goes out. C&Ps are great presses, simple to use and relatively readily available, and are capable of a lot of fine work.
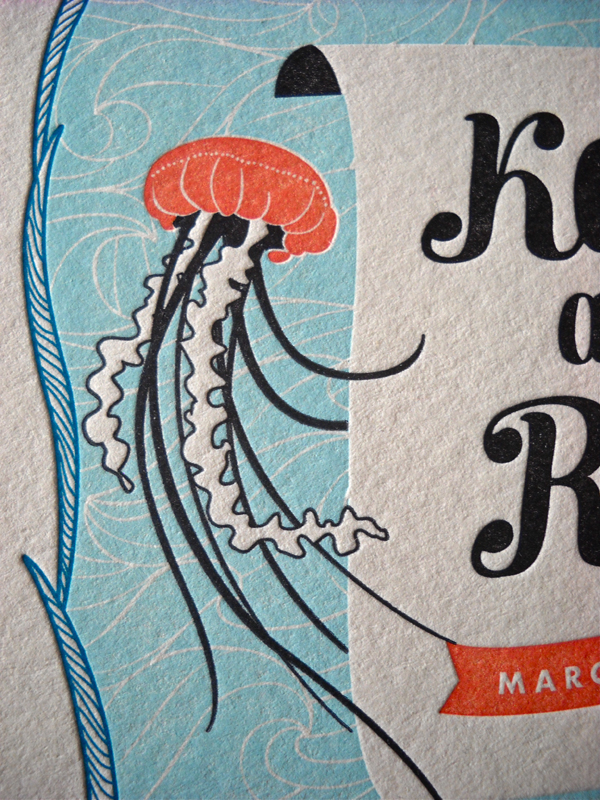
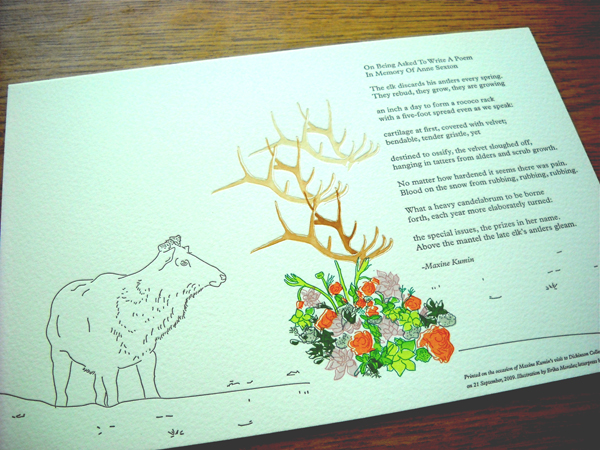
WHAT’S NEXT Ladies of Letterpress will be at the 2012 National Stationery Show for a third year with a new, super, wonderful, talented group of printers. And the second-annual LOLP conference is happening again-stay tuned for more details.
We’d like to give bigs thanks to Kseniya for taking the time to give us the scoop on Thomas Printers!